
What is an Injection Pump?
An injection pump is a mechanical device that delivers a precise amount of fuel at high pressure to fuel injectors. These injectors then spray fuel into the combustion chamber of an engine. This process plays a key role in the efficient operation of diesel engines, ensuring proper air-fuel mixing and combustion. This article will explore how injection pumps work, their components, and their importance in optimizing engine performance.
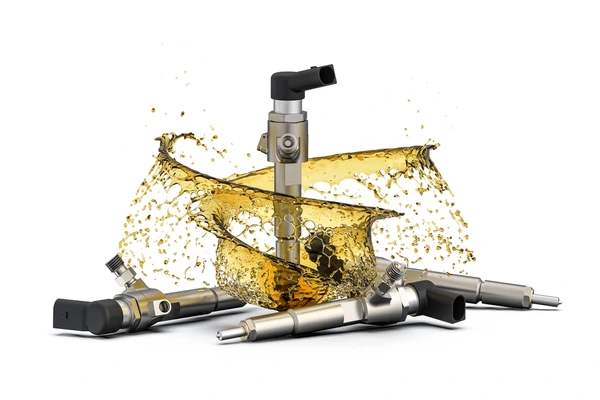
Symptoms of a Failing Injection Pump
Loss of Fuel Pressure: A common sign of failure is a dramatic drop in fuel delivery pressure. This can cause a lean-out condition, where the engine gets less fuel, resulting in poor performance and potential damage.
Reduced Fuel Flow: A malfunctioning pump can cause a significant loss of fuel flow, essential for smooth engine operation. This leads to decreased engine performance and efficiency.
Unusual Sounds: Cavitation in the pump can produce ratchet or grinding noises, signaling the formation of gas bubbles in the fuel.
Inconsistent Engine Performance: A failing pump can cause fluctuating fuel pressure, leading to rough engine operation or decreased power output.
Increased Temperatures: Inefficiency in the pump can cause temperatures above 50°C, raising heat levels in the engine compartment.
Engine Damage: Even short periods of cavitation can damage the pump, reducing its capacity and efficiency, and leading to further engine issues.
System Shutdown: A major failure may trigger safety mechanisms that shut down the engine to prevent further damage.
Methods to Fix a Failing Injection Pump
Replacement of Faulty Components: If a specific part is malfunctioning, replacing just that component may solve the issue, avoiding the need for a full pump replacement.
System Drain and Cleaning: If debris or particles are causing blockages, draining and cleaning the system can restore the pump’s efficiency.
Adjustment of Settings: Adjusting the pump settings or engine parameters can temporarily improve performance until a permanent repair is made.
Regular Maintenance: Preventative maintenance, like regular inspections and replacing worn parts, can prevent pump failure and extend the system’s lifespan.
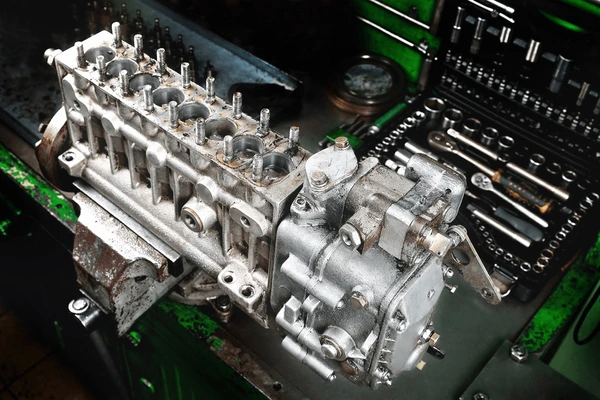
Injection Pump vs. Fuel Pump: Key Differences
Definition and Function
Fuel Pump: A fuel pump draws fuel from the tank and delivers it to the engine at the required pressure. It ensures a steady fuel supply for engine efficiency, typically powered by an electric motor or camshaft.
Injection Pump: An injection pump pressurizes and injects fuel into the engine’s cylinders at high pressure, usually between 150 to 200 bar. It ensures proper fuel atomization and mixing with air for efficient combustion, often called the “heart” of a diesel engine.
Structure and Components
Fuel Pump: A fuel pump has a housing, impeller, and pump stage driven by an electric motor or camshaft. It includes check valves, diaphragms, and nozzles to regulate flow and pressure.
Injection Pump: An injection pump has a more complex structure with a plunger, barrel, cam mechanism, and pressure chamber. It ensures precise control over fuel injection timing and pressure.
Pressure and Flow Rate
Fuel Pump: Fuel pumps operate at lower pressures (30 to 80 kPa) and maintain a flow rate to meet the engine’s demand during operation.
Injection Pump: Injection pumps generate much higher pressures, up to 200 bar, to ensure efficient atomization and combustion in diesel engines.
Advantages and Challenges
Fuel Pump: Fuel pumps are simple, reliable, and have fewer moving parts. However, they lack the precision of injection pumps at high loads or low speeds.
