
What Is a Heat Sink?
A heat sink is a passive heat exchanger designed to dissipate heat from a hot surface to a cooler ambient environment. It works by maximizing the surface area in contact with the cooling medium (typically air or liquid) and facilitating efficient heat transfer through conduction and convection. Key components of a heat sink include:
- Base plate: A flat surface that attaches to the heat source (e.g., CPU, power transistor) for efficient heat conduction.
- Fins: Thin, parallel protrusions extending from the base plate to increase the surface area for heat dissipation.
- Heat pipes (optional): Embedded tubes containing a working fluid that transfers heat from the base plate to the fins through phase change and capillary action.
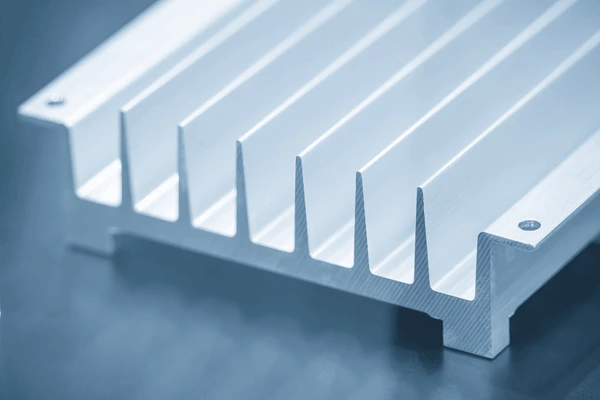
How Does a Heat Sink Work?
- Conduction: The heat sink is typically made of materials with high thermal conductivity, such as aluminum alloys or copper, to facilitate efficient heat transfer from the electronic component to the heat sink base. The heat sink base is in direct contact with the heat-generating component, allowing heat to be conducted from the component to the base.
- Convection: The heat sink features an array of fins or channels that increase the surface area exposed to the surrounding air or coolant. As the heat is conducted from the base to the fins, it is dissipated to the surrounding air or coolant through convection. The increased surface area enhances the convective heat transfer, enabling more efficient heat dissipation.
- Airflow or Coolant Flow: To further improve heat dissipation, heat sinks are often combined with fans or liquid cooling systems. The airflow or coolant flow over the fins enhances convective heat transfer by removing the heated air or liquid from the fin surfaces, allowing for continuous heat dissipation.
Types of Heat Sinks
- Extruded Fin Heat Sinks: The most common and inexpensive type, made by extruding aluminum or copper into fins. They have a relatively simple design with straight fins, offering good heat dissipation at low cost.
- Stamped Plate Fin Heat Sinks: Formed by stamping fins from a flat metal sheet and attaching them to a base. They allow for more complex fin designs like pin fins or flared fins for increased surface area.
- Folded Fin Heat Sinks: Manufactured by folding thin metal strips into a fin array. This enables very thin fin spacing and high fin density for improved thermal performance.
- Vapor Chamber Heat Sinks: Contain a vapor chamber integrated into the base that utilizes phase change cooling for high heat transfer rates. Suitable for high heat flux applications.
- Heat Pipe Heat Sinks: Incorporate heat pipes embedded in the base or fins to effectively transfer heat through phase change cooling over longer distances.
- Radial/Circular Heat Sinks: Designed for uniform heat spreading from a circular heat source like LEDs. The fins are arranged radially for efficient air flow.
- Composite/Polymer Heat Sinks: Made from thermally conductive polymer composites or advanced materials like pyrolytic graphite. Offer lighter weight and tailored thermal properties.
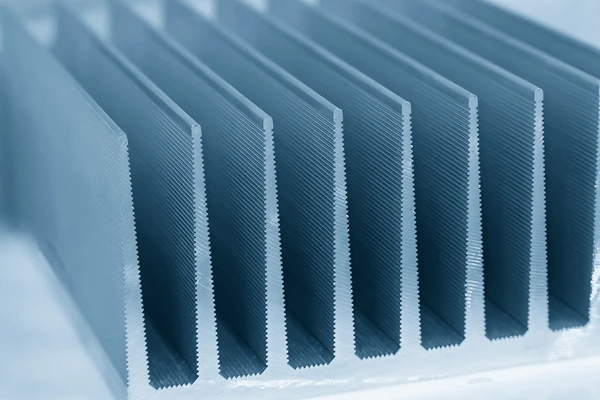
Common Materials Used in Heat Sinks
- Aluminum alloys: Lightweight, inexpensive, and easy to manufacture. Thermal conductivity around 150-250 W/m-K. Widely used in CPU coolers and electronics cooling.
