A real-time motion planning method for robots based on force feedback
A motion planning, robotics technology, applied in manipulators, program-controlled manipulators, manufacturing tools, etc., can solve the problems of not considering the rated torque constraint of the manipulator, motion shock, failure shutdown, etc., to improve the quality of processing and assembly, smooth acceleration, eliminate Effects of Data Acquisition Noise
- Summary
- Abstract
- Description
- Claims
- Application Information
AI Technical Summary
Problems solved by technology
Method used
Image
Examples
Embodiment Construction
[0049] A real-time motion planning method for robots based on force feedback. Aiming at the problem that the mechanical arm cannot move smoothly in the case of large periodic attitude corrections, the existing piecewise linear force-position control method is corrected, such as figure 1 As shown, the specific steps are:
[0050] (1) Use a six-dimensional force sensor for data collection, and obtain the component forces f of the X, Y, and Z axes in the base coordinate system of the manipulator after gravity compensation and coordinate transformation X , f Y , f Z , and according to the component force f X , f Y , f Z Obtain the external force f in the base coordinate system of the manipulator;
[0051] Wherein, the coordinate system of the six-dimensional force sensor coincides with the X and Y axes of the tool coordinate system of the manipulator respectively, and the calculation method of the external force is: subtract the load gravity at the end of the manipulator from...
PUM
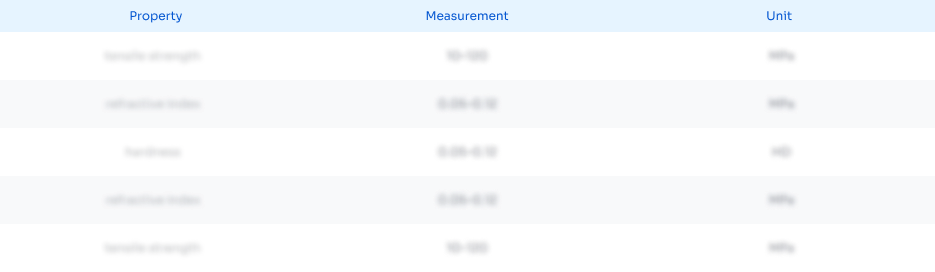
Abstract
Description
Claims
Application Information

- Generate Ideas
- Intellectual Property
- Life Sciences
- Materials
- Tech Scout
- Unparalleled Data Quality
- Higher Quality Content
- 60% Fewer Hallucinations
Browse by: Latest US Patents, China's latest patents, Technical Efficacy Thesaurus, Application Domain, Technology Topic, Popular Technical Reports.
© 2025 PatSnap. All rights reserved.Legal|Privacy policy|Modern Slavery Act Transparency Statement|Sitemap|About US| Contact US: help@patsnap.com