
High-density polyethylene, commonly known as HDPE, is a thermoplastic polymer widely used in packaging, construction, piping, and industrial applications. Known for its high strength, chemical resistance, and durability, HDPE is one of the most versatile and widely used plastics. This article explores the composition, properties, applications, advantages, and environmental impact of HDPE.
What is HDPE?
High-density polyethylene (HDPE) is a linear, semi-crystalline thermoplastic polymer known for its high strength, rigidity, and chemical resistance. It is widely used in packaging, construction, piping, and industrial applications due to its excellent durability and processability.
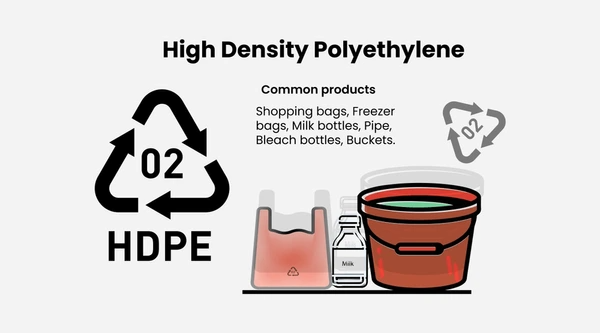
Key Characteristics of HDPE
- Crystallinity: 80-90%, contributing to its strength and rigidity.
- Density: Ranges from 0.93 to 0.97 g/cm³.
- Softening Point: 125-135°C, allowing for high-temperature applications.
- Long-Term Usage Temperature: Can withstand up to 100°C.
How HDPE is Produced
HDPE is manufactured through low-pressure catalytic polymerization, commonly using Ziegler-Natta catalysts. Its linear molecular structure results in high rigidity and excellent chemical resistance.
Molecular Structure and Comonomers
- Primary Comonomers: Includes C4-C10 α-olefins such as 1-butene and 1-hexene, which improve impact strength and flexibility.
- Molecular Weight Distribution:
- Single-modal HDPE: Uniform molecular weight for specific applications.
- Bimodal HDPE: Combines high and low molecular weight components for improved melt strength and flowability.
Example: Bimodal HDPE for Advanced Performance
Some HDPE formulations, such as Dow’s CONTINUUM™ resins, use a bimodal molecular structure to achieve a balance between strength, durability, and processing ease, making them ideal for industrial and high-performance applications.
Wondering how HDPE enhances performance in various applications? Eureka Technical Q&A provides expert insights into its durability, chemical resistance, and versatility, helping you understand why high-density polyethylene is a top choice for industrial and commercial use.
Key Properties and Limitations of HDPE
Advantages of HDPE
- Chemical Resistance: Resistant to acids, alkalis, salts, and aliphatic hydrocarbons. It remains insoluble in organic solvents at room temperature.
- Mechanical Strength: Higher tensile strength than LDPE, with typical values ranging from 20-30 MPa. Excellent resistance to creep deformation.
- Processing Versatility: Suitable for injection molding, blow molding, and extrusion. Wide melt flow rate (MFR) range from 0.1 to 50 g/10 min, allowing adaptability for different manufacturing processes.
Technical Limitations
- Heat Resistance Constraints: The long-term usage temperature is below 100°C, with a heat distortion temperature (HDT) of around 75-90°C, limiting its use in high-heat environments.
- Environmental Stress Cracking (ESCR): High-density polyethylene has high notch sensitivity. Unmodified HDPE typically has an ESCR value (ASTM D1693) below 200 hours, making it susceptible to stress cracking under certain conditions.
- Surface Characteristics: Native High-density polyethylene has a low surface energy (~31 mN/m), which makes it challenging for adhesion, printing, and coating applications without surface treatment.
