
What is A Roller Conveyor?
A roller conveyor is a type of material handling equipment that uses a series of rollers mounted on bearings to transport unit loads. These rollers are fixed at specific intervals on two side frames, which are supported by stands or trestles placed on the floor. The primary function of a roller conveyor is to convey materials by the movement of its components, while the equipment itself remains stationary. Roller conveyors are typically used for unit loads with at least one rigid, near-flat surface to maintain stable equilibrium on the rollers, such as ingots, plates, rolled stock, pipes, logs, boxes, and crates.
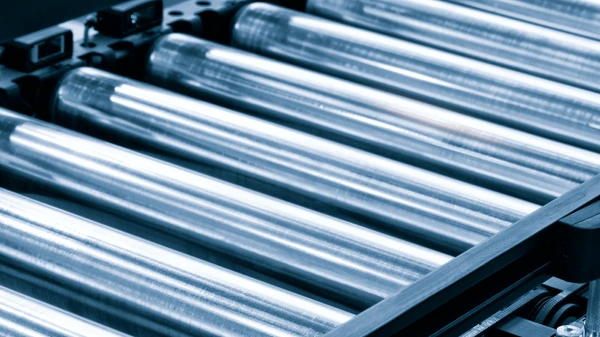
Key Components of a Roller Conveyor System
- Rollers: The primary load-bearing and driving components, which can vary in diameter and spacing depending on the size and type of load.
- Side Frames: Structural elements that support the rollers and maintain the integrity of the conveyor system.
- Bearings: Mechanisms that allow the rollers to rotate smoothly.
- Stands or Trestles: Supports that elevate the side frames and rollers off the ground.
- Drive Mechanism: Can include motorized rollers or external drive units to power the movement of the rollers.
Types of Roller Conveyors
- Gravity Roller Conveyors: Utilize the force of gravity to move materials down an incline.
- Powered Roller Conveyors: Use motors to drive the rollers, allowing for controlled movement of materials.
- Accumulation Roller Conveyors: Designed to allow materials to accumulate at specific points without causing damage or excessive pressure.
- Line Shaft Roller Conveyors: Feature a single drive shaft that powers multiple rollers via belts or bands.
How Roller Conveyors Work
- Material Placement: Materials are placed on the rollers, which are arranged in parallel between the conveyor frames.
- Roller Rotation: In powered systems, motors drive the rollers via a driving force receiver. The rollers rotate, creating a frictional force that moves the materials along the conveyor path.
- Conveyance Control: The speed and direction of the rollers can be controlled to manage the flow of materials. This is particularly important in applications where precise handling and positioning of materials are required.
- Accumulation and Sorting: Some roller conveyors are equipped with sensors and control systems that allow for the accumulation and sorting of materials. These systems can stop and start the rollers as needed to manage the flow and ensure that materials are conveyed to the correct destination.
Benefits of Roller Conveyors
- Efficiency: They provide a continuous and efficient means of transporting goods, reducing manual handling and increasing throughput.
- Flexibility: Roller conveyors can be customized to fit various layouts and can handle a wide range of product sizes and weights.
- Durability: Designed to withstand heavy loads and harsh conditions, making them suitable for industrial applications.
- Cost-Effectiveness: They have lower operational costs compared to other conveyor systems due to their simple design and ease of maintenance.
- Scalability: Easily expandable by adding more rollers or sections to accommodate increased production demands.
Challenges and Maintenance of Roller Conveyors
- Noise: Metal rollers and bearings can generate significant noise, particularly as the bearings wear over time.
- Frequent Maintenance: Regular lubrication, tightening, and repairs are necessary to maintain optimal performance and prevent breakdowns.
- Wear and Tear: Components such as rollers, bearings, and drive mechanisms are subject to wear and tear, necessitating periodic replacement to avoid operational disruptions.
- Complexity in Advanced Systems: Roller conveyors with advanced features like linear motors or integrated control systems may require specialized maintenance and troubleshooting skills.
