
In today’s complex product development landscape, organizations must identify and address risks before they lead to costly failures or safety issues. One of the most advanced and structured tools used for this purpose is FMECA—Failure Modes, Effects, and Criticality Analysis. Building on the foundational principles of FMEA, FMECA adds a layer of criticality assessment to help teams prioritize the most severe and impactful failure modes.
This article offers a complete guide to FMECA: what it is, how it works, where it’s applied, and how tools like PatSnap’s Eureka Feasibility Analysis AI Agent can optimize and accelerate the entire process using AI-driven insights.
What Is FMECA?
FMECA stands for Failure Modes, Effects, and Criticality Analysis. It is an advanced form of FMEA (Failure Mode and Effects Analysis) that adds a quantitative or qualitative criticality assessment to prioritize failure modes based not only on likelihood and detectability but also on system-level impact.
The goal of FMECA is to:
- Identify all possible failure modes in a product, process, or system.
- Analyze their effects on performance, safety, or mission success.
- Assess the criticality (or importance) of each failure mode.
- Guide design, testing, or mitigation actions based on risk severity.
FMECA is used extensively in aerospace, defense, medical devices, automotive, and other safety-critical industries where system failure can have serious consequences.
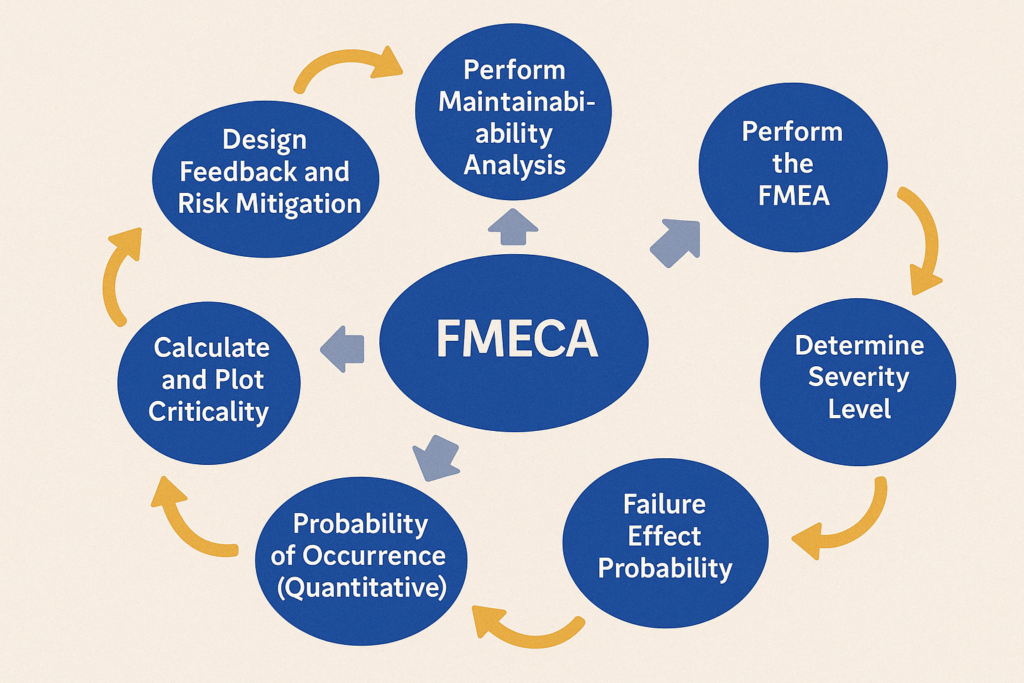
How FMECA Works: Key Components and Process
The FMECA process follows the structure of a traditional FMEA with an added emphasis on criticality analysis. The core steps include:
- Define the Scope
Clearly outline the system, assembly, or process to be analyzed. Break it into functions, components, or process steps. - Identify Failure Modes
For each item or function, list all potential ways it could fail (e.g., breakage, signal loss, leakage, overheat). - Analyze Effects
Determine the impact of each failure on the overall system or process. Effects can include safety hazards, functional loss, downtime, or degradation. - Determine Causes and Detection Methods
Record the likely causes of each failure and how easily they can be detected during testing, inspection, or real-world use. - Calculate Severity, Occurrence, and Detection
Like FMEA, each failure mode is scored for how severe its consequences are, how frequently it might occur, and how likely it is to be detected. - Conduct Criticality Analysis
Assess the criticality level using one of two methods:- Quantitative: Multiply failure rate by severity and exposure.