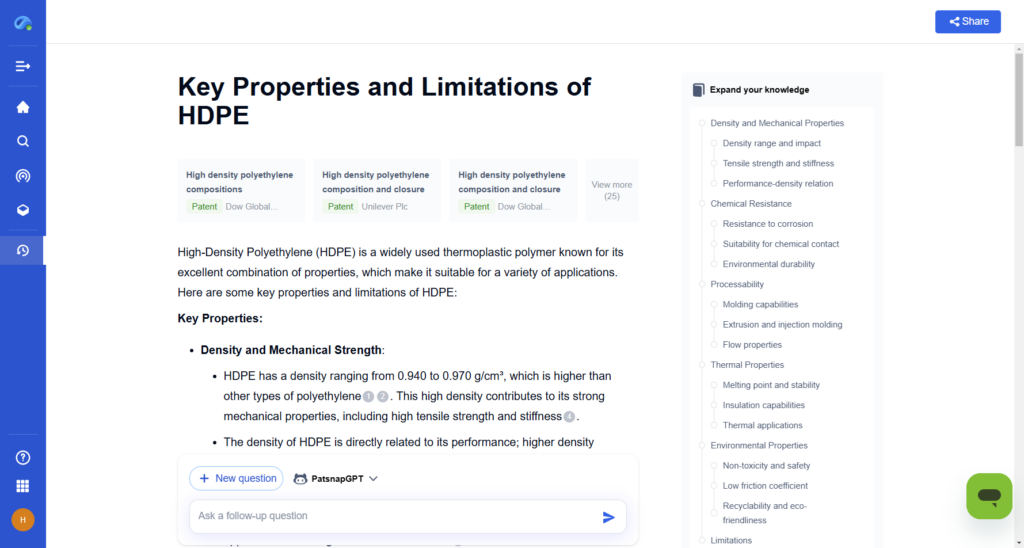
HDPE Applications Across Industries
High-Density Polyethylene (HDPE) continues to evolve with new material innovations, enhancing its strength, durability, and versatility. Below are key applications and technical advancements shaping the future of High-density polyethylene.
Infrastructure & Fluid Transport Systems
- Piping Solutions
HDPE’s molecular design, such as bimodal PE 4710 resins, enables high-pressure resistance (≥12.5 MPa) and an extended service life exceeding 50 years. Its low hydraulic friction improves efficiency, while innovative wall structures reduce production costs and maintain leak-proof joints. - Critical Evaluation
Some patents highlight abrasion resistance in slurry pipes using monomodal HDPE (density ≥939 kg/m³, MWD 3–12). However, bimodal resins dominate due to superior stress crack resistance, suggesting a trade-off between molecular distribution and performance in specific applications.
Medical Implants & Prosthetics
- Rhinoplasty Applications
Porous HDPE implants enhance nasal tip projection by 15–20%, as shown in a 33-patient study. Their biocompatibility and pore interconnectivity (100–300 µm) support tissue integration, improving structural stability. - Reliability Considerations
Although clinical results are promising, long-term data on foreign body reactions and calcification risks remain limited. Further research is needed to ensure long-term safety.
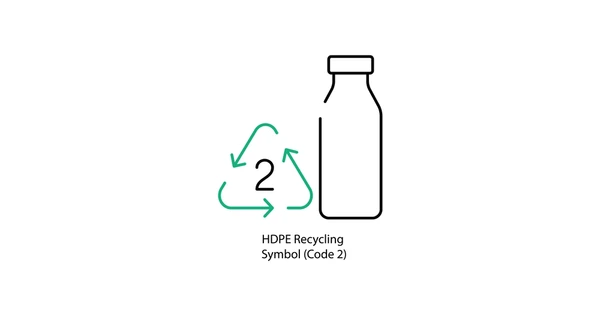
Additive Manufacturing & Recycling
- 3D Printing Innovations
Blending HDPE with branched polyethylene (20–30% wt.) reduces warpage by 40% and improves layer adhesion. Recycled HDPE/glass fiber composites retain at least 85% of their tensile strength after reprocessing. - Technical Challenges
Filament extrusion requires precise temperature control (190–230°C) to prevent polymer degradation and maintain print quality. Manufacturers must optimize processing conditions for consistency.
High-Performance Composites
- Reinforced HDPE Blends
Adding 9 wt.% PAN fibers increases HDPE’s tensile strength by 1.2× (~35 MPa) and raises the Vicat softening point by 8°C. UHMWPE/HDPE blends (5–10% wt.) enhance impact strength at −46°C by 3×. - Limitations
Despite strength improvements, PAN fibers reduce elongation at break from 600% to 250%, limiting overall ductility. This trade-off must be considered for structural applications requiring flexibility.
