A steam purging tail gas treatment process and complete set of equipment
A technology for exhaust gas treatment and complete set of devices, applied in the direction of vapor condensation, separation method, dispersed particle separation, etc., can solve the problems of unusable electric heaters, unrecyclable pollutants, no movable treatment devices, etc., and achieves explosion-proof level. Improve and solve the problem of exhaust emission control and the effect of convenient installation and maintenance
- Summary
- Abstract
- Description
- Claims
- Application Information
AI Technical Summary
Problems solved by technology
Method used
Image
Examples
Embodiment 1
[0103] Treatment of refinery hexene production units, raw material storage tanks and waste oil storage tanks steam purge tail gas, steam purge tail gas composition (volume fraction) water vapor 78%, nitrogen 14%, hydrocarbons 8%. Hydrocarbons mainly include alkanes, olefins and a small amount of aromatics and halogenated hydrocarbons. The total gas flow rate is 400~500m 3 / h, the operating conditions of the membrane module and low-temperature catalytic oxidation are shown in Table 1 below, and the process results are shown in Table 2:
[0104] Table 1, Device Operating Conditions
[0105]
[0106]
[0107] Table 2, process treatment results (gas composition and concentration in each section)
[0108]
Embodiment 2
[0110] Treatment of steam purge tail gas after shutdown of catalytic cracking unit and waste oil storage tank in refinery. The steam purge tail gas composition (volume fraction) is 68% water vapor, 19% nitrogen, and 13% hydrocarbons. Hydrocarbons mainly include alkanes, olefins, aromatics, ethers, and halogenated hydrocarbons, as well as sulfur-containing components such as hydrogen sulfide and mercaptans. The total gas flow is 200~400m 3 / h, process parameters such as temperature, pressure, and flow of the membrane module and low-temperature catalytic oxidation are shown in Table 1 below, the total gas composition, total non-methane hydrocarbons and the concentration of representative components, and the process treatment results are shown in Table 2:
[0111] Table 1, Device Operating Conditions
[0112]
[0113]
[0114] Table 2, process flow processing results (gas composition and concentration in each section)
[0115]
PUM
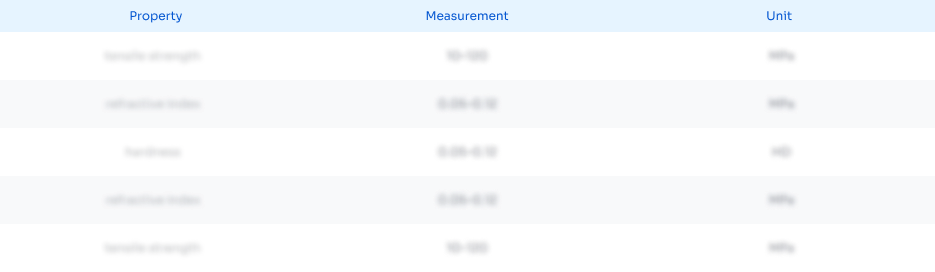
Abstract
Description
Claims
Application Information

- R&D
- Intellectual Property
- Life Sciences
- Materials
- Tech Scout
- Unparalleled Data Quality
- Higher Quality Content
- 60% Fewer Hallucinations
Browse by: Latest US Patents, China's latest patents, Technical Efficacy Thesaurus, Application Domain, Technology Topic, Popular Technical Reports.
© 2025 PatSnap. All rights reserved.Legal|Privacy policy|Modern Slavery Act Transparency Statement|Sitemap|About US| Contact US: help@patsnap.com