
How Does a VFD Work?
A Variable Frequency Drive (VFD) is a game-changing device in motor control, offering precise regulation of an AC motor’s speed by adjusting the frequency and voltage supplied. Widely used across industries, VFDs enhance energy efficiency, extend equipment lifespan, and enable greater process control. In this article, we’ll explore how VFDs work, their benefits, and why they are essential in modern industrial and commercial applications.
Key Components of a VFD
1. Rectifier
- Converts incoming AC power into DC voltage, serving as the first stage of power conversion.
- This process enables the drive to create a controllable DC voltage for further processing.
2. DC Link
- Filters and stabilizes the rectified DC voltage, ensuring a steady and smooth power supply.
- The DC link acts as an intermediary stage between the rectifier and inverter.
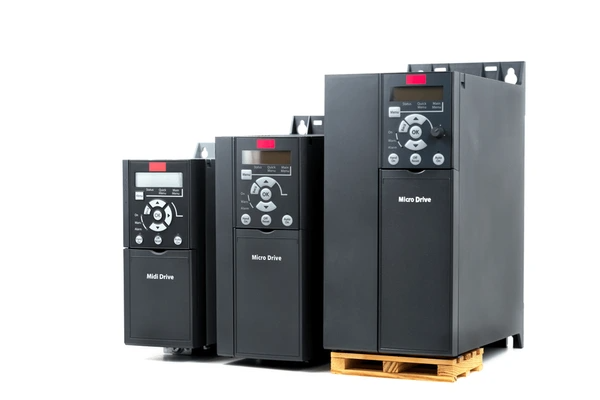
3. Inverter
- Converts the filtered DC voltage back into AC, with adjustable frequency and voltage.
- Power semiconductor switches, such as IGBTs, allow precise control over the output power characteristics.
4. Control Unit
- Uses a microprocessor to regulate the inverter’s output based on the desired motor speed and load conditions.
- The control unit ensures smooth operation and optimizes performance according to user-defined parameters.
How Speed Control Works
- The drive adjusts motor speed by varying the frequency of the AC output.
- It maintains a consistent voltage-to-frequency ratio to ensure rated torque is produced.
- This approach provides precise control over motor speed, torque, and energy consumption.
Benefits of Using a VFD
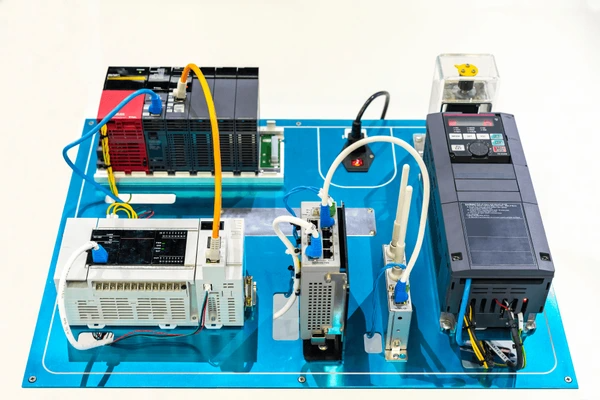
Energy Efficiency and Cost Savings
- Variable speed drives enable precise motor control by adjusting speed and torque based on load demands.
- They significantly reduce energy consumption, especially in variable torque applications like fans and pumps.
- This energy efficiency often results in a quick return on investment, typically within just a few years.
Improved Process Control and Flexibility
- Drives allow advanced control over speed and torque profiles, optimizing processes for better performance.
- Soft-starting motors reduces mechanical stress and enhances equipment longevity.
- They offer precise speed regulation, torque control, and load-sharing capabilities, adding flexibility to various applications.
Reduced Mechanical Stress and Maintenance
- Soft-start and soft-stop functions minimize mechanical stress on motors and connected equipment.
- This reduces wear and tear, extending equipment lifespan and lowering maintenance costs.
- By eliminating mechanical speed control components like gearboxes, they further simplify maintenance needs.
Lower Starting Currents and Torque Shock
- Drives reduce starting currents, easing electrical stress on the power distribution system.
- They prevent torque shocks during motor startup, protecting driven equipment and prolonging its service life.