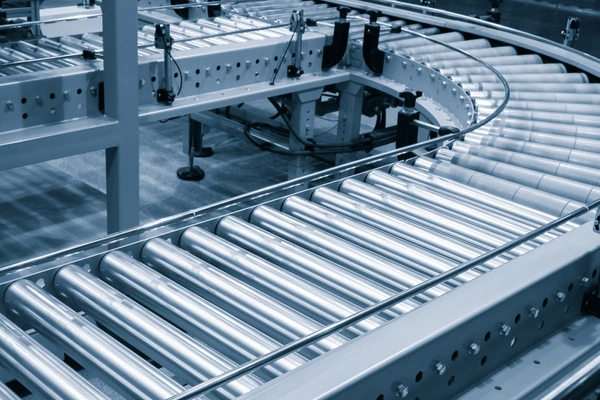
Applications of Roller Conveyor
Manufacturing Industry
Roller conveyors are integral to manufacturing processes, particularly in metalworking and forming environments. They facilitate the transfer of bulk metal materials such as ingots, billets, or coils through various stages of melting, annealing, tempering, quenching, hardening, or rolling processes. These conveyors help in manipulating the size, shape, chemical, and mechanical properties of the materials being worked on. However, challenges such as metal-on-metal contact can lead to slippage and unintended motion, causing deformities or blemishes on the materials.
Warehousing and Distribution
In warehousing and distribution centers, roller conveyors are used to move products through facilities, past various operations, and to different destinations. They are often part of accumulator conveyor systems, which allow for live storage and accumulation of loads. These systems are crucial in managing the flow of products, ensuring that orders are processed efficiently and ready for shipment as a group. For example, in beverage distribution facilities, individual beverage products are fed onto a main line and packaged together for shipment.
Packaging and Assembly Lines
Roller conveyors are widely used in packaging and assembly lines for transporting goods, packaging materials, and other items. They are particularly useful in environments where products need to be moved from loading stations to consumption stations. The flexibility to adjust the length and type of rollers allows these conveyors to adapt to changes in production volumes and new product introductions.
Food Processing Industry
In the food processing industry, roller conveyors are employed to transport food products through various stages of processing and packaging. They are designed to withstand contamination and are often made from materials that are easy to clean and maintain. However, steel rollers can be problematic due to their thermal and electrical conductivity, making them unsuitable for certain environments. Alternatives such as polymer concrete rollers have been proposed to address these issues, although they have not seen widespread adoption.
Automotive Industry
In the automotive industry, roller conveyors are used to transport heavy equipment and semi-finished products like machinery parts. These conveyors are designed to handle the weight and size of automotive components, ensuring smooth and efficient transfer between different stages of production. The ability to control the direction and speed of the rollers is crucial in managing the flow of materials in automotive assembly lines.
Glass Manufacturing
In glass manufacturing, roller conveyors are used to transport delicate glass products. Specially designed L-type bi-directional roller conveyors can move glass in perpendicular directions without rotating it, ensuring that the orientation and direction of the glass remain unchanged. This is particularly important in preventing damage to the glass during transportation.
Logistics and Material Handling
Roller conveyors are essential in logistics and material handling for moving goods along predetermined paths. They are used to convey pallets, boxes, and other containers in intralogistic applications. The design of roller conveyors allows for straight or curved conveying directions, making them versatile for various logistical needs. The ability to control the conveying action of multiple goods on the rollers enhances their efficiency in material handling operations.
Agricultural Sector
In the agricultural sector, roller conveyors are used to transport products such as root crops, grains, and fodder mixtures. These conveyors can move products in horizontal, sloping, and vertical directions, making them suitable for various agricultural applications. They can also perform additional functions such as mixing products, dispensing materials, and separating impurities.
