
What is Neoprene?
Neoprene, also known by its chemical name polychloroprene, is a family of synthetic rubbers that are produced by the polymerization of chloroprene. It was first developed by DuPont in 1930 and has since found widespread use in various industries due to its unique properties.
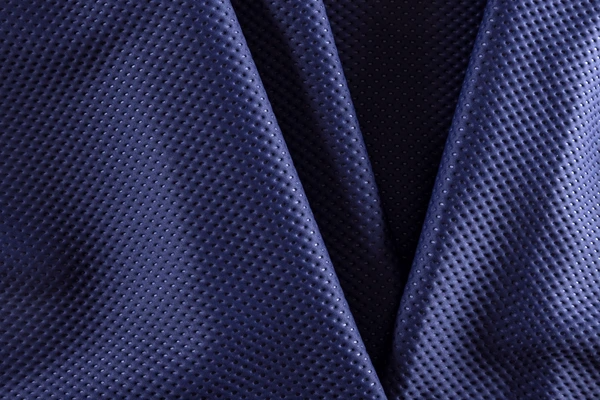
Properties of Neoprene
- Thermal Insulation: Neoprene foam’s closed-cell structure offers excellent thermal insulation. It lets minimal water pass to the skin, which body heat then warms, boosting insulation.
- Elasticity and Flexibility: Neoprene retains elasticity and flexibility across a wide temperature range, perfect for uses needing stretchable and durable materials.
- Chemical Resistance: Neoprene resists oils, chemicals, and weathering, making it ideal for industrial settings exposed to harsh environments.
- Durability: Its resilience allows Neoprene to endure repeated stress and environmental exposure without major degradation, ensuring long-lasting performance.
How is Neoprene Made?
Polymerization
The process begins with the polymerization of chloroprene monomers to form polychloroprene. This is typically achieved through emulsion polymerization, where chloroprene is dispersed in water with the aid of surfactants and initiators. The resulting polychloroprene latex is a stable dispersion of polymer particles in water.
Vulcanization
To enhance the mechanical properties and stability of Neoprene, the polychloroprene latex undergoes vulcanization. This process involves the addition of curing agents, such as sulfur or metal oxides, and accelerators like ethylene thiourea (ETU). Vulcanization creates cross-links between polymer chains, improving the material’s elasticity, strength, and resistance to degradation. However, ETU is known to be toxic and may not be fully eliminated from the final product, posing potential health risks.
Foam Formation
For applications requiring foam, such as wetsuits, the vulcanized polychloroprene is further processed to create a closed-cell foam structure. This involves the incorporation of blowing agents that generate gas bubbles within the material during heating. The closed-cell structure of Neoprene foam provides excellent thermal insulation and buoyancy, as it traps air and minimizes heat transfer.
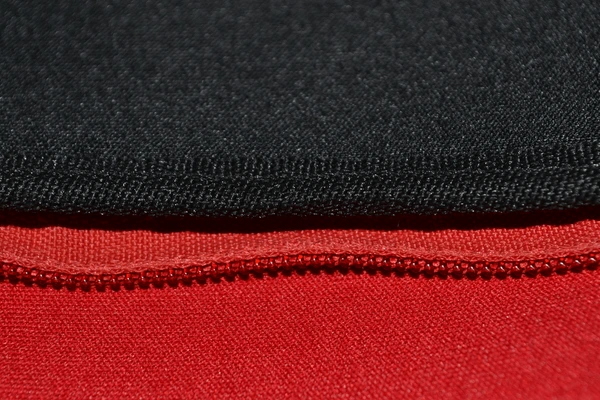
Advantages and Disadvantages of Neoprene
Advantages of Neoprene
- Chemical Resistance: Neoprene is resistant to oils, chemicals, and solvents, making it ideal for use in harsh environments.
- Thermal Stability: It maintains its properties over a wide temperature range, from -50°C to 120°C, which is beneficial for applications requiring thermal resistance.
- Mechanical Properties: Neoprene exhibits good tensile strength, flexibility, and abrasion resistance, which are essential for durable products.
- Water Resistance: Its closed-cell structure provides excellent water resistance, making it suitable for aquatic and marine applications.
- Elasticity: Neoprene has good elasticity and can return to its original shape after deformation, which is useful in applications like wetsuits and gaskets.
Disadvantages of Neoprene
- Cost: It is generally more expensive than other types of synthetic rubber, which can be a limiting factor for cost-sensitive applications.
