
What is a Flange?
A flange is a ring-shaped device designed to connect various piping system components. It is primarily used where a connecting or dismantling joint is needed, such as the joint of pipes to fittings, valves, or equipment. The mating surface of a flange, nozzle, or valve is called the “face,” which is usually machined to create a smooth surface.
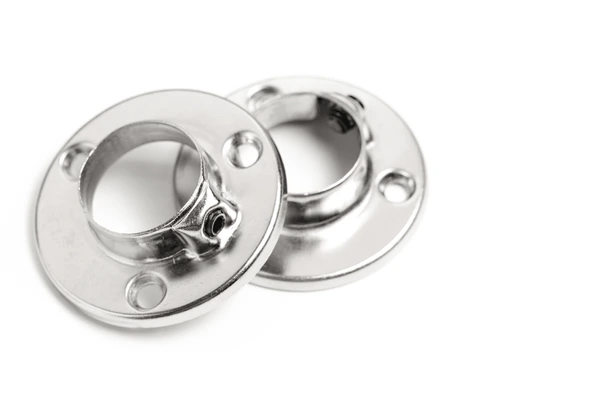
How Flanges Work
- Mating Surfaces: Flanges have surfaces that fit against similar surfaces on other components, creating a seal when bolted together.
- Mounting Portions: These portions include holes for bolts or studs, which are used to secure the flange to another flange or surface.
- Sealing Mechanism: The sealing is often achieved using gaskets placed between the mating surfaces. The contact pressure applied by flange screws ensures the tightness of the seal.
- Material and Design: Flanges can be made from various materials, including metals like steel, stainless steel, and precious metals such as platinum group metals for high-temperature applications 2. The design may include features like ribs for added strength and stability.
Types of Flanges
- Weld Neck Flange: Designed for high-pressure applications, it has a long tapered hub that provides reinforcement.
- Threaded Flange: Used in low-pressure and non-critical applications, it is screwed onto the pipe without welding.
- Socket Weld Flange: Ideal for small-diameter, high-pressure pipes, it is welded on one side only.
- Slip-On Flange: Easier to install, it is slipped over the pipe and then welded.
- Lap Joint Flange: Used with a stub end, it is suitable for systems requiring frequent dismantling.
- Reducing Flange: Used to connect pipes of different diameters.
- Blind Flange: Used to close the end of a piping system.
- Orifice Flange: Used for measuring the flow rate of fluids.
Common Materials Used for Flanges
- Carbon Steel: Commonly used due to its strength and affordability.
- Stainless Steel: Offers excellent corrosion resistance, making it suitable for harsh environments.
- Alloy Steel: Provides enhanced mechanical properties for high-pressure and high-temperature applications.
- Composite Materials: Used for specific applications requiring lightweight and corrosion-resistant properties.
Advantages of Using Flanges
- Ease of Assembly and Disassembly: Flanges allow for quick and easy assembly and disassembly of piping systems, facilitating maintenance and inspection.
- Versatility: Flanges can be used in various applications, including plumbing, heating, and industrial systems, and can accommodate different pipe sizes and materials.
- Leak-Proof Connections: Properly installed flanges provide a secure and leak-proof connection, essential for fluid and gas transport.
- Flexibility: Flanges can be designed to accommodate different orientations and positions, making them suitable for complex piping systems.
Disadvantages of Flanges
- Potential for Misalignment: Flanges require precise alignment during installation. Misalignment can lead to leaks and mechanical failures.
- Space Requirements: Flanges can be bulky, requiring additional space for installation and maintenance.
- Cost: High-quality flanges, especially those made from specialized materials like precious metals, can be expensive.
- Maintenance: Flanges may require regular maintenance to ensure the integrity of the connection, especially in high-pressure or high-temperature applications.
Flange Standards and Specifications
Flanges are manufactured and tested according to various international standards to ensure their quality and compatibility. Some of the key standards include:
- ASME B16.5: This standard covers pipe flanges and flanged fittings for sizes NPS 1/2 through NPS.
- EN 1092-1: This European standard specifies the requirements for circular flanges made from steel and other materials.
- ISO 7005: This international standard provides guidelines for metallic flanges, including dimensions, tolerances, and pressure ratings.
- API 605: This standard covers large-diameter carbon steel flanges for the petroleum industry.
Specifications of Flanges
Flanges are specified based on several parameters, including:
- Size: The nominal pipe size (NPS) or diameter of the flange.
- Pressure Class: The pressure rating of the flange, which indicates the maximum pressure it can withstand.
- Material: The material of construction, such as carbon steel, stainless steel, or alloy steel.
- Face Type: The type of face, such as raised face (RF), flat face (FF), or ring-type joint (RTJ).
- Bolt Holes: The number, size, and spacing of bolt holes for securing the flange
Choosing the Right Flange
- Pressure and Temperature Ratings: Ensure the flange can withstand the operating conditions of the system.
- Material Compatibility: Choose a flange material compatible with the pipe and the fluid being transported to prevent corrosion and degradation.
- Size and Thickness: Ensure the flange dimensions match the pipe size and thickness to maintain system integrity.
