
What is the RB Engine?
The RB Engine, or Reciprocating Piston Engine, is a widely recognized type of internal combustion engine that has powered transportation for over a century. Known for its reliability and versatility, the RB engine has evolved beyond traditional use, with its potential for alternative applications such as chemical production gaining attention. The concept of using internal combustion engines as chemical reactors dates back to 1910, when Hausser first demonstrated their ability to produce nitric oxide and nitric acid. Since then, various industries and research groups have explored the RB engine’s broader capabilities, making it a subject of ongoing innovation and interest. This article will delve into the history, features, and applications of the RB engine, offering insights into its enduring relevance.
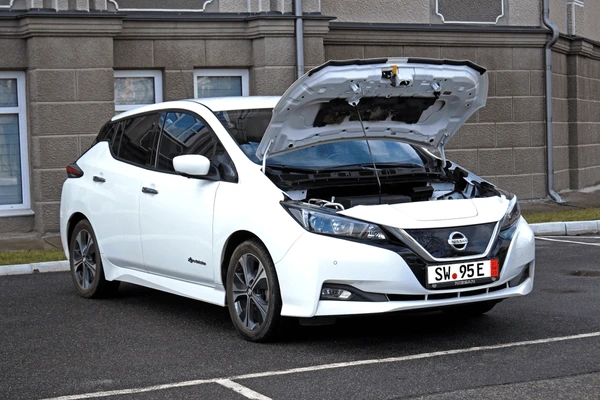
The Evolution of the RB Engine
Technological Advancements
- Turbocharging: The introduction of turbocharging in models like the RB26DETT significantly increased power output and efficiency. Turbocharging allowed for higher air intake and combustion efficiency, leading to improved performance metrics.
- Variable Valve Timing (VVT): The implementation of VVT technology in later models enhanced the engine’s efficiency and power delivery by optimizing valve timing for different engine speeds and loads.
- Advanced Fuel Injection Systems: The evolution from mechanical to electronic fuel injection systems enabled more precise fuel delivery, improving combustion efficiency and reducing emissions.
Performance Improvements
- Power Output: The power output of the RB engine series has seen substantial increases. For instance, the RB26DETT engine, used in the Nissan Skyline GT-R, produced up to 276 horsepower in its stock form, with potential for much higher outputs with modifications.
- Torque: Enhancements in turbocharging and fuel injection have also improved torque delivery, providing better acceleration and overall driving dynamics.
- Efficiency: The introduction of technologies like VVT and advanced fuel injection has not only improved power and torque but also enhanced fuel efficiency and reduced emissions.
Key Design Changes
- Cylinder Head Design: The evolution of the cylinder head design, including the use of lightweight materials and optimized combustion chamber shapes, has contributed to better airflow and combustion efficiency.
- Block Construction: The use of high-strength materials and improved casting techniques has enhanced the durability of the engine block, allowing it to withstand higher power outputs and stresses.
- Cooling Systems: Advances in cooling system design, including more efficient water and oil cooling pathways, have helped manage the increased thermal loads associated with higher performance levels.
Nissan Models Equipped with RB Engines
- Nissan Skyline (R31, R32, R33, R34):
The Nissan Skyline GT-R models, particularly the R32, R33, and R34, are renowned for their RB26DETT engine. This 2.6L twin-turbo inline-six delivers impressive power and is highly regarded for tuning potential. - Nissan Cefiro (A31):
The A31 Cefiro featured the RB20DET engine, a 2.0L turbocharged inline-six. It strikes a balance between performance and practicality. - Nissan Laurel (C33, C34, C35):
The Nissan Laurel models, including the C33, C34, and C35, were equipped with RB20DET and RB25DET engines. These engines combined luxury with strong performance. - Nissan Stagea (WC34):
The Stagea, known as the “Skyline Wagon,” featured the RB25DET engine. It offered powerful performance in a versatile, spacious station wagon.
RB Engine vs SR Engine
Key Performance Differences
- RB Engine:
This engine features a jump transition from 1RB to 81RB, with a difference of 20.08 +/- (5 + TT), where TT = 0.7. The range is between 14.38 and 25.78. Performance follows specific patterns, with starting power at 17.75 dBm. A decrease occurs at TPC = -1 dB, with worst-case limits from -6.7 to 6.7 and -0.4 to 2.4 for the third worst point. - SR Engine:
Jump transitions for this engine aren’t detailed, but they likely differ from the RB model. Direct comparisons are needed to fully understand the performance.
Advantages and Disadvantages
RB Engine
Advantages:
- Wide Transition Range: The engine handles a broad range of transitions, offering flexibility across different conditions.
