A Method of Suppressing Residual Vibration at the End of Servo System Based on Model Tracking Control
A technology of servo system and residual vibration, applied in general control system, control/adjustment system, program control, etc., can solve the problems of poor vibration suppression effect of input shaper and slow vibration suppression speed, etc.
- Summary
- Abstract
- Description
- Claims
- Application Information
AI Technical Summary
Problems solved by technology
Method used
Image
Examples
Embodiment Construction
[0071] In order to have a clearer understanding of the technical features, purposes and effects of the present invention, the specific implementation manners of the present invention will now be described in detail with reference to the accompanying drawings.
[0072] Embodiments of the present invention provide a method for suppressing residual vibration at the end of a servo system based on model tracking control.
[0073] Please refer to figure 1 , figure 1 It is a flowchart of a method for suppressing residual vibration at the end of a servo system based on model tracking control in an embodiment of the present invention; specifically, it includes the following steps:
[0074] S101: Modeling the servo system to obtain an ideal model of the servo system; the servo system is a servo system with an elastic connection device;
[0075] S102: Calculate and obtain the system natural frequency and damping ratio of the servo system according to the ideal model;
[0076] S103: ...
PUM
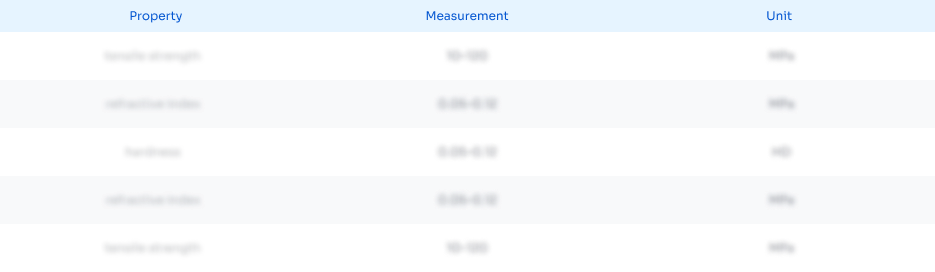
Abstract
Description
Claims
Application Information

- R&D
- Intellectual Property
- Life Sciences
- Materials
- Tech Scout
- Unparalleled Data Quality
- Higher Quality Content
- 60% Fewer Hallucinations
Browse by: Latest US Patents, China's latest patents, Technical Efficacy Thesaurus, Application Domain, Technology Topic, Popular Technical Reports.
© 2025 PatSnap. All rights reserved.Legal|Privacy policy|Modern Slavery Act Transparency Statement|Sitemap|About US| Contact US: help@patsnap.com