- Installation and Maintenance: Consider ease of installation and the need for future maintenance or disassembly.
- Cost: Balance the initial cost with the long-term benefits and performance of the flange.
Maintenance and Inspection of Flanges
- Visual Inspection: Regularly check for signs of corrosion, wear, and damage on the flanges and bolts.
- Torque Verification: Ensure that bolts are tightened to the specified torque to maintain the integrity of the seal.
- Gasket Inspection: Check the condition of gaskets and replace them if they show signs of wear or damage.
- Leak Testing: Perform pressure tests to detect any leaks in the system.
- Cleaning: Keep the flange faces clean and free from debris to ensure a proper seal.
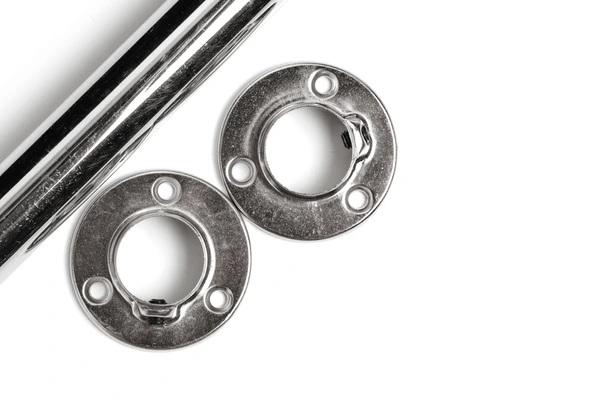
Applications of Flange
Oil and Gas Industry
In the oil and gas sector, flanges are crucial for connecting pipelines, valves, pumps, and other equipment. They are extensively used in sub-sea drilling operations to connect riser sections, which transport materials such as injection fluids, drilling mud, and produced hydrocarbons from the sea floor to above-sea facilities. The flanges in these applications must ensure consistent face-to-face contact to prevent leaks and withstand high-pressure environments. The use of high-strength fasteners and precise tightening procedures are essential to maintain the integrity of these connections and avoid flange failure due to axial and radial displacements.
Chemical and Petrochemical Industry
Flanges in the chemical and petrochemical industries are used to connect pipes that transport various chemicals, often under high pressure and temperature conditions. These flanges must be resistant to corrosion and chemical reactions. Materials such as stainless steel, alloy steel, and other corrosion-resistant alloys are commonly used to manufacture these flanges. The ability to quickly dismantle and reassemble flanged connections makes maintenance and inspection more manageable, ensuring the safety and efficiency of chemical processing plants.
Water and Wastewater Treatment
In water and wastewater treatment plants, flanges are used to connect pipes, pumps, and valves that handle large volumes of water and waste. The flanges in these systems must be durable and resistant to corrosion caused by constant exposure to water and chemicals used in treatment processes. Common materials for these flanges include ductile iron, stainless steel, and PVC. The ease of assembly and disassembly of flanged connections facilitates regular maintenance and repairs, ensuring the continuous operation of treatment facilities.
Power Generation
Flanges play a vital role in power generation plants, including nuclear, thermal, and hydroelectric plants. They are used to connect various components such as turbines, boilers, heat exchangers, and piping systems. In these applications, flanges must withstand high temperatures and pressures, making materials like alloy steel and stainless steel ideal choices. The precision and reliability of flanged connections are critical to maintaining the safety and efficiency of power generation processes.
Food and Beverage Industry
In the food and beverage industry, flanges are used to connect pipes and equipment involved in the processing, packaging, and distribution of food products. These flanges must meet stringent hygiene standards and be resistant to corrosion caused by food products and cleaning agents. Stainless steel is the preferred material for flanges in this industry due to its corrosion resistance and ease of cleaning. The ability to quickly disassemble flanged connections allows for thorough cleaning and maintenance, ensuring food safety and quality.
Pharmaceutical Industry
The pharmaceutical industry requires flanges that meet high standards of cleanliness and corrosion resistance. Flanges are used to connect piping systems that transport various pharmaceutical ingredients and products. Stainless steel and other corrosion-resistant materials are commonly used to manufacture these flanges. The ease of disassembly and reassembly of flanged connections facilitates regular cleaning and sterilization, which are crucial for maintaining the purity and quality of pharmaceutical products.
Automotive Industry
In the automotive industry, flanges are used in exhaust systems, engine components, and other critical parts of vehicles. These flanges must withstand high temperatures and vibrations, making materials like stainless steel and alloy steel suitable choices. The precision and durability of flanged connections ensure the reliable performance of automotive systems and components.
Construction and Infrastructure
Flanges are used in various construction and infrastructure projects to connect pipes, valves, and other components in plumbing, heating, and cooling systems. These flanges must be durable and resistant to environmental factors such as corrosion and temperature fluctuations. Materials like ductile iron, stainless steel, and PVC are commonly used for flanges in construction applications. The ease of assembly and disassembly of flanged connections facilitates installation and maintenance, ensuring the efficient operation of building systems.