Versatility and Compatibility
- Compatible with a wide range of AC motors, including induction and synchronous models, they offer unmatched versatility.
- They support diverse industrial processes such as pumping, ventilation, and material handling, adapting to various applications.
Common Applications of VFDs
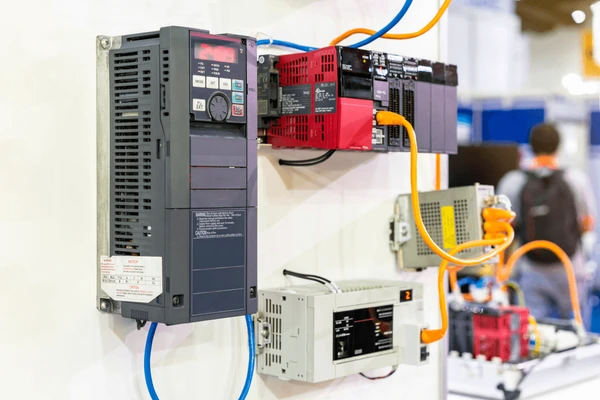
1. HVAC and Chiller Systems
- Drives improve HVAC and chiller efficiency by enabling soft motor starts and reducing energy consumption.
- They lower short-circuit currents and enhance load-shedding capabilities, ensuring smoother system operation.
2. Pumping Systems
- In water treatment and desalination, they offer efficient flow control and reduce energy usage.
- These systems eliminate the need for mechanical regulators, simplifying operations and lowering costs.
3. Industrial Machinery
- Drives control motor speeds in machinery like blowers, conveyors, extruders, and fans.
- This ensures precise process control while delivering substantial energy savings for industrial applications.
4. Automotive and Transportation
- Electric vehicles use these drives to power traction motors at variable speeds, increasing efficiency and range.
- They provide smoother acceleration and improved energy management for transportation systems.
5. Material Handling
- Drives ensure smooth acceleration and deceleration of conveyors, cranes, and hoists.
- This reduces mechanical stress, lowers energy consumption, and extends the lifespan of handling equipment.
6. Compressors
- By adjusting motor speed based on load requirements, they optimize air compressor operations.
- This leads to significant energy savings and improved system reliability.
Application Cases
Product/Project | Technical Outcomes | Application Scenarios |
---|---|---|
VFD Display Circuit Shenzhen Topband Co., Ltd. | Utilizes a rectified and regulated power supply and microprocessor to output segment codes and filament on-off signals, achieving low-cost VFD display lighting and brightness uniformity. | Display applications requiring cost-effective and uniform brightness control. |
VFD for AC Induction Motors | Provides an introduction to the use of VFD control for AC induction motors and how to effectively specify AC induction motors for VFD applications. | Cement plant design and operation involving AC induction motor control. |
Scalable Multi-level Power Converter Magna International, Inc. | Utilizes 2-level converters with GaN transistors to achieve efficient AC power conversion for motor drives, capable of handling 800V DC input, offering reduced losses and simplified cooling. | Motor drive applications requiring high efficiency and simplified thermal management. |
Motor Drive Topologies for Electrified Vehicles Magna International, Inc. | Employs a current-source inverter system with wide-bandgap transistors, enhancing efficiency and reducing costs for electric motor drives in electrified vehicles. | Traction and charging systems in electrified vehicles. |
Integrated Direct Mount Branch Protection for VFD Eaton Intelligent Power Ltd. | Integrates a branch protection device directly onto a variable frequency drive, reducing system size and mounting complexity while providing cost-effective and easily installable motor control with enhanced power protection. | Motor control systems requiring compact design and integrated power protection. |
Emerging Trends in Motor Drive Technology
1. Wide-Bandgap Semiconductors
- Innovations in Silicon Carbide (SiC) and Gallium Nitride (GaN) enable higher efficiency and power density in motor drives.
2. Advanced Control Algorithms
- Modern drives use sophisticated algorithms for better precision, torque control, and energy optimization.
3. IoT Integration
IoT-enabled systems offer real-time monitoring, intelligent energy management, and predictive maintenance for improved reliability.
To get detailed scientific explanations of variable frequency drives, try Patsnap Eureka.
