
What is a Purge Valve?
A purge valve controls the flow of fluids, especially in systems where gas or vapor removal is essential. It’s widely used in industrial applications like fuel cell systems, evaporative emission control (EVAP) systems in vehicles, and pneumatic systems. This article will explore how purge valves work, their types, and their common uses.
Types of Purge Valves
Electromagnetic Purge Valve: This valve uses an electromagnetic coil to control fluid flow, ensuring precise and consistent flow with minimal pulsation.
Solenoid-Actuated Purge Valve: With solenoid valves, this design allows for adjustable flow rates and improved flow characteristics through multiple passages.
Dual Armature Purge Valve: Common in EVAP systems, this valve features two independent armatures that control the flow of fuel vapors through separate outlets.
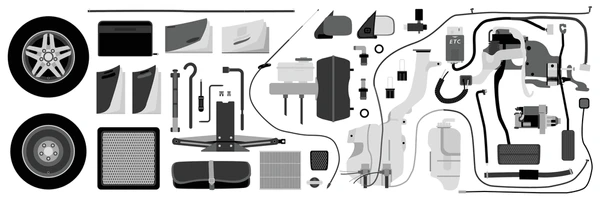
How Does a Purge Valve Work?
A purge valve has a housing, diaphragm, control chambers, and exhaust ports. The diaphragm moves between open and closed positions, regulating fluid flow. It works by balancing pressure forces from the inlet and control chambers with a spring force. This determines whether the valve is open or closed.
Signs of a Faulty Purge Valve
Error Messages and Alerts
- Low Suction:
The LCD screen displays a low suction error, accompanied by light and sound warnings. - VARD Sensors Failure:
A failure in the VARD sensors triggers error messages on the LCD screen. - Pinch Valve Failure:
Error messages and warnings about improper pinch valve rod movement appear on the LCD screen. - VARD Cable Continuity Check Failure:
If the VARD cable connection breaks, an error message appears, indicating an open circuit. - FIL Error State:
Blood detected in the purge line for a certain duration triggers error messages and cautions.
Mechanical and Operational Issues:
- Vacuum Threshold Level:
The vacuum line segment must meet a threshold, measured via sensors and an isolation filter. A failure could signal an issue with the valve. - Piezoelectric Element Failure:
If the lower piezoelectric elements detect air and the upper ones detect fluid, it indicates a potential valve issue.
Required Actions
In these cases, the perfusionist should take corrective action. This might involve replacing the AAR controller, VARD cable, or manually opening the pinch valve to purge air.
Purge Valve vs. EGR Valve: Key Differences
unction and Purpose
Purge Valve:
This component channels fuel vapors from the EVAP system into the engine intake manifold, reducing evaporative emissions and preventing fuel vapor release into the atmosphere. It’s a key part of the EVAP system, which captures and recycles fuel vapors.
EGR Valve:
The EGR valve recirculates exhaust gases back into the intake manifold, lowering the formation of harmful nitrogen oxides (NOx). By recycling exhaust gases, it helps improve both emissions control and fuel efficiency.
Operation
Purge Valve:
When the engine is running, the valve opens, allowing fuel vapors to flow into the intake manifold. The engine control unit (ECU) regulates the valve’s function based on factors like intake manifold pressure and engine speed.
EGR Valve:
This valve opens and closes according to ECU signals, controlling exhaust gas flow into the intake manifold. Depending on the design, it can be actuated mechanically, electrically, or hydraulically to adjust recirculated exhaust gas.
Location and System Integration
Purge Valve:
Typically found in the EVAP system, the valve is connected to components like the canister, fuel tank, and intake manifold. It operates within a closed-loop system that captures and recycles fuel vapors.
EGR Valve:
Located in the exhaust system, the EGR valve links the exhaust manifold to the intake manifold. It’s crucial for the emissions control system, working alongside other components like the catalytic converter.
Control and Regulation
Purge Valve:
The ECU manages the valve’s operation based on intake pressure, engine speed, and other factors. This ensures efficient fuel vapor management while maintaining the integrity of the EVAP system.
EGR Valve:
The ECU also controls this valve, adjusting its opening to regulate the amount of exhaust gas recirculated. This precise control helps optimize emissions and engine performance based on load, speed, and temperature.
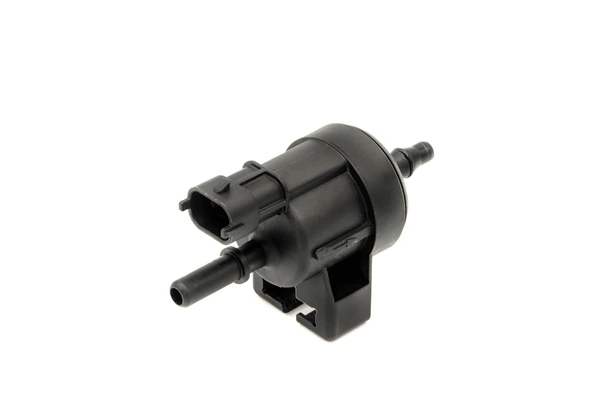
How to Test a Purge Valve
Flow Rate Measurement
Pressurized fluid flows through the valve, and a flow measuring system tracks the rate. This ensures the valve operates within the expected parameters.
