
What is an EDM Machine?
Electrical Discharge Machining (EDM) is a non-traditional machining process used to develop complex surface geometries and intricate angles in materials that are difficult to machine using conventional methods. It is widely used in industries such as mold and die making, aerospace, and surgical components manufacturing. The process is applicable to any conductive material with resistivity not exceeding 100 ohm-cm, regardless of its hardness, toughness, or strength.
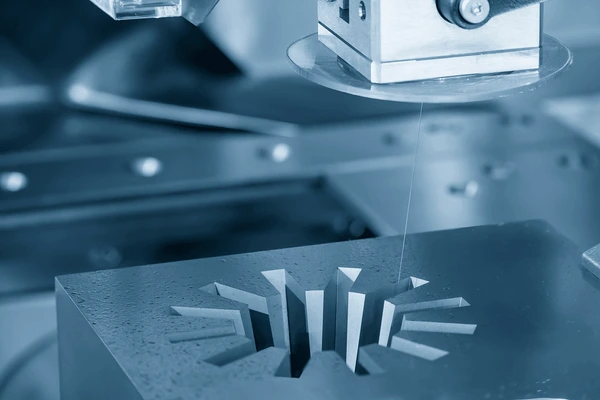
Main Components of an EDM Machine
- Machine Head: Holds and moves the electrode.
- Wire Guide: Guides the wire electrode in wire EDM machines.
- Machining Wire: The wire electrode used in wire EDM.
- Rotary Table and Fixed Table: Used to position and hold the workpiece.
- Fixture: Holds the workpiece in place during machining.
- Pulse Power Supply: Provides the electrical discharges necessary for machining.
- Dielectric System: Includes the dielectric fluid, pumps, and filters to maintain the fluid’s cleanliness and temperature.
How EDM Machines Work
The EDM process involves generating a series of electrical discharges between the electrode and the workpiece, which are separated by a small gap filled with a dielectric fluid. The key steps in the EDM process are as follows:
- Gap Ionization: A servo-controlled feed mechanism moves the electrode towards the workpiece until the gap is small enough to ionize the dielectric fluid by the applied voltage.
- Spark Generation: A short-duration electrical discharge occurs, creating a plasma channel and generating temperatures between 8000°C and 20,000°C. This intense heat causes localized melting and vaporization of the material from both the electrode and the workpiece.
- Material Removal: The molten material is flushed away by the dielectric fluid, and the process repeats at the next closest point between the electrode and the workpiece, gradually eroding the material to form the desired shape.
Types of EDM Machines
- Wire EDM: Uses a thin wire as the electrode to cut intricate shapes and contours. It is particularly useful for machining complex geometries and hard materials.
- Sinker EDM: Uses a shaped electrode (usually made of graphite or copper) to create cavities and intricate shapes in the workpiece.
- Micro EDM: Designed for high-precision and high-performance machining of micro-scale components. It employs advanced control systems and piezoelectric actuators for precise movement and gap control.
Materials Machined with EDM
EDM is particularly effective for machining hard and electrically conductive materials that are difficult to machine using conventional methods. These materials include:
- Tool Steels: Widely used in mold and die making due to their hardness and wear resistance.
- Tungsten Carbide: Commonly used in cutting tools and wear-resistant parts.
- Titanium Alloys: Utilized in aerospace and medical applications for their high strength-to-weight ratio and corrosion resistance.
- Superalloys (e.g., Inconel, Hastelloy): Used in high-temperature applications such as turbine blades and aerospace components.
- Graphite: Often used as an electrode material due to its high melting point and electrical conductivity.
Advantages and Disadvantages of EDM Machines
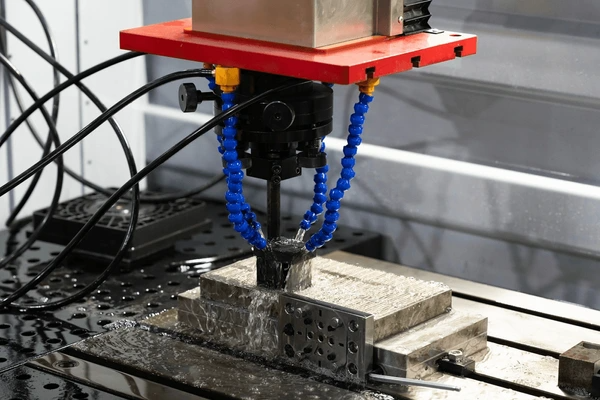
Advantages of EDM Machines
- Non-Traditional Process: EDM generates no cutting forces, allowing for the production of small, fragile pieces without deformation.