Application Cases
Product/Project | Technical Outcomes | Application Scenarios |
---|---|---|
BOP Stack Alignment System Halliburton Energy Services, Inc. | Ensures proper alignment of connected components, reducing the risk of misalignment and enhancing operational efficiency. | Oil and gas drilling operations requiring precise alignment of blowout preventer stacks. |
Drilling Riser Flanges Grant Prideco, Inc. | Reduces shear in connectors, preventing bolt breakage and flange failure, ensuring reliable and safe drilling operations. | Offshore and onshore drilling operations where high mechanical stress is present. |
Optimal Product Manufacturing Parameter Device Commissariat à l´énergie atomique et aux énergies Alternatives | Optimizes manufacturing parameters to improve product quality and efficiency using causal analysis and rule generation. | Manufacturing industries requiring precise control over product properties and manufacturing processes. |
Polymerized Rubber-Modified Monovinylidene Aromatic Copolymer Dow Global Technologies LLC | Improves toughness and durability of materials, making them suitable for various industrial applications. | Industries requiring high-performance materials, such as automotive and packaging. |
Hole Flanging Process | Enhances flange edge squareness and quality through optimized flange-forming directions and parameters. | Manufacturing processes involving hole expansion and flange formation, such as automotive and aerospace industries. |
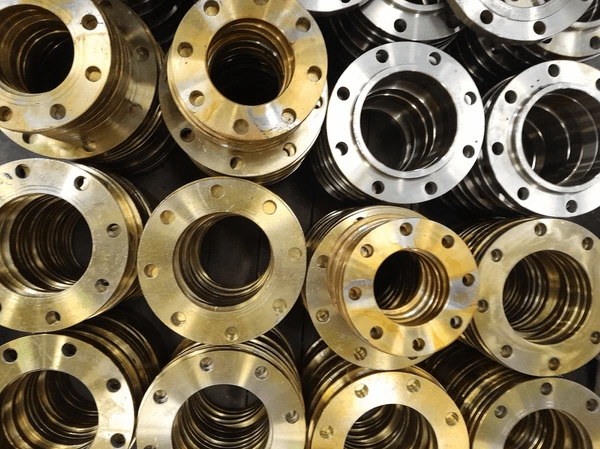
Latest Technical Innovations in Flange
Improved Alignment Mechanisms
One of the significant challenges in flange connections is ensuring proper alignment of the mating surfaces. Misalignment can lead to operational inefficiencies and potential failures. Recent innovations have introduced advanced alignment mechanisms that ensure precise orientation of flanges relative to the connected components. For instance, new designs incorporate self-aligning features that automatically adjust the flange orientation during installation, reducing the risk of misalignment and enhancing the overall reliability of the connection.
Finite Element Analysis (FEA) in Flange Design
Finite Element Analysis (FEA) has become a crucial tool in optimizing flange design. By simulating the flange-forming process, engineers can predict and mitigate issues such as poor flange edge squareness and stress distribution. Recent studies have demonstrated the effectiveness of FEA in understanding the flange-forming mechanism, particularly in the hole flanging process. This process involves expanding a pre-holed workpiece using a larger punch, and FEA helps in analyzing the effects of upward and downward burr orientation on flange quality. Laboratory experiments have validated these simulations, showing that proper burr orientation can significantly improve flange edge squareness and reduce secondary operations.
Advanced Materials and Coatings
The use of advanced materials and coatings has significantly enhanced the performance of flanges in various industries. Composite materials, for example, offer superior strength-to-weight ratios and corrosion resistance compared to traditional metals. Additionally, innovative coatings such as thermal spray coatings and anti-corrosion layers have been developed to extend the lifespan of flanges, especially in harsh environments like sub-sea drilling operations. These coatings provide a protective barrier against corrosive elements, thereby maintaining the integrity of the flange connections over extended periods.
High-Pressure and High-Temperature Applications
Flanges used in high-pressure and high-temperature applications, such as in the oil and gas industry, have seen significant advancements. Innovations include the development of flanges that can withstand extreme conditions without compromising their structural integrity. For example, flanges used in sub-sea drilling operations are designed to maintain consistent face-to-face contact to prevent leaks and ensure proper operation. These flanges are equipped with high-strength fasteners that can bear substantial loads and resist axial and radial displacements caused by manufacturing variances and operational stresses.
Integration of Sensors and Monitoring Systems
The integration of sensors and monitoring systems into flange assemblies is a recent innovation aimed at enhancing operational safety and efficiency. These sensors can monitor parameters such as pressure, temperature, and stress in real-time, providing valuable data for predictive maintenance and early detection of potential issues. By continuously monitoring the condition of flange connections, industries can prevent failures and optimize maintenance schedules, thereby reducing downtime and operational costs.
Customizable and Modular Flange Designs
To cater to the diverse needs of different industries, customizable and modular flange designs have been developed. These designs allow for easy adaptation to specific requirements, such as varying sizes, materials, and connection types. Modular flanges can be quickly assembled and disassembled, facilitating maintenance and reducing installation time. This flexibility is particularly beneficial in industries where rapid changes in operational conditions are common, such as in the chemical and petrochemical sectors.
To get detailed scientific explanations of flange, try Patsnap Eureka.