- Copper: Excellent thermal conductivity (around 400 W/m-K), but heavier and more expensive than aluminum. Used in high-performance applications.
- Copper alloys: Combine copper’s high conductivity with improved mechanical properties. Examples include copper-tungsten and copper-molybdenum alloys.
How to Choose the Right Heat Sink
Heat Sink Material Properties
The material properties of the heat sink are crucial for effective heat dissipation. Key properties to consider include:
- Thermal conductivity: Higher thermal conductivity allows for better heat transfer from the heat source to the fins. Copper and aluminum alloys are commonly used due to their high thermal conductivity.
- Density: Lower density materials are preferred to reduce the overall weight of the heat sink.
- Coefficient of thermal expansion: Materials with a low coefficient of thermal expansion minimize thermal stresses and deformations.
- Cost: Aluminum alloys are generally more cost-effective than copper, though copper has superior thermal conductivity.
Heat Sink Design and Geometry
The design and geometry of the heat sink significantly impact its thermal performance:
- Fin geometry: Fin height, thickness, spacing, and shape affect the surface area for heat dissipation and airflow characteristics.
- Base plate thickness: A thicker base plate improves heat spreading from the heat source.
- Surface enhancements: Techniques like fin interruptions, perforations, and surface roughening can enhance heat transfer.
- Vapor chambers/heat pipes: Integrating vapor chambers or heat pipes into the heat sink can further improve heat dissipation.
Thermal Load and Operating Conditions
The thermal load and operating conditions dictate the heat sink requirements:
- Heat flux: Higher heat fluxes from the heat source necessitate more efficient heat sinks.
- Airflow conditions: Forced convection (fans) or natural convection (passive cooling) affect heat sink design.
- Operating environment: Factors like ambient temperature and airflow quality influence heat sink selection.
- Partial heating: Optimizing the heat sink for the specific heated area can improve performance.
Additional Considerations
Other factors to consider include:
- Space constraints: Compact designs may require specialized heat sink geometries.
- Active cooling integration: Compatibility with liquid cooling or fan configurations.
- Cost and manufacturability: Simpler designs may be preferred for cost and ease of manufacturing.
- Reliability and lifetime: Materials and designs that minimize thermal stresses and corrosion.
Advantages of Heat Sinks
- Effective heat dissipation, preventing overheating and failure
- Compact and lightweight compared to liquid cooling systems
- Passive operation (no moving parts) for natural convection designs
- Scalable and customizable for different heat loads and space constraints
Challenges and Limitations
- Limited heat transfer capacity, especially for high-power devices
- Fin spacing and airflow resistance trade-off
- Orientation and gravity dependence for natural convection designs
- Manufacturing complexity for advanced designs (e.g., vapor chambers)
- Potential noise and power consumption for forced convection
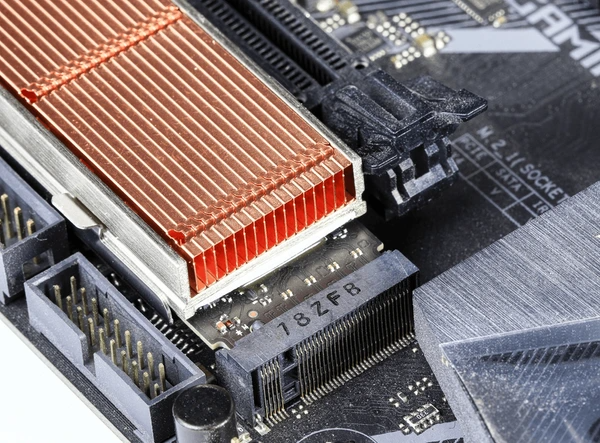
Applications of Heat Sinks
Computer Hardware Heat sinks are widely used to dissipate heat from computer components like CPUs, GPUs, and chipsets, preventing overheating and ensuring optimal performance.