Sustainable Packaging
- Enhanced Barrier Properties
HDPE produced with late-transition metal catalysts reduces oxygen transmission rates by 30% compared to traditional Ziegler-Natta catalysts. These improvements help extend the shelf life of packaged goods. - Market Insights
Bio-based HDPE from sugarcane ethanol is gaining traction. However, scalability remains a challenge due to high feedstock costs, limiting its widespread adoption.
Structural Engineering
Shish-Kebab Morphology for Strength Enhancement
Extensional dynamic oscillatory shear flow induces oriented crystalline structures, increasing tensile strength up to 120 MPa (3.8× higher than baseline HDPE). This technique enables applications in load-bearing aerospace components, offering fatigue resistance beyond 10⁶ cycles at 20 MPa stress.
HDPE Suppliers and Grades
Several global manufacturers produce high-performance, High-density polyethylene grades tailored for different industrial applications. Below are key suppliers and their representative high-density polyethylene products, including their properties and common applications.
SABIC: SABIC® HDPE F00952
- Properties:
- High density (0.952 g/cm³)
- High tensile strength (MD 60 MPa / TD 56 MPa)
- High elongation at break (MD 400% / TD 550%)
- Heat resistance (Vicat softening point 125°C)
- Excellent oxidation resistance and printability
- Applications:
- High-strength shopping bags and grocery bags
- Multi-wall bag liners
- Replacement for thin paper products
- High-quality printed packaging films
LyondellBasell: Petrothene LT493501
- Properties:
- High density (0.948 g/cm³)
- High environmental stress crack resistance (ESCR: 1000 hours, Condition B)
- Tensile strength of 24.1 MPa
- Elongation at break of 600%
- Flexural modulus of 900 MPa
- Vicat softening point of 126°C
- Easy to process for extrusion and blow molding
- Applications:
- Fiber optic and telecommunication cable conduits
- High-voltage power cable protective pipes
- Blow-molded containers
- Engineering-grade pipes compliant with ASTM F2160/D3350 standards
LOTTE Chemical: HIVOREX® 5000S
- Properties:
- High density (0.954 g/cm³)
- High tensile strength (31.4 MPa)
- High elongation at break (500%)
- High flexural modulus (981 MPa)
- Vicat softening point of 125°C
- Excellent impact resistance (20 kg·cm/cm)
- Easy to process for fiber and stretched applications
- Applications:
- Monofilament for ropes and fishing nets
- Waterproof tarpaulins
- High-strength woven bags
- Industrial textiles
- Melt-stable fiber extrusion applications
LOTTE Chemical: HIVOREX® 7000F
- Properties:
- High density (0.956 g/cm³)
- Low melt flow rate (0.035 g/10 min)
- High ESCR (1000 hours, F50)
- Tensile strength of 31.4 MPa
- Elongation at break of 500%
- Flexural modulus of 981 MPa
- Vicat softening point of 124°C
- Excellent bubble stability for blown film applications
- Applications:
- Industrial and general-purpose packaging films
- Shopping bags and garbage bags
- High-toughness thin film products
- High-strength packaging materials suitable for blown film processing
Strategic Insights for R&D
- Priority Areas:
- Recycled HDPE Upcycling: Validate mechanical properties of waste-derived aggregates against ASTM D638/D790.
- Multimodal HDPE Scalability: Assess cost-effectiveness of three-stage polymerization vs. conventional methods.
- Transparent HDPE: Explore copolymerization with α-olefins (e.g., 1-hexene) to enhance optical clarity without orientation .
- Risk Mitigation:
- Patent ’s biaxially oriented HDPE films (MD×TD = 2×6) lack data on stress-cracking resistance.
- Claims in (HDPE covers for wastewater lagoons) are mechanically descriptive but lack material innovation.
Emerging Opportunities
- Bio-Based HDPE: Integrate with flame-retardant additives for non-woven applications .
- Smart Additives: Develop pH-responsive stabilizers for high-density polyethylene used in harsh environments .