- Environmental Impact: The production and disposal of Neoprene can have environmental impacts, including the release of harmful chemicals and difficulties in recycling.
- Limited UV Resistance: Prolonged exposure to UV light can cause Neoprene to degrade, which may limit its use in outdoor applications without additional UV protection.
- Allergenic Potential: Some individuals may develop allergic reactions to Neoprene, particularly when used in direct contact with the skin.
Applications of Neoprene
Traditional Applications of Neoprene
- Automotive Industry: It is used for hoses, belts, and gaskets due to its resistance to oils, chemicals, and heat. Its durability and flexibility make it ideal for components exposed to harsh conditions.
- Construction Industry: In construction, it serves in sealing and insulation, commonly found in expansion joints, bridge bearings, and window seals. Its weather resistance and long-term elasticity are vital for these applications.
- Marine Industry: Neoprene’s saltwater resistance and insulating properties make it ideal for wetsuits, diving suits, and other marine gear, offering thermal insulation and buoyancy for underwater activities.
- Electrical Industry: It insulates electrical cables and connectors, providing flame resistance and dielectric properties for safety and reliability in electrical applications.
Innovative Applications of Neoprene
- Medical Devices: Neoprene’s hypoallergenic nature and consistent compression make it ideal for orthopedic braces and supports, ensuring comfort in therapeutic uses.
- Wearable Technology: Its flexibility and comfort make Neoprene a popular choice for wearable tech, including fitness trackers and smart clothing, providing a skin-friendly experience.
- Renewable Energy: It is being explored for seals and gaskets in wind turbines and solar panels, offering durability and resistance to environmental factors, enhancing system longevity.
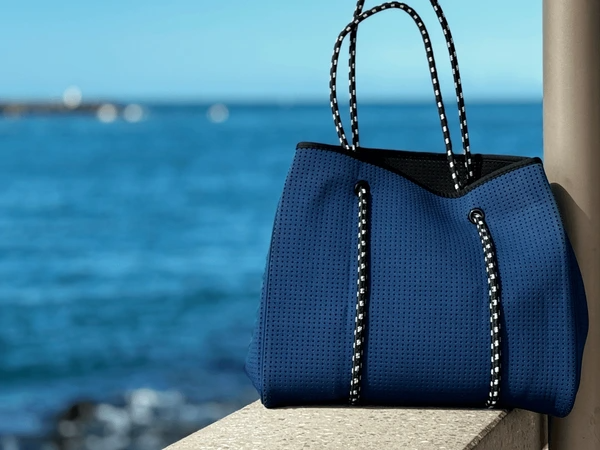
Latest Technical Innovations in Neoprene
Advancements in Synthesis Methods
Recent research has focused on improving the synthesis methods of Neoprene to enhance its properties and production efficiency. One significant innovation is the development of more environmentally friendly polymerization techniques. Traditional methods often involve the use of hazardous solvents and generate significant waste. Newer approaches aim to reduce the environmental impact by utilizing aqueous emulsion polymerization, which minimizes the use of organic solvents and reduces waste production. Additionally, researchers are exploring the use of renewable monomers derived from biomass to replace traditional petrochemical-based monomers, thereby making the synthesis process more sustainable.
Newly Developed Materials or Additives
Recent developments have focused on enhancing Neoprene’s properties through new materials and additives. Incorporating nanomaterials like graphene and carbon nanotubes significantly improves mechanical strength, thermal stability, and electrical conductivity. These nanocomposites outperform conventional Neoprene, making them ideal for demanding applications. Additionally, novel plasticizers and stabilizers are being used to enhance flexibility and durability without compromising other essential properties.
Innovations in Production Process
The production process of Neoprene has seen several innovations aimed at improving efficiency and product quality. One notable advancement is the implementation of continuous production processes, which replace traditional batch processing. Continuous processes offer several advantages, including better control over reaction conditions, reduced production times, and lower operational costs. Additionally, advancements in process monitoring and control technologies, such as real-time spectroscopy and advanced data analytics, have enabled more precise control over the polymerization process, resulting in more consistent product quality.
To get detailed scientific explanations of neoprene, try Patsnap Eureka.

Learn more
Shock Cords: Versatile Strength for Every Need
Pressure Switches: Small Devices, Big Impact
Unveiling The Lead Screw: Its Mechanism, Benefits, And Beyond