- Qualitative: Classify failures into priority categories (e.g., high, medium, low) based on impact.
- Prioritize and Act
Use criticality rankings to focus on high-risk issues first and implement corrective actions to reduce risk or improve monitoring.
Why Use FMECA Over Standard FMEA?
While traditional FMEA is effective for identifying potential failure modes, FMECA goes further by quantifying or ranking their criticality in a system context. This is essential in applications where:
- Safety is paramount (e.g., flight control systems, implantable medical devices)
- Downtime is costly (e.g., power generation, manufacturing lines)
- Redundancy must be justified (e.g., in aerospace and defense systems)
Failure Modes, Effects, and Criticality Analysis also supports compliance with rigorous standards such as MIL-STD-1629A, IEC 60812, and SAE J1739, making it a necessary step in government contracts and regulated industries.
Applications of FMECA in Real-World Industries
- Aerospace and Defense: To evaluate risks in propulsion, avionics, navigation, and communication systems.
- Medical Devices: To ensure critical components (e.g., pacemakers, infusion pumps) perform reliably and safely.
- Automotive: To analyze failures in braking, steering, and advanced driver-assistance systems (ADAS).
- Energy and Utilities: To prevent critical failures in power plants, turbines, or oil rigs.
In these sectors, Failure Modes, Effects, and Criticality Analysis is often part of a broader reliability engineering or systems safety strategy.
How PatSnap’s Eureka AI Agent Enhances FMECA
While FMECA provides deep insights into failure modes and risk levels, the traditional process can be time-consuming and heavily reliant on expert judgment. That’s where PatSnap’s Eureka Feasibility Analysis AI Agent steps in—augmenting FMECA with automation, predictive analytics, and real-world data.

1. AI-Driven Failure Mode Detection
Eureka scans global databases—patents, technical reports, and historical failures—to automatically suggest relevant failure modes. This reduces blind spots and speeds up the discovery phase.
2. Real-Time Criticality Assessment
Eureka applies machine learning models to score severity, occurrence, and detection based on past outcomes and data trends. For quantitative analysis, it estimates failure rates and ranks modes by criticality in seconds.
3. Simulation-Based Validation
For complex designs like sensor-regulated silencers or mission-critical systems, Eureka simulates operating conditions to identify critical failure points under real-world stressors.
4. Smart Recommendations for Risk Mitigation
Beyond just identifying risks, Eureka recommends corrective actions—such as design changes, better materials, or monitoring methods—based on proven industry solutions.
5. Automated FMECA Reports
Eureka auto-generates professional-grade FMECA reports with tables, criticality indices, risk rankings, and suggested improvements—ideal for audits, certifications, or engineering reviews.
By integrating Eureka into the FMECA workflow, companies can accelerate analysis, reduce human error, and make better-informed decisions using AI-enhanced insights.
FMECA vs. FMEA: What’s the Difference?
Feature | FMEA | FMECA |
---|---|---|
Focus | Identifying failure modes and effects | Adding criticality to prioritize failure modes |
Analysis Depth | Qualitative | Qualitative + Quantitative |
Used In | General product/process development | Safety-critical, high-reliability systems |
Risk Prioritization Method | RPN (Severity × Occurrence × Detection) | Criticality Index (Failure Rate × Severity) |
Common Standards | ISO 9001, IATF 16949 | MIL-STD-1629A, IEC 60812, SAE J1739 |
Best Practices for Effective FMECA
To get the most out of FMECA, follow these practices:
- Start early: Perform FMECA during concept or architecture definition phases.
- Use cross-functional teams: Include system engineers, quality, safety, and domain experts.
- Leverage real-world data: Feed FMECA with actual field failure data or simulation results.
- Revisit regularly: Update FMECA as the design, process, or usage environment changes.
- Use tools like Eureka: Accelerate and enhance the process with AI-powered assistance.
Conclusion
FMECA remains a gold-standard methodology for identifying and prioritizing failure risks in critical systems. But traditional methods are time-intensive and prone to oversight. PatSnap’s Eureka Feasibility Analysis AI Agent transforms FMECA into a faster, more reliable, and insight-rich process—driven by data, simulation, and AI.
Whether you’re working on aerospace systems, medical devices, or advanced mechanical assemblies, combining FMECA with Eureka helps you prevent failure, reduce cost, and design with confidence.
Streamline your criticality analysis. Strengthen your product reliability. Start your next FMECA with Eureka.
To get detailed scientific explanations of FMECA, try Patsnap Eureka.