- In-Depth Performance Data: Detailed sub-test results provide clear insights, helping optimize engine performance.
Disadvantages:
- Complex Control: The variability in transitions may require advanced control systems to maintain stability.
SR Engine
Advantages:
- Simplified Control: Fewer transition variations may make the engine easier to control and more stable.
- Optimized for Specific Uses: The engine may excel in particular applications, providing better performance in those scenarios.
Disadvantages:
- Limited Flexibility: A smaller transition range may make it less adaptable to varying operational conditions.
Primary Applications
- RB Engine:
Thanks to its flexibility, this engine is ideal for high-performance applications. It’s well-suited for computing, telecommunications, and advanced automotive systems. - SR Engine:
The SR engine is better for specialized applications, such as industrial machinery and specific communication systems, where stability is key.
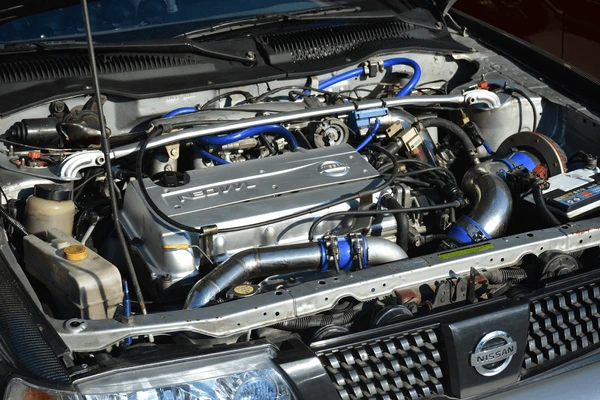
Applications of RB Engine
Flexible Electronics and Health Monitoring
- Flexible Electronics:
RB composites are ideal for flexible electronics due to their durability and resistance to environmental factors. These materials are used in wearable devices, where flexibility is crucial. - Health Monitoring:
In healthcare, RB composites power flexible sensors and devices that conform to the body. These devices provide continuous and accurate health data collection.
Physical Therapy and Rehabilitation
- Therapeutic Devices: RB composites’ flexibility and strength make them perfect for physical therapy devices. They adapt to patients’ movements, offering effective and comfortable therapy.
Automotive Industry
- Engine Components: RB composites are used in automotive engine parts, where durability and resistance to corrosion are essential. This improves component lifespan and performance.
- Robotic Applications: The RB20 model automates the grinding of automotive cylinder blocks, excelling in precision and repetitive tasks in manufacturing environments.
Medical Device Manufacturing
- Component Polishing: RB20 robots polish medical device components, ensuring high precision and a smooth surface finish. This is critical for medical applications.
Foam Sculpting and Printing
- Foam Sculpting: The RB20 robot handles complex foam sculpting tasks with ease. It works efficiently with different materials and shapes.
- Printing Applications: In printing, the RB Engine polishes and finishes steel plates, ensuring high-quality prints and durable printing equipment.
Textile and Apparel Industry
- Spray Coating: The RB08 model sprays coating evenly on denim jeans. It ensures efficient application, enhancing both durability and appearance.
Electronics and Consumer Goods
- Surface Treatment: RB08 robots treat the surfaces of electronic casings, providing a high-quality finish and protection from environmental damage.
- Helmet Cleaning: The RB08 model is used for plasma cleaning helmet visors, ensuring clarity and durability of the protective gear.
Construction and Manufacturing
- Powder Coating: The RB15L model performs powder coating applications, delivering a uniform, durable finish on various surfaces.
- Metal Surface Coating: The RB20 model applies metal powder coating to internal surfaces, ensuring protection and extending component longevity.
Glass and Ceramics Industry
- Adhesive Application: The RSP600A15 robot applies adhesives to glass supports, ensuring precision and strength in glass assembly.
Foundry and Casting
- Sand Molding: The RB50 model applies sand mold slurry, ensuring uniformity and strength during the casting process.
Latest Technical Innovations in RB Engine
Ongoing research aims to enhance efficiency, reliability, and environmental performance of RB engines. Potential future directions include:
- Integration with Renewable Energy Sources:
Hybrid systems may integrate RB engines with renewable energy, improving grid stability and lowering carbon footprints. - AI and Machine Learning:
AI and machine learning could improve control strategies and enable predictive maintenance for better engine performance. - Sustainable Materials:
Exploring eco-friendly materials for critical components can reduce environmental impact and promote sustainability in future RB engine designs.
To get detailed scientific explanations of RB Engine, try Patsnap Eureka.
