
What is Kinetic Friction?
Kinetic friction, also referred to as dynamic friction, is the force that opposes the relative motion of surfaces in contact. Unlike static friction (μs), which prevents motion from starting, kinetic friction (μk) acts once movement occurs. Typically, the coefficient of kinetic friction (μk) is lower than that of static friction (μs). This article explores the principles of kinetic friction, its distinctions from static friction, and its practical significance in various applications.
Formula for Kinetic Friction
The force resisting motion between moving surfaces is calculated using the formula:
fk=μk⋅FNf_k = \mu_k \cdot F_N
Here:
- fkf_k: the kinetic friction force
- μk\mu_k: the coefficient of kinetic friction
- FNF_N: the normal force between surfaces
This relationship shows that friction increases proportionally with the normal force and is influenced by the materials’ friction coefficient.
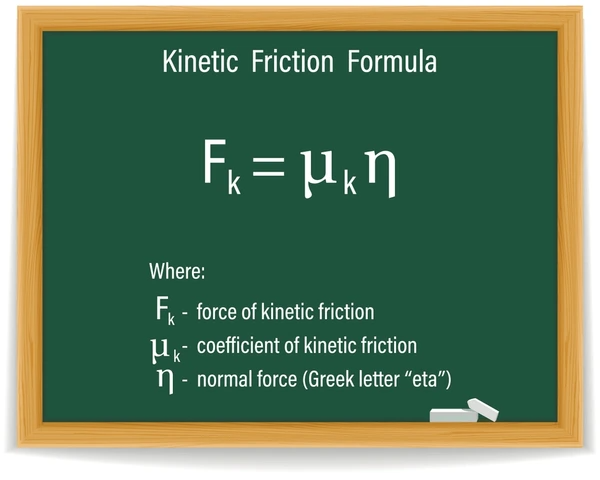
Main Factors Influencing Friction Between Moving Surfaces
Material Properties
The type of material greatly impacts the coefficient of friction. For instance, in paddy hulling, phenolic discs have friction coefficients ranging from 0.155 to 0.221, polyamide discs range from 0.214 to 0.288, and hardwood discs vary between 0.189 and 0.246. These differences depend on the surface characteristics and moisture content of the grains.
Surface Temperature
Heat affects how surfaces interact. As temperature increases, the friction coefficient often rises due to changes in molecular bonding and material properties, especially in high-performance applications.
Surface Roughness and Cleanliness
Rougher surfaces generate more friction due to mechanical interlocking, while dirt or debris can either increase or reduce friction depending on its nature. Clean, smooth surfaces tend to provide more predictable friction.
Contact Mechanics in Specialized Applications
In orthodontics, the type of ligature and bracket-wire combinations influence resistance. Elastic ligatures or stainless steel options affect performance based on material combinations and ligation mechanics.
Moisture Content
Moisture alters surface interactions. For example, paddy grains with moisture content between 11% and 23% exhibit higher resistance at increased moisture levels due to modified surface properties and interactions.
Reducing Kinetic Friction: Lubrication Methods
- Boundary Lubrication (BL): This lubrication regime relies on molecularly thin films that adhere to sliding surfaces. Friction occurs at the interface of these boundary layers, making it effective under conditions of high pressure and low velocity. In such scenarios, liquid lubricants may not fully separate the surfaces. While polymers and soft materials are often used as lubricants in this regime, they can exhibit considerable energy dissipation during motion.
- Mixed Lubrication: Mixed lubrication occurs when both a lubricant film and surface asperities share the load. This regime bridges boundary and hydrodynamic lubrication, balancing film effectiveness with surface contact. It is commonly encountered in scenarios with intermediate velocities and moderate pressures.
- Hydrodynamic Lubrication: Hydrodynamic lubrication minimizes friction by maintaining a full fluid film between sliding surfaces. This regime is typically achieved at high velocities and low loads, where the lubricant film fully separates the surfaces and prevents direct contact, resulting in smooth motion.
- Elastohydrodynamic Lubrication (EHL): EHL combines aspects of hydrodynamic lubrication with elastic deformation of surfaces under high pressure. In this regime, the lubricant film is thinner, yet it effectively reduces friction while accommodating surface deformation. EHL is prevalent in high-pressure applications like gear systems and rolling element bearings, where surface integrity is critical.
Applications of Kinetic Friction
Automotive Industry
Friction is integral to automotive systems, particularly in braking and tire-road interactions. The contact between brake pads and rotors or drums ensures effective deceleration. Advanced materials and innovative designs enhance the durability and efficiency of these components. For example, electromechanical steering systems rely on friction to determine torque, ensuring precise control and safety.
Mechanical Systems and Machinery
In machinery, friction often contributes to wear and tear, impacting efficiency and longevity. Techniques like lubrication and advanced materials help reduce these effects. Vibratory systems also use friction to dampen unwanted vibrations, improving mechanical performance. Additionally, kinematic excitation aids in designing machines with controlled frequency responses, though outcomes may vary.
Material Science and Engineering
Understanding friction is key to creating materials with tailored properties. Advanced testing devices now measure friction coefficients at different speeds, offering critical data for innovation. Research into granular materials reveals how particle interactions generate friction, providing insights for handling powders and optimizing granular flow processes.
Experimental and Educational Tools
Friction concepts are effectively demonstrated through hands-on experiments. The Timoshenko oscillator, for instance, showcases friction principles using a moving plate to measure friction coefficients. This affordable setup offers students an engaging way to explore mechanical principles and the behavior of sliding surfaces.
Lubrication and Surface Engineering
High-pressure scenarios demand careful friction management. Molecular simulations show that lubricant properties and surface interactions influence friction levels. Factors like the flexibility of bonds between the lubricant and surface play a major role, informing the design of effective lubricants and advanced surface treatments.
Application Cases
Product/Project | Technical Outcomes | Application Scenarios |
---|---|---|
Electromechanical Steering Actuators Ford Global Technologies LLC | Determines friction torque for precise control and safety in steering systems. | Automotive steering systems requiring precise control and safety. |
Kinematic Excitation Systems | Active reduction of vibration using mechanical elements. | Designing mechanical systems with desired frequency spectrum. |
Kinetic Friction Test Device | Measures coefficient of kinetic friction with high reliability and feasibility. | Testing kinetic friction in engineering materials. |
Timoshenko Oscillator | Illustrates Coulomb’s law of kinetic friction with accurate measurements. | Educational experiments and demonstrations of kinetic friction. |
Granular Friction Model | Demonstrates kinetic friction through mutual collisions of particles. | Studying granular friction in simple dynamical systems. |
Latest Technical Innovations in Kinetic Friction
Recent advancements in controlling and utilizing kinetic friction include:
- Finite Element Analysis (FEA): The use of FEA software like ABAQUS to simulate and validate kinetic friction models, ensuring the reliability of new test devices.
- Non-Classical Synthetic Methods: Innovative approaches in designing mechanical systems with desired frictional properties, allowing for early verification of system performance.
- Molecular Dynamics Simulations: Advanced simulations to understand the behavior of lubricants and granular materials at the molecular level, leading to better control of frictional properties.
To get detailed scientific explanations of kinetic friction, try Patsnap Eureka.
