
What Is Die Casting?
Die casting is a manufacturing process in which molten metal is injected under high pressure and speed into a reusable steel mold or die to produce near-net-shape castings.
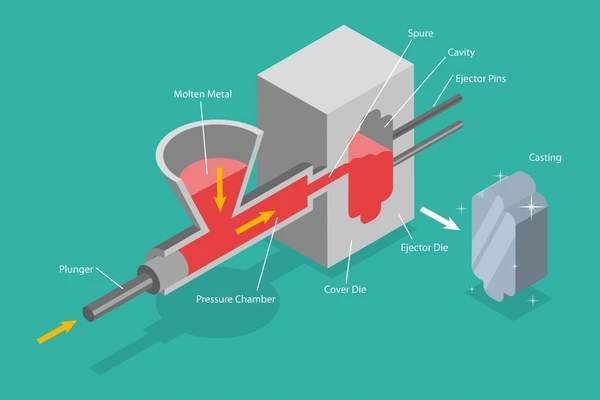
How Die Casting Works
- Mold Preparation: The die or mold is prepared by applying a lubricant spray to facilitate the removal of the casting after solidification. The mold consists of two halves that define the cavity shape of the desired part.
- Melt Injection: Molten metal, typically non-ferrous alloys like aluminum, zinc, or magnesium, is injected into the die cavity through a shot sleeve or gooseneck. The injection can be done using either a hot chamber or cold chamber system.
- Solidification and Cooling: The molten metal rapidly solidifies and cools inside the die cavity due to the high thermal conductivity of the steel mold.
- Ejection: Once the casting has solidified, the die is opened, and ejector pins are used to remove the solidified part from the mold cavity.
Types of Die Casting
- Hot Chamber Die Casting: The injection system is submerged in the molten metal bath, suitable for low-melting-point alloys like zinc.
- Cold Chamber Die Casting: The molten metal is transferred from a separate furnace into the injection system, suitable for higher-melting-point alloys like aluminum.
- Vacuum Die Casting: A vacuum is applied to the die cavity to remove air and gases, improving the quality and mechanical properties of the castings.
- Squeeze Die Casting: The molten metal is solidified under high pressure, resulting in a denser and higher-quality casting with minimal porosity.
Common Materials Used in Die Casting
Aluminum Alloys
Aluminum alloys are the most widely used materials in die casting due to their excellent castability, high strength-to-weight ratio, and corrosion resistance. Common aluminum alloys for die casting include:
- Al-Si alloys (e.g., A380, A384, A413) – good fluidity, moderate strength
- Al-Cu alloys (e.g., A206, A201) – high strength, wear resistance
- Al-Mg alloys (e.g., AM60, AM50) – good corrosion resistance, weldability
Magnesium Alloys
Magnesium alloys offer the highest strength-to-weight ratio among die casting alloys, making them suitable for lightweight applications. Common magnesium alloys include:
- AM60, AM50 – good castability, corrosion resistance
- AZ91, AM20 – high strength, creep resistance
Zinc Alloys
Zinc alloys are cost-effective and have excellent fluidity, making them suitable for thin-walled and intricate castings. Common zinc alloys are:
- Zamak alloys (Zn-Al-Cu-Mg) – good castability, moderate strength
- ZA alloys (Zn-Al) – high impact strength, corrosion resistance
Copper-based Alloys
Copper-based alloys offer high strength, wear resistance, and thermal conductivity, but have limited castability. Common copper alloys include:
- Brass alloys (Cu-Zn) – good corrosion resistance, machinability
- Bronze alloys (Cu-Sn) – high strength, wear resistance
Advantages of Die Casting
- High production rate: Die casting allows for rapid production of complex parts with excellent dimensional accuracy and surface finish. The process can produce tens of thousands of castings in rapid succession.
- Near-net-shape capability: Die castings can be produced with intricate details, thin walls, and complex geometries, reducing the need for subsequent machining operations. This results in cost savings and material efficiency.
- Excellent mechanical properties: Die cast parts exhibit high strength, hardness, and density due to the rapid solidification and heat transfer characteristics of the process.
