
What Is DLP 3D Printing?
DLP 3D printing, short for Digital Light Processing, is revolutionizing additive manufacturing by delivering precision and speed. This innovative technique builds three-dimensional objects layer by layer using a digital projector. By curing photosensitive resin with UV light, DLP ensures each layer is solidified quickly and accurately. Unlike other 3D printing methods, it cures entire layers at once, resulting in faster production and higher-quality parts. In this article, we’ll explore how DLP 3D printing works, its benefits, and its role in modern manufacturing.
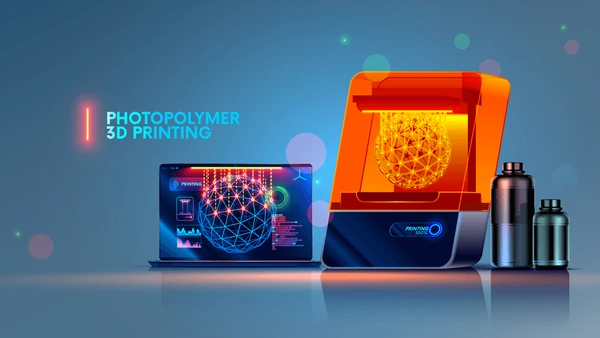
How DLP 3D Printing Works
The Role of Light Projection
DLP 3D printing relies on a digital projector to shine light onto a vat filled with liquid photopolymer resin. The projector displays a precise pattern for each layer of the 3D model. When the light hits the resin, it cures the exposed areas, forming a solid layer.
Layer-by-Layer Printing Process
After curing the first layer, the build platform moves slightly, making room for the next layer. The projector then displays the next pattern, and the resin cures again to form the next layer. This layer-by-layer approach continues until the object is fully formed.
Speed and Efficiency
Unlike other methods like SLA or FDM, DLP cures entire layers at once rather than point by point. This significantly speeds up the process while maintaining high accuracy. This efficiency makes DLP ideal for applications where both speed and quality are essential.
Precision and Detail
The resolution in DLP 3D printing depends on the pixel count of the projector. Higher pixel counts allow for greater detail and smoother surfaces. This precision makes it possible to create intricate designs, such as dental models, jewelry, and industrial components.
Versatility and Applications
DLP 3D printing excels in creating small, detailed objects with consistent quality. Its ability to combine speed, accuracy, and intricate detailing makes it a popular choice across industries requiring reliable and efficient prototyping.
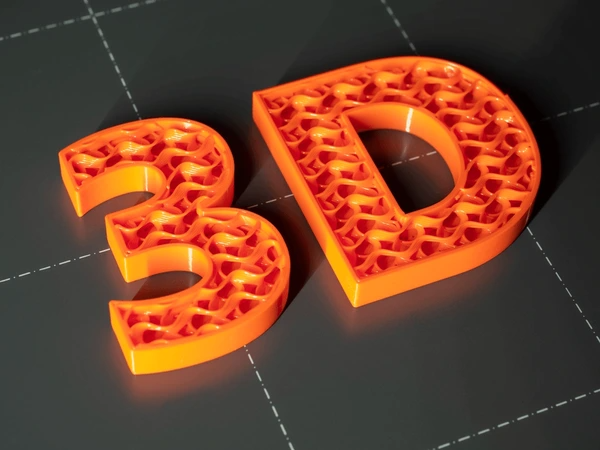
Materials Used in DLP 3D Printing
Photopolymers: The Foundation of DLP Printing
Photopolymers are the most commonly used materials in this technology. They consist of monomers, oligomers, and photoinitiators, which solidify upon exposure to light. This light-induced polymerization process transforms liquid resin into solid layers, creating precise and durable 3D objects.
Monomers: Building the Polymer Network
Monomers are the primary building blocks of photopolymers. Common monomers include methyl methacrylate, ethylene glycol diacrylate, and hydroxyethyl acrylate. By selecting different monomers, manufacturers can tailor properties such as strength, flexibility, and transparency.
Oligomers: Enhancing Mechanical Strength
Oligomers, which are low-molecular-weight polymers, play a crucial role in improving the mechanical properties of printed parts. Acting as crosslinking agents, they enhance durability and rigidity, making the final products suitable for various demanding applications.
Photoinitiators: Triggering the Reaction
Photoinitiators are responsible for starting the polymerization process when exposed to light. Common examples include camphorquinone and iridium complexes. These compounds ensure accurate curing and contribute to the precision and quality of each printed layer.