- Precision and Intricacy: EDM can produce intricate parts with superior finishes and high tolerance limits, making it ideal for complex shapes and fine details.
- Material Versatility: EDM can machine extremely hard materials, including alloys, tool steels, and tungsten carbides, without the limitations imposed by conventional machining methods.
- Minimal Operator Intervention: The process requires minimal operator intervention, reducing the risk of human error and increasing efficiency.
Disadvantages of EDM Machines
- Low Material Removal Rate (MRR): Compared to traditional machining methods like milling and turning, EDM has a lower MRR, making it less efficient for large-scale material removal.
- Electrical Conductivity Requirement: The workpiece material must be electrically conductive, limiting the range of materials that can be machined using EDM.
- Excessive Tool Wear: The tool electrode experiences significant wear during the machining process, which can affect the accuracy and quality of the machined parts.
- Complex Parameter Optimization: Achieving optimal results requires careful optimization of various parameters, making the process more complicated and time-consuming.
EDM vs. Other Machining Methods
- Material Removal Mechanism: EDM uses electrical discharges to erode material, whereas conventional machining methods like milling and turning use mechanical forces to cut material. This allows EDM to machine very hard materials that would be difficult or impossible to machine with conventional methods.
- Surface Finish and Precision: EDM can achieve very fine surface finishes and high precision, making it suitable for applications requiring intricate shapes and tight tolerances. Conventional machining may struggle to achieve the same level of detail and surface quality on hard materials.
- Tool Wear: In EDM, tool wear is a significant issue as the electrode also erodes during the process. In contrast, conventional machining tools wear down more slowly but can still be a concern when machining hard materials.
EDM vs. Other Non-Conventional Methods
- Laser Machining: Laser machining is another non-conventional method that uses focused laser beams to cut materials. While both EDM and laser machining can handle hard materials, EDM is generally better for achieving high precision and fine surface finishes. Laser machining, however, can be faster and is not limited to conductive materials.
- Ultrasonic Machining: Ultrasonic machining uses high-frequency vibrations to remove material. It is effective for brittle materials like ceramics and glass, which are not suitable for EDM. However, EDM is preferred for conductive materials and can achieve better precision and surface quality.
Applications of EDM Machine
Automotive Industry
- Precision Component Manufacturing: EDM is extensively used for manufacturing high-precision components such as fuel injectors, engine parts, and transmission components. The ability to machine hard materials with high accuracy makes EDM ideal for these applications.
- Mold and Die Making: EDM is crucial in creating molds and dies for automotive parts, ensuring high precision and surface finish. This is particularly important for parts that require complex geometries and tight tolerances.
Aerospace Industry
- Turbine Blade Manufacturing: EDM is used to manufacture turbine blades and other components that require intricate shapes and high precision. The process allows for the machining of superalloys and other hard materials used in aerospace applications.
- Component Repair: EDM is also employed in the repair of aerospace components, such as removing damaged sections and precisely machining new parts to fit.
Medical Devices
- Surgical Instruments: The precision and ability to machine small, intricate parts make EDM suitable for manufacturing surgical instruments and medical implants.
- Micro-Machining: EDM is used for micro-machining applications in the medical field, such as creating tiny holes and complex shapes in medical devices.
Tool and Die Industry
- Die Sinking: EDM is widely used for die sinking applications, where complex shapes are machined into hard materials to create dies for various manufacturing processes.
- Electrode Manufacturing: EDM is also used to create electrodes for other EDM processes, ensuring high precision and repeatability.
Electronics Industry
- Microelectronics: EDM is employed in the manufacturing of microelectronic components, where precision and the ability to machine small features are critical.
- Connector Manufacturing: EDM is used to create precise connectors and other components used in electronic devices.
General Manufacturing
- Prototyping: EDM is used for rapid prototyping, allowing manufacturers to quickly create and test new designs.
- Custom Parts: The flexibility of EDM makes it suitable for producing custom parts with complex geometries and tight tolerances.