Purge Fluid Usage
Purge fluid flows through the valve in the opposite direction of normal operation. This helps remove contaminants that could impact the valve’s function.
Leak Testing
After purging, the system is pressurized and checked for leaks. This step ensures the valve has effectively removed air or contaminants.
Applications of Purge Valve
Air-Drying Devices and Pressurized Air Systems:
Purge valves control exhaust air flow in air-drying devices. They have a body and piston that manage airflow through passages. This system removes air and moisture, boosting efficiency and longevity in pressurized air systems, such as those in commercial vehicles.
Hydronic Heating and Cooling Systems:
In hydronic systems, purge valves eliminate air bubbles and pockets that cause inefficiency. Placed on the secondary loop, they ensure better performance during installation and maintenance.
Capacitor Applications:
Purge valves regulate fluid or gas flow in capacitors. They include a housing, cavity, and lumen to manage fluid flow, ensuring smooth operation.
Microfluidic Applications:
Gas purge valves in microfluidic chips remove excess gases, aligning liquids without sensors. These valves use a three-layer design to remove gases efficiently in lab-on-a-chip applications.
Fuel Cells:
In PEM fuel cells, purge valves at the anode remove nitrogen buildup. This reduces impedance and minimizes hydrogen wastage, improving overall efficiency.
Vacuum Cleaners and Dust Separators:
Purge valves introduce air into the flow when pressure drops, ensuring cyclonic dust separators work effectively and prevent motor overheating.
Valve Rod Cooling in Butterfly Valves:
Purge valves inject cool fluid into butterfly valves transporting high-temperature fluids. This protects the valve rod from overheating and prevents dust invasion.
Heart-Assist Devices:
In heart-assist devices, tri-leaflet valve designs with purge flows improve blood circulation and reduce thromboembolic complications, ensuring smoother blood flow.
Application Cases
Product/Project | Technical Outcomes | Application Scenarios |
---|---|---|
Air-Drying Device with Purge Valve ZF CV Systems Europe BV | Reduces the possibility of use of integrated safety valves, ensuring efficient removal of air and moisture from pressurized air systems. | Pressurized air-based systems in commercial vehicles. |
Purge/Fill Valve NIBCO, Inc. | Hydraulically separates flow in primary and secondary loops, ensuring efficient air removal during installation and maintenance. | Hydronic heating and cooling systems. |
Purge Valve for Capacitor Systematic Power Manufacturing LLC | Prevents rapid deterioration of EDLC or pseudocapacitor by managing rippling voltage or over voltage, enhancing the life of energy storage devices. | Capacitor applications in electrical apparatus. |
Purge Valve for Vacuum Cleaner Dyson Technology Ltd. | Ensures efficient operation of cyclonic dust separator apparatus by reliably operating in response to airflow reduction, reducing motor overheating risk. | Vacuum cleaners with cyclonic dust separator apparatus. |
Gas Purge Valve with Activation Sensor A.R.I. Flow Control Accessories Ltd. | Monitors and transmits parameters associated with the valve for remote control, enhancing system monitoring and control. | Fluid systems requiring remote monitoring and control. |
Latest Technical Innovations in Purge Valve
Enhanced Efficiency
- Material Selection: Advanced materials like high-performance alloys and ceramics increase durability and resistance to extreme temperatures and corrosion.
- Valve Design: Smart valve designs with sensors and actuators enable real-time monitoring, optimizing performance and minimizing downtime.
Improved Reliability
- Sealing Technologies: Advanced seals, such as metal-to-metal and elastomers, improve leak-tightness and extend the lifespan of valves.
- Automation and Control Systems: Integrating automation and control systems ensures precise operation, reducing human error and boosting system reliability.
Environmental Sustainability
- Energy Efficiency: Valve designs focus on reducing energy consumption with features like low-friction bearings and optimized flow paths.
- Sustainable Materials: The industry is shifting to sustainable materials and processes, reducing environmental impact over a valve’s lifecycle.
Industry-Specific Innovations
- Oil and Gas Industry: Purge valves are being designed to endure high-pressure, high-temperature conditions, ensuring safety and efficiency.
- Chemical Processing: Valves for chemical processing are engineered to handle corrosive fluids, with protective coatings that prevent degradation.
To get detailed scientific explanations of Purge Valve, try Patsnap Eureka.