- AI-Driven Formulation: Leverage ML to optimize multimodal high-density polyethylene compositions for target MFR/density ranges.
Innovations in HDPE Research with Eureka
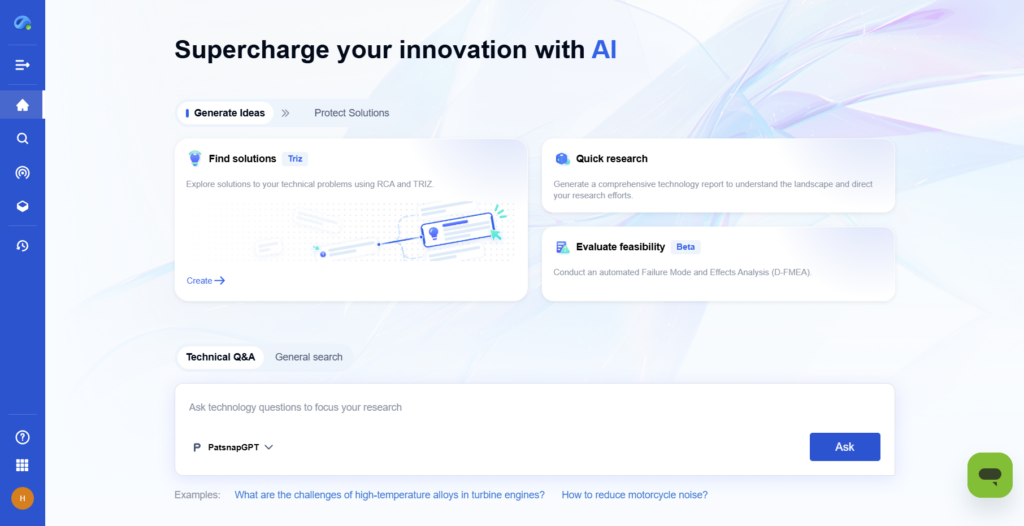
🔍 What is Eureka?
Eureka by PatSnap is an AI-powered research intelligence tool that helps manufacturers and engineers:
- Analyze material properties
- Discover patents and new HDPE applications
- Optimize production methods with real-time data insights
🔍 How Eureka Enhances HDPE Research
- Material Performance Analysis – Eureka identifies new polymer blends for improving HDPE strength and flexibility.
- Sustainability Optimization – AI-driven research suggests eco-friendly recycling methods for HDPE.
- Patent Intelligence – Eureka tracks global innovations in high-Density Polyethylene production and applications.
📌 Example of Eureka in Action:
A plastics manufacturing company using Eureka can:
- Analyze patents on biodegradable High-Density Polyethylene alternatives
- Predict the durability of High-Density Polyethylene pipes in extreme conditions
- Find new applications for recycled High-Density Polyethylene in the automotive sector
Conclusion
HDPE is a high-performance plastic widely used in packaging, construction, automotive, and medical industries. Its strength, chemical resistance, and recyclability make it an essential material for modern applications.
🔍 Want to explore the latest trends in HDPE research? Sign up for Eureka today and unlock AI-powered insights!
FAQs
1️⃣ What makes HDPE different from other plastics?
✅ High-Density Polyethylene is stronger, more durable, and resistant to chemicals, making it superior for industrial and packaging applications.
2️⃣ Is HDPE environmentally friendly?
✅ While High-Density Polyethylene is not biodegradable, it is 100% recyclable, making it a sustainable choice for various industries.
3️⃣ How does Eureka help in HDPE research?
✅ Eureka analyzes material properties, tracks new patents, and suggests innovative recycling methods for High-Density Polyethylene applications.
4️⃣ Can HDPE be used for drinking water pipes?
✅ Yes! High-Density Polyethylene pipes are approved for potable water systems due to their non-toxic and corrosion-resistant properties.
5️⃣ What are the future trends in High-Density Polyethylene technology?
✅ Innovations like biodegradable High-Density Polyethylene, smart composites, and AI-powered recycling methods are shaping the future of High-Density Polyethylene materials.
To get detailed scientific explanations of HDPE, try Patsnap Eureka.