Application Cases
Product/Project | Technical Outcomes | Application Scenarios |
---|---|---|
Precision Component Manufacturing | High accuracy in machining hard materials, ideal for fuel injectors, engine parts, and transmission components. | Automotive industry for high-precision components. |
Mold and Die Making | Ensures high precision and surface finish, crucial for parts with complex geometries and tight tolerances. | Automotive industry for creating molds and dies. |
Turbine Blade Manufacturing | Allows machining of superalloys and other hard materials with intricate shapes and high precision. | Aerospace industry for turbine blades and other components. |
Component Repair | Enables precise machining of new parts to fit, useful for removing damaged sections. | Aerospace industry for repairing components. |
Surgical Instruments | Precision and ability to machine small, intricate parts. | Medical industry for manufacturing surgical instruments and medical implants. |
Latest Technical Innovations in EDM Machine
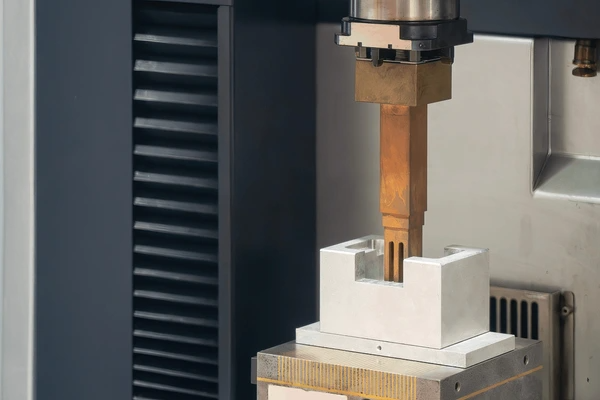
Advanced Control Systems
The control system is a critical component of EDM machines, significantly influencing machining efficiency and quality. Recent innovations have focused on optimizing parameter control, servo control, and numerical control systems. These advancements aim to meet the increasing demands for higher machining precision and efficiency. For instance, the development of adaptive control technology based on gap detection and servo feed systems has enhanced the reliability and long-term unmanned operation of CNC EDM machines. Additionally, the integration of expert systems and decision control software has further improved the control accuracy and operational stability.
Micro-EDM Technologies
Micro-EDM has seen substantial advancements, particularly in the development of high-precision and high-performance micro-EDM machine tools. Key technologies include:
- Macro-Micro Servo Control Systems: Utilizing piezoelectric ceramics to achieve displacement as small as 3.42 nm, significantly improving the machining gap state and enhancing efficiency and quality.
- Reverse Machining Systems: Combining block electrode reverse machining and wire electrode discharge grinding (WEDG) to fabricate micro-electrodes with diameters as small as 4 μm.
- Ultra-Micro Energy RC Power Supply: Reducing single pulse energy to pico-joule levels, which is crucial for stable micro-EDM operations.
Discharge Grinding
A novel method of discharge grinding using wire EDM machines has been developed. This technique involves modifying the pulse power supply to reduce discharge energy per spark, enabling the machining of mini-sized shafts with diameters as small as 0.08 mm and achieving surface roughness of Ra 0.473 μm. This innovation allows for precise and efficient grinding of small components, expanding the capabilities of wire EDM machines.
Powder-Mixed EDM (PMEDM)
PMEDM represents a significant advancement in surface modification techniques. By mixing thermally and electrically conductive powders with dielectric fluids, PMEDM enhances machining performance and alters surface characteristics. This method reduces the shielding strength of the dielectric fluid, increases the gap between the electrode and workpiece by up to 200%, and produces shallower craters on the machined surface. PMEDM also allows for simultaneous machining and coating of workpieces, addressing many limitations of traditional EDM processes.
Innovations in EDM Machine Design
Recent developments in EDM machine design include the creation of small-size EDM machines tailored for machining geometrically complex shapes and hard materials. These machines incorporate advanced pulse generators, automatic control mechanisms, and efficient pump and filter systems. Such designs aim to meet specific domestic demands for precision and surface roughness in machining operations.
To get detailed scientific explanations of EDM machines, try Patsnap Eureka.

Learn more
Shock Cords: Versatile Strength for Every Need
Pressure Switches: Small Devices, Big Impact
Unveiling The Lead Screw: Its Mechanism, Benefits, And Beyond