Injection Pump: Injection pumps offer superior fuel control, improving engine performance and efficiency while reducing emissions. However, they require more maintenance due to their complexity.
Applications of Injection Pump
Fuel Injection Systems
Injection pumps are vital in fuel injection systems, particularly in diesel engines. They ensure accurate fuel delivery to the engine’s cylinders, essential for efficient combustion and optimal performance. These pumps are designed to regulate fuel pressure and timing, adapting to engine speed and load conditions.
Water Treatment and Production
Injection pumps are used to inject chemicals into water streams at controlled rates during water treatment. The innovative Line Bleeding Injection Pump (LBIP) utilizes line pressure for efficient chemical injection, offering a low-maintenance solution. This system is particularly beneficial in seawater desalination, reducing power consumption and operating costs in remote areas.
Mixing of Solid and Loose Materials
In industrial applications, injection pumps mix solid materials with gases or liquids. They use spreaders and precise parameters to ensure uniform mixing, which is crucial in processes like material processing and production.
Medical Imaging
In medical imaging, injection pumps administer contrast agents. A new method allows for rapid setup based on patient and appliance-specific parameters, enhancing the efficiency of image recording processes.
Experimental and Testing Platforms
Injection pumps are used in testing environments to calibrate fuel injection systems and speed governors. This is key to ensuring the reliability and performance of diesel engines in vehicles and machinery.
Precision Engineering and Liquid-Crystalline Applications
High-pressure fuel injection systems leverage liquid-crystalline properties to reduce mechanical losses and boost fuel efficiency, demonstrating the advanced applications of pump technology in precision engineering.
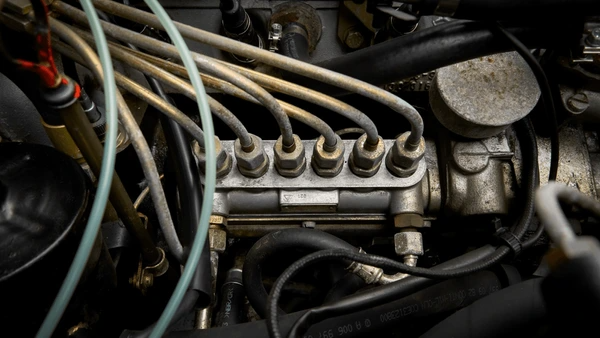
Application Cases
Product/Project | Technical Outcomes | Application Scenarios |
---|---|---|
Self-designed Injection Pump | Optimization of fission structure through reverse design and transposition thinking, improving existing injection pump design. | Design and structural optimization for practical applications. |
High-pressure Fuel Injection Pump | Reduction of friction loss and wear through hydrodynamic and boundary lubrication modes, improving fuel efficiency. | Marine diesel engines requiring high-pressure fuel injection. |
Injection Mixer for Solid Loose Materials | Utilizes an antilock brake device to unload the suction zone, improving mixing efficiency. | Stirring and mixing of solid loose materials in gas and liquid media. |
Fuel Injection Pump Yanmar Power Technology Co., Ltd. | Reduces manufacturing costs and increases the number of components, improving overall efficiency. | Fuel injection systems for internal combustion engines. |
Contrast Agent Injection Pump Siemens Healthineers AG | Enables easy and fast setting of the injection pump for image recording. | Medical imaging requiring precise contrast agent injection. |
Latest Technical Innovations in Injection Pump
Improved Liquid Additive Injection Pumps
- Adjustable Volumetric Flow Rate: Recent innovations allow better control over the volumetric flow rate of injected additives. The addition of an easily accessible adjustment bushing enables changes to the plunger stroke length, which adjusts the amount of additive injected without altering the pump’s power supply.
- Robust Roller Bearing Drive: The use of a strong split-load roller bearing drive improves accuracy and reliability in additive injection. It powers the piston(s) during both suction and discharge to maintain precise flow rates.
- Spring Energized Seal: This design solves common issues with overtightened packing, which often occurs during field maintenance, ensuring smooth operation and easier servicing.
Design and Structural Optimization
Recent design advancements have optimized injection pump structures through reverse engineering and practical application thinking. Self-designed models serve as references for future innovations, showing the importance of ongoing optimization in pump technology.
Novel Line Bleeding Injection Pump (LBIP) Concept
The LBIP concept improves water treatment processes by reducing maintenance needs and cutting operational costs. It uses line pressure to inject chemicals, eliminating the need for additional driving power. This system can inject doses ranging from 10 to 500 liters per day and functions with high-pressure lines. Its variable displacement facility makes it a cost-effective solution, especially for renewable seawater desalination in remote locations.
Two-Stage Injection Pump for Mixing Apparatus
Experiments show that a two-stage pump system enhances mixing performance. Combining two single-stage pumps boosts spread energy and pressure while reducing the required admixture ratio. This setup achieves better spraying pressure at the spray gun’s end, offering significant advantages over traditional pumps.
To get detailed scientific explanations of injection pumps, try Patsnap Eureka.