Application Cases
Product/Project | Technical Outcomes | Application Scenarios |
---|---|---|
Loading Table Roller Brush Assembly Osborn LLC | Supports various outer radial dimensions of transport rollers, enhancing versatility and ease of maintenance. | Used in material transport systems where different sizes of rollers are required, such as in manufacturing and packaging industries. |
Telescopic Roller Conveyor FlexQube AB | Provides telescopic functionality, allowing for adjustable length and easy integration into existing systems. | Ideal for flexible material handling in warehouses and distribution centers where space optimization is crucial. |
Conveyor Roller with Integral Clutch Mhs Conveyor Corp. | Offers cost-effective and reliable operation with convenient and efficient control. | Suitable for packaging and transportation industries where precise control of material flow is necessary. |
Roller Conveyor for Reverse Vending Machine Aalto University Foundation | Quick-release mechanism for easy module replacement and maintenance. | Used in reverse vending machines for efficient handling and sorting of recyclable materials. |
Conveyor Belt with Rollers and Switch Conveyor Laitram LLC | Allows for selective propulsion of conveyed articles in different directions, enhancing sorting capabilities. | Applicable in automated sorting systems in logistics and distribution centers for efficient material handling. |
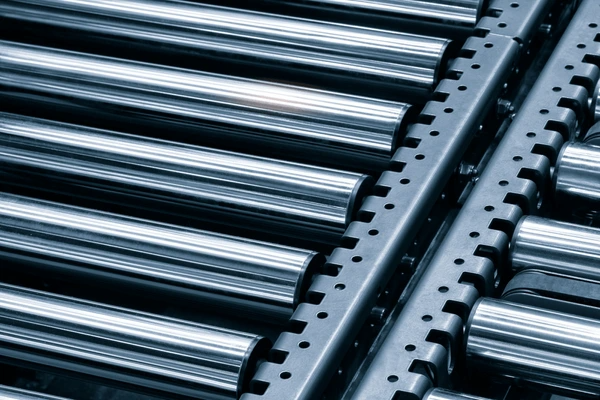
Latest Technical Innovations in Roller Conveyor
Innovations in Roller Conveyor Design
- Switch Conveyor Systems: Recent innovations include the development of switch conveyors that can divert conveyed articles without the shortcomings of traditional shoe sorters or roller conveyors. These systems utilize a conveyor belt with rollers arranged in alternating first and second lanes, which can be selectively moved into and out of contact with the belt to direct the flow of items. This design reduces noise and maintenance requirements associated with metal conveyors.
- L-type Bi-directional Roller Conveyors: A novel design for transporting delicate materials like glass involves L-type bi-directional roller conveyors. These systems are designed to move glass at a 90-degree angle without rotating it, ensuring safe handling and transportation within manufacturing sectors.
Material Innovations
- Composite Shaftless Rollers: One significant advancement is the development of lightweight composite idler rollers. These rollers are designed to reduce the overall weight by approximately 47% compared to traditional steel rollers, enhancing the strength-to-weight ratio and performance of the conveyor system. This innovation is particularly beneficial for long belt conveyors used in industries like mining, where reducing the weight of thousands of rollers can lead to substantial efficiency gains.
Mechanical and Structural Enhancements
- Integral Clutch Mechanism: Roller conveyors now incorporate integral clutch mechanisms that allow rollers to slip relative to the drive system. This feature is particularly useful in accumulator conveyor systems, where it enables controlled accumulation and release of products, improving the efficiency of material handling in manufacturing and distribution facilities.
- Modular Conveyor Belts: Another innovation is the use of modular conveyor belts with integrated rollers and switch mechanisms. These belts consist of rows of belt modules connected end-to-end at hinges, with rollers that can extend above and below the belt. The switch mechanism can selectively contact different groups of rollers to control their rotation, providing greater flexibility and control over the conveyor system.
Control and Automation
- Dual-Zone Configuration: Modern roller conveyors feature advanced control systems that allow for dual-zone configurations. These systems can selectively drive different sections of the conveyor independently, optimizing the transportation path based on real-time data. This capability is enhanced by the integration of imaging devices that capture object data and adjust the conveyor’s operation accordingly.
Noise Reduction and Maintenance
- Noise Reduction Techniques: Innovations aimed at reducing the noise generated by roller conveyors include the use of quieter materials and improved bearing designs. These advancements address the common issue of noisy metal conveyors, especially as their bearings wear over time, and reduce the need for frequent maintenance operations such as lubricating and tightening.
Energy Efficiency
- Heat Sink Integration: Some roller conveyors now feature rollers with integrated heat sinks. This design helps dissipate heat generated during operation, improving the longevity and reliability of the conveyor system. The heat sink integration is particularly beneficial in high-throughput environments where continuous operation can lead to significant heat buildup.
To get detailed scientific explanations of roller conveyors, try Patsnap Eureka.

Learn more
Shock Cords: Versatile Strength for Every Need
Pressure Switches: Small Devices, Big Impact
Unveiling The Lead Screw: Its Mechanism, Benefits, And Beyond