Power Electronics Heat sinks play a crucial role in power electronics, cooling devices like transistors, rectifiers, and voltage regulators in power supplies, inverters, and converters.
Automotive Industry Automotive applications of heat sinks include cooling engine control units, power electronics modules, and LED lighting systems in vehicles.
LED Lighting Heat sinks are essential for LED lighting systems, dissipating heat generated by high-power LEDs and ensuring their longevity and efficiency.
Telecommunications In telecommunications, heat sinks are used to cool power amplifiers, transceivers, and other high-power components in base stations and networking equipment.
Renewable Energy Heat sinks are employed in solar photovoltaic systems and wind turbines to cool power electronics and ensure optimal energy conversion efficiency.
Industrial Machinery Various industrial machines and equipment, such as motors, drives, and welding systems, utilize heat sinks to dissipate excess heat and maintain reliable operation.
Application Cases
Product/Project | Technical Outcomes | Application Scenarios |
---|---|---|
CPU Coolers | Efficient heat dissipation for high-performance processors | Desktop and laptop computers |
GPU Coolers | Effective cooling for graphics processing units | Gaming PCs and workstations |
Server Heat Sinks | Reliable thermal management for data center servers | Enterprise data centers |
LED Heat Sinks | Optimized heat transfer for high-power LED lighting | Commercial and industrial lighting systems |
Battery Cooling System | Efficient thermal management for EV battery packs | Electric vehicles |
Latest Technical Innovations in Heat Sinks
Heat Sink Design Innovations
- 3D Airflow Channel Design: Creating three-dimensional airflow channels in the heat sink structure to increase heat exchange between the sink and air, improving heat dissipation efficiency.
- Crimped Fin Design: Using grooves in the heat sink base and impact-deformed walls to hold fins in place, creating voids that exhibit high thermal resistance for better heat transfer.
- Topology Optimization: Employing graph theory, population search algorithms, and response surface methodology to optimize the topology of a 3D heat sink structure composed of nodes and edges for increased heat dissipation.
- Gas-Liquid Plug Flow: Restricting pipeline size and forming a gas-liquid plug flow, along with curved and partially-cylindrical surfaces to increase windward area and heat dissipation.
- Integrated Fin Structure: Connecting tips of adjacent fins with a connecting piece, forming an integrated structure that decreases mass and improves heat dissipation and manufacturing/installation efficiency.
Innovative Heat Sink Materials
- Cladded Metal Approach: Cladding a core metal with an outer metal of lower melting point, pressing the outer metal into grooves in the base for better heat transfer and manufacturing efficiency.
- High Conductivity Materials: Using materials with higher thermal conductivity than conventional metals (e.g., aluminum) as the primary heat dissipation member, such as embedding heat pipes in the base.
- Nanofluids: Incorporating nanofluids, which exhibit enhanced thermal properties, into heat sink designs for improved heat transfer performance.
- Phase Change Materials: Utilizing phase change heat pipes or materials to enhance heat dissipation performance, particularly in compact electronic devices.
- Low-Weight High-Conductivity Materials: Exploring lightweight, high thermal conductivity materials like carbon-based composites or metal foams to address the weight limitations of conventional metal heat sinks.
FAQs
- What is the main purpose of a heat sink?
The main purpose is to dissipate heat away from electronic components to prevent overheating and maintain performance. - Can I run a CPU or GPU without a heat sink?
No, running high-performance components without a heat sink can lead to overheating and permanent damage. - How do I clean and maintain a heat sink?
Use compressed air to remove dust and ensure fans (if applicable) are free of debris. Regular cleaning improves efficiency. - Are copper heat sinks better than aluminum ones?
Copper offers better thermal conductivity but is heavier and more expensive. Aluminum is more cost-effective and lighter. - What is the difference between passive and active heat sinks?
Passive heat sinks rely on natural convection, while active heat sinks use fans or pumps to enhance heat dissipation.
To get detailed scientific explanations of heat sinks, try Patsnap Eureka.

Learn more
Multiplexor: Efficient Data Selector for Electronics
Understanding STP Cable: Shielded Twisted Pair Explained
Understanding Twisted Pair Cable: Basics, Benefits, and Uses
JFET 101: A Beginner’s Guide to Junction Field-Effect Transistors
HDMI vs. DisplayPort: Which is Best for Your Monitor?