Magnetic force driving mechanism for valve
A magnetic drive and valve technology, applied to engine components, valve operation/release devices, valve details, etc., can solve problems such as low safety, leakage, and production impact, and achieve the effect of improving production efficiency
- Summary
- Abstract
- Description
- Claims
- Application Information
AI Technical Summary
Problems solved by technology
Method used
Image
Examples
Embodiment Construction
[0008] Such as figure 1 , 2 Shown: 9 is valve stem, is supported in the left end disk 6 by bearing, and left end disk 6 is fixedly connected with left bearing cover 13 by bolt. The left end plate 6 is connected to the right end plate 1 through the connecting sleeve 4, and the connecting sleeve 4, the left end plate 6 and the right end plate 1 are all fixedly connected by bolts. On the right end plate 1, the outer magnet cylinder 3 located inside the connecting sleeve 4 is supported by bearings, the shaft end of the outer magnet cylinder 3 protrudes to the outside of the right end plate 1, and the right end plate 1 is fixedly connected with a bolt with a right bearing cover 10 . There is an inner rotor 5 keyed to the valve stem 9 inside the outer magnet cylinder 3 , and a nut is provided at the end of the valve stem 9 for axially limiting the inner rotor 5 . An isolation cover 2 fixedly connected with the left end disk 6 is provided between the inner rotor 5 and the outer ma...
PUM
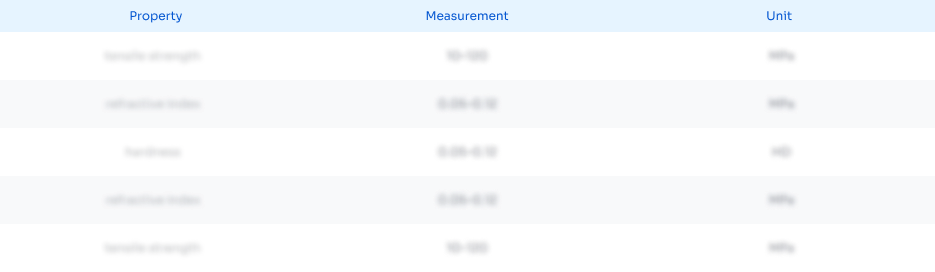
Abstract
Description
Claims
Application Information

- Generate Ideas
- Intellectual Property
- Life Sciences
- Materials
- Tech Scout
- Unparalleled Data Quality
- Higher Quality Content
- 60% Fewer Hallucinations
Browse by: Latest US Patents, China's latest patents, Technical Efficacy Thesaurus, Application Domain, Technology Topic, Popular Technical Reports.
© 2025 PatSnap. All rights reserved.Legal|Privacy policy|Modern Slavery Act Transparency Statement|Sitemap|About US| Contact US: help@patsnap.com