
Introduction to Shell and Tube Heat Exchangers
A shell and tube heat exchanger is commonly used in many industries. Their robust design and versatility make them highly efficient. These devices consist of a large pressure vessel, known as the shell, containing a bundle of tubes. One fluid flows through the tubes, while another flows around them within the shell. Heat transfers between the two fluids through the tube walls. This article will explore how shell and tube heat exchangers work, their benefits, and common applications.
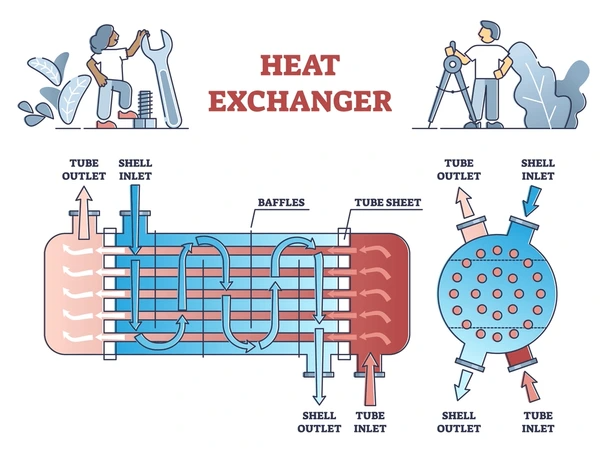
Shell and Tube Heat Exchangers Work Principal
A shell-and-tube heat exchanger transfers heat between two fluids: one flows through the tubes, the other around them. The tube walls separate the fluids, preventing mixing while allowing heat transfer. Heat moves through conduction and convection. Typically, the system consists of a cylindrical shell enclosing a bundle of tubes. Fluids enter and exit through specific nozzles. This article will explain how this system works and its common applications in various industries.
Key Components of a Shell and Tube Heat Exchanger
- Shell: The outer cylindrical vessel that houses the tube bundle. It provides the space for the shell-side fluid to flow over the tubes.
- Tube Bundle: A collection of tubes through which the tube-side fluid flows. The tubes can be plain or enhanced with fins to increase the heat transfer area.
- Tube Sheets: Plates to which the tubes are fixed at both ends. They prevent the mixing of the shell-side and tube-side fluids.
- Baffles: Plates installed inside the shell to direct the flow of the shell-side fluid across the tubes multiple times, enhancing heat transfer by inducing turbulence.
- Inlet and Outlet Nozzles: Openings for the entry and exit of fluids on both the shell side and the tube side.
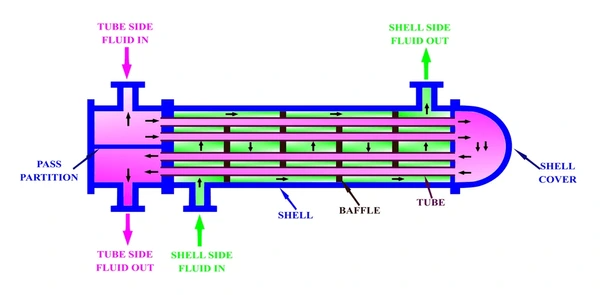
Shell and Tube Heat Exchanger vs. Plate Heat Exchanger
Structural Design
STHEs: Shell-and-tube heat exchangers consist of tubes within a cylindrical shell. One fluid flows through the tubes, and another flows around them. Tubes can be plain or finned to enhance heat transfer. Baffles direct the flow, increasing turbulence for better efficiency.
PHEs: Plate heat exchangers are made of corrugated plates stacked together, forming parallel flow channels. Fluids alternate between the plates in a counter-current arrangement. Plates are sealed with gaskets or welds, depending on the requirements.
Heat Transfer Efficiency
STHEs: Shell-and-tube heat exchangers generally have lower heat transfer efficiency due to the larger surface area required. However, they excel in high-pressure environments and can handle a broad range of temperatures.
PHEs: Plate heat exchangers are more efficient, with heat transfer coefficients three to four times higher than STHEs. Their increased surface area and turbulence allow for a more compact and cost-effective design, requiring less coolant.
Maintenance and Fouling
STHEs: Maintenance is more complex in shell-and-tube designs due to the intricate tube bundle and fouling risks. Despite this, they are durable and resistant to corrosion, making them suitable for harsh industrial environments.
PHEs: Plate heat exchangers are easier to maintain due to their modular design, which allows for quick disassembly. The turbulence within the plates reduces fouling, but gaskets may need replacing more often to maintain performance.