- Versatility: Die casting can be used with a wide range of non-ferrous alloys, including aluminum, magnesium, zinc, and copper-based alloys, allowing for diverse applications.
Challenges in Die Casting
- Porosity and gas entrapment: The high injection speeds and rapid solidification can lead to the formation of pores, gas entrapment, and shrinkage cavities in the castings. This can compromise the mechanical properties and surface quality.
- Die wear and soldering: The high temperatures and pressures involved in die casting can cause die wear, heat checking, and soldering of the molten metal to the die surface, reducing die life and increasing maintenance costs.
- Dimensional accuracy limitations: Thermal deformations during the casting process can affect the dimensional accuracy of the castings, sometimes requiring post-machining operations.
- Design limitations: Die casting imposes certain design constraints, such as draft angles, uniform wall thickness, and limitations on undercuts, due to the nature of the process and the need for die ejection.
- Environmental concerns: Traditional die casting processes may involve the use of lubricants and release agents, which can generate effluents and environmental concerns.
Applications of Die Casting
Automotive Industry
- Engine components (cylinder heads, engine blocks, pistons, etc.)
- Transmission housings and gearbox components
- Suspension and steering system parts
- Structural components (chassis, body panels, etc.)
- Decorative and trim components
Aerospace Industry
- Airframe components (structural fittings, brackets, etc.)
- Engine components (housings, impellers, etc.)
- Avionics and electronics enclosures
Electronics and Electrical Industry
- Housings and enclosures for consumer electronics, appliances, and industrial equipment
- Connectors, switches, and other electrical components
- Heat sinks and thermal management components
Construction and Building Industry
- Door and window hardware (handles, hinges, locks, etc.)
- Plumbing fixtures and fittings
- Architectural hardware and decorative elements
Other Industries
- Medical and dental equipment (surgical instruments, prosthetics, etc.)
- Sporting goods and recreational equipment
- Furniture and home appliances
- Toys and consumer products
Latest Technical Innovations in Die Casting
Machinery and Process Innovations
- Copper Rotor Die Casting: A pressure die casting process and machine to produce highly efficient copper rotors for AC induction motors, facilitating improved efficiency and performance by enabling maximum copper filling with minimum porosity.
- Semi-Solid Die Casting: A process involving the preparation of semi-solid slurries of alloys and their injection into dies, resulting in improved mechanical properties and reduced defects.
- Super Slow Speed Die Casting: An ultra-slow injection speed technique that enhances the quality of castings by minimizing turbulence and air entrapment.
Material and Alloy Innovations
- Refractory Metal Intermetallic Composites: The use of composite materials like niobium silicide, molybdenum disilicide, and others as charge materials in die casting systems, enabling the production of high-temperature components.
- Lightweight Alloys: The development of advanced lightweight alloys, such as aluminum and magnesium alloys, for automotive applications, driving innovations in die casting technologies to accommodate these materials.
Process Optimization and Control
- Computer Numerical Simulation: The application of numerical simulations to optimize die casting processes, including mold design, gating systems, and process parameters.
- Vacuum Die Casting: A technique that involves removing gases from the die cavity during casting, reducing porosity and improving mechanical properties and surface quality.
- Integrated Manufacturing Systems: The implementation of computer-integrated manufacturing systems (CIMS) in die casting, enabling process automation, monitoring, and control.
Mold and Die Innovations
Composite Liners: The development of composite liners or inserts for shot chambers, featuring erosion-resistant coatings on refractory metal liners, improving service life for casting corrosive metals and alloys.
FAQs
- What is the main advantage of die casting over other methods?
Die casting offers high precision and excellent surface finishes, making it ideal for mass production of complex parts. - Which metals are best for die casting?
Common metals include aluminum, zinc, magnesium, and copper alloys, each suited for specific applications. - How long do die casting molds last?
Die casting molds are highly durable, lasting for thousands of production cycles depending on usage and maintenance. - What are common defects in die casting?
Defects include porosity, warping, and incomplete fills, often caused by improper temperature or pressure settings. - Is die casting environmentally friendly?
Die casting is efficient and minimizes material waste, and many metals used are recyclable, making it relatively eco-friendly.
To get detailed scientific explanations of die casting, try Patsnap Eureka.