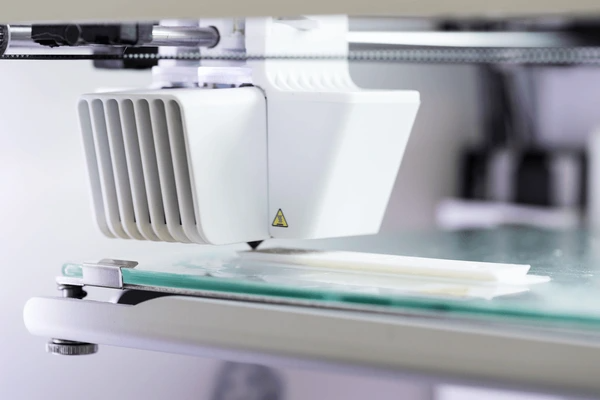
Applications of DLP 3D Printing
Creating High-Resolution Metallic Parts
DLP technology delivers precision metal printing for applications needing excellent mechanical, thermal, and electrical properties. Lithographic metal additive manufacturing (LMAM) allows the production of intricate, hollow structures with unmatched accuracy. This approach is perfect for small devices like microheat exchangers and biomedical implants.
Advancing Ceramic and Composite Materials
Ceramic fabrication benefits greatly from DLP’s speed and precision. For example, barium titanate (BaTiO3) nanocomposites improve electrical properties like dielectric constants and polarization values. These characteristics make them ideal for piezoelectric elements in advanced electronics.
Manufacturing Orthodontic Appliances
DLP is transforming orthodontics by enabling the production of polymer-based appliances with biocompatible materials like Dental LT Clear resin. Custom printers have been developed to optimize surface smoothness and improve the quality of these personalized dental solutions.
Revolutionizing Tissue Engineering and Biomedical Applications
This technology supports tissue engineering by producing detailed, complex structures tailored to patient needs. From prosthetics to anatomical models, DLP provides precision solutions for biomedical applications, improving customization and functionality.
Producing Abrasion-Resistant Parts
Manufacturers use DLP to create durable, abrasion-resistant parts by reinforcing resins with fumed silica. This innovation reduces material waste and machining costs, helping businesses lower their carbon footprint while increasing product longevity.
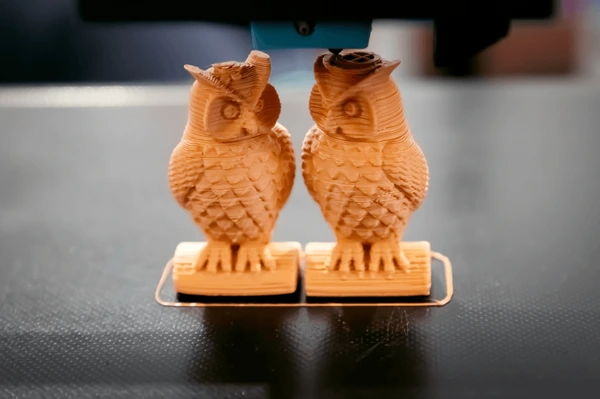
Future Trends in DLP 3D Printing Technology
1. Innovations in Materials
- Hydroxyapatite Ceramics: Researchers are advancing the use of hydroxyapatite ceramics for bone repair and medical implants. These materials require precise printing methods to ensure the structural integrity and porosity necessary for their applications.
- Transparent Materials: Development is underway for materials like Si3N4-SiO2 ceramics, which are ideal for harsh environments. These materials offer excellent wave-transparent performance, making them valuable in aerospace communication and guidance systems.
2. Improved Resolution and Precision
- Advanced Printing Strategies: Techniques like falling-down methods are enabling more accurate control over layer thickness and curing processes.
- Enhanced Material Properties: These strategies improve the mechanical strength and microstructural integrity of printed components, meeting the demands of complex designs and industrial applications.
3. Expanding Applications Across Industries
- Industrial Production: 3D printing is now widely used in the aerospace, automotive, healthcare, and electronics industries. Its ability to produce complex geometries with minimal material waste makes it a top choice for scalable production.
- Chemical Research: In the chemical industry, this technology supports digital chemical synthesis, automation, and material development, showcasing its adaptability.
4. Optimizing the Printing Process
- Refining Parameters: Researchers are working to optimize photoinitiators, additive dyes, and exposure times to enhance product quality.
- Process-Property Relationships: Studies aim to understand how printing parameters influence material properties and performance, improving efficiency and reducing costs.
5. Market Growth and Sustainability Trends
- Growing Market Demand: The high-resolution 3D printing market is expanding rapidly as industries invest in research and development.
- Sustainable Manufacturing: Its waste-reducing capabilities make this technology appealing for companies seeking eco-friendly manufacturing practices.
To get detailed scientific explanations of DLP 3D Printing, try Patsnap Eureka.