Benefits of Using Shell and Tube Heat Exchangers
High Pressure and Temperature Handling:Their robust design allows them to operate under extreme pressures and temperatures, ideal for demanding industries.
Versatility:They can handle various fluids, including liquids, gases, and two-phase mixtures, with different flow arrangements.
Ease of Maintenance:Their design allows for easy disassembly and cleaning, addressing fouling and scaling issues in many industries.
Customization:They can be tailored with different tube configurations and materials to meet specific process needs.
Cost-Effectiveness:Despite their complexity, they are affordable to build and operate, offering a long service life and efficiency.
Applications of Shell and Tube Heat Exchangers
Chemical Processing: They play a crucial role in heating, cooling, condensation, and evaporation. These are key in distillation and solvent recovery.
Power Generation: In power plants, they improve thermal efficiency by serving as feedwater heaters, condensers, and pre-heaters.
Oil and Gas: In refineries, they manage thermal energy during crude oil heating, gas cooling, and product fractionation.
HVAC Systems: They regulate temperatures in both residential and commercial heating, ventilation, and air conditioning systems.
Pharmaceuticals: Essential for maintaining precise temperatures in drug production and pharmaceutical manufacturing.
Food and Beverage: Used in pasteurization and sterilization to ensure product safety and maintain quality.
Cryogenics: They are vital in low-temperature processes, such as liquefied natural gas (LNG) processing and storage.
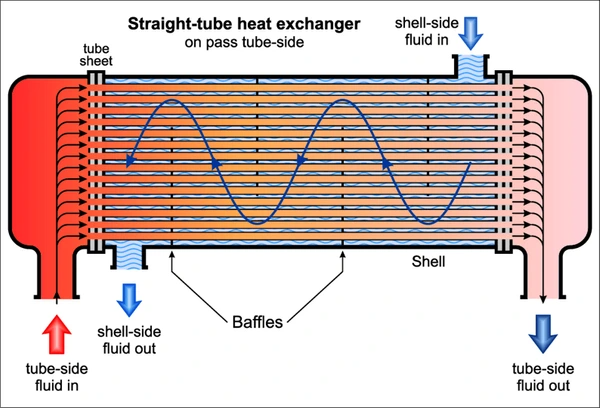
Latest Technical Innovations in Shell and Tube Heat Exchangers
1. Heat Transfer Enhancement Techniques
Recent advancements have focused on improving heat transfer efficiency. Traditional methods, like altering geometric parameters (e.g., diameter, tube count), have been well-studied. A promising innovation is nanofluids (NFs), which are suspensions of nanoparticles in base fluids like water or oil. These fluids boost the thermophysical properties, leading to better heat transfer rates. Though challenges like higher viscosity and pressure drops exist, ongoing research is optimizing these issues to maximize efficiency.
2. Structural Innovations
Several structural changes have been introduced to improve performance. For example, helical baffles enhance heat transfer while reducing pressure drops. This design allows smoother flow and better space utilization, reducing vibration impacts. Foam heat transfer units, such as graphite foam, also improve heat transfer and offer cost-effectiveness and corrosion resistance.
3. Advanced Materials
Material selection is crucial for performance and durability. Superalloys like Haynes 282, known for their high creep strength, are ideal for high-temperature and high-pressure applications. Additionally, microtube exchangers (MT-STHXs), with smaller inner diameters, offer compact designs and high power densities, making them increasingly popular.
4. Innovative Design Methodologies
Innovative design methods are enhancing heat exchanger efficiency. Perforated plates in the tube space improve heat transfer and reduce hydraulic resistance by distributing the heat-transfer fluid evenly. Staggered nozzle arrangements also improve performance by ensuring uniform fluid distribution, further enhancing heat transfer.
5. Experimental and Computational Studies
Experimental studies have validated the performance of new designs and materials. For instance, injecting air bubbles into fluid flow increases turbulence and boosts heat transfer by 25-40%. Computational studies, like Computational Fluid Dynamics (CFD), provide detailed insights into the temperature and flow fields, helping refine and optimize designs.
6. Energy Efficiency and Sustainability
Energy efficiency and sustainability are key in new heat exchanger technologies. Innovations focus on reducing energy consumption and costs. Advanced materials and design tweaks improve heat transfer while minimizing pressure drops. Thinner tubes have proven effective, increasing heat transfer rates while keeping the design compact and sustainable.
To get detailed scientific explanations of Shell and Tube Heat Exchangers, try Patsnap Eureka.
