
What Are Engine Bearings?
Engine bearings are critical components in internal combustion engines, facilitating the smooth rotation of the connecting rod and supporting the crankshaft’s rotation within the engine block. Their primary function is to reduce friction and wear between moving parts, thereby enhancing the engine’s efficiency and longevity. Proper selection of bearing materials is crucial to minimize energy loss due to friction and to ensure the durability of the engine components.
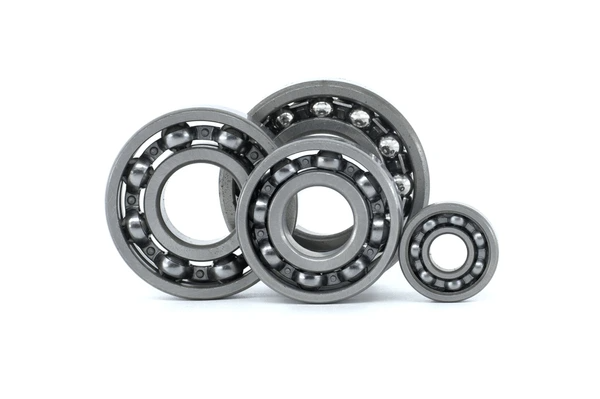
Types of Engine Bearings
- Main Bearings: Main bearings support the crankshaft’s stable rotation within the engine block, preventing both radial and axial movement. They usually consist of a sturdy steel backing, coated with low-friction, wear-resistant materials like aluminum or bronze alloys.
- Connecting Rod Bearings: Connecting rod bearings are located at the ends of the rods linking the pistons to the crankshaft. They facilitate the smooth rotation of the connecting rods on the crankshaft journals, enabling efficient power transmission from the pistons.
- Camshaft Bearings: Camshaft bearings support the camshaft, which regulates valve timing. These bearings require proper lubrication and durable material choices to withstand high loads and speeds during engine operation.
Materials Used in Engine Bearings
- Cu- or Al-based alloys: These often contain small amounts of lead (e.g., Al–Sn or Al–Pb alloys) due to lead’s excellent embeddability and conformability properties. However, due to environmental and health concerns, Pb-based alloys are being replaced by Pb-free materials.
- Pb-free materials: Modern bearings use Cu-based alloys with softer phases such as Bi, Al, and Sn to maintain performance while eliminating lead.
- Surface treatments: Techniques like resin coating and soft metal plating (e.g., bismuth alloy plating) are used to enhance fatigue resistance and seizure resistance. Additionally, onion-like carbon added to resin coatings improves tribological performance.
How Engine Bearings Work
Engine bearings reduce friction between moving parts and support the crankshaft and camshaft in internal combustion engines. They consist of two halves: the upper and lower bearing shells, which combine to form a complete bearing shell. These shells provide a contact surface for revolving parts like the crankshaft. The upper shell mounts in the engine block, and the lower shell fits in the bearing cap. Tightening the engine block and bearing cap portions creates a “bearing crush,” which helps define the cylinder diameter in a piston engine.
Common Issues with Engine Bearings
- Wear and Tear: Over time, bearings can wear out due to friction and inadequate lubrication, leading to increased clearances and potential engine damage.
- Fretting Corrosion: This occurs due to micro-movements between the bearing and its housing, leading to surface damage and reduced bearing life.
- Distortion: Improper alignment or excessive loads can cause bearing distortion, affecting the lubrication film and leading to increased wear.
- Seizure: Lack of proper lubrication can cause the bearing to seize, resulting in catastrophic engine failure.
Maintenance Tips for Engine Bearings
- Regular Lubrication: Ensure that the engine is adequately lubricated with high-quality oil to reduce friction and wear. Regularly check and change the oil to prevent contamination.
- Monitoring and Inspection: Periodically inspect the bearings for signs of wear, corrosion, or damage. Use techniques like vibration analysis to detect early signs of bearing issues.
- Surface Treatments: Apply surface treatments such as resin coating or soft metal plating to enhance the bearing’s durability and resistance to wear and seizure. Bismuth alloy plating and DLC coatings are examples of advanced surface treatments that improve fatigue and seizure resistance.
- Proper Installation: Ensure that bearings are installed correctly, with the appropriate clearance and alignment, to prevent uneven wear and potential failure.
Replacement and Repair of Engine Bearings
- Disassembly: Remove the engine components to access the bearings. This typically involves removing the crankshaft and connecting rods.
- Inspection: Inspect the bearings and related components for wear, damage, and alignment issues. Measure the bearing clearances and check for proper lubrication.
- Replacement: Replace worn or damaged bearings with new ones. Ensure the new bearings are of the correct size and material specifications.
- Reassembly: Reassemble the engine components, ensuring proper alignment and torque specifications. Apply assembly lube to the bearings to provide initial lubrication during startup.
- Testing: After reassembly, perform a thorough engine test to ensure proper operation and lubrication of the new bearings.
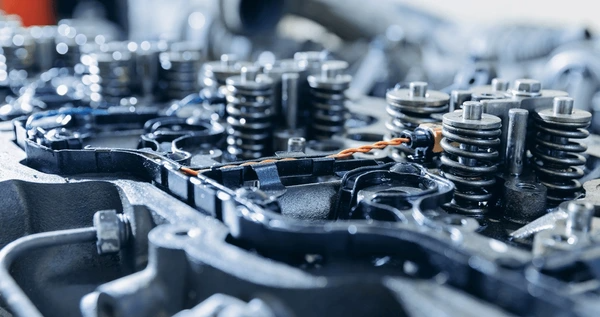
Applications of Engine Bearings
Applications in the Automotive Industry
- Journals for Supporting Driven Shafts: These bearings facilitate continuous rotational movement, ensuring smooth operation of the engine’s moving parts.
- Automotive Door Hinges and Pedals: Bearings are used in door hinges, door checks, brake, and accelerator pedals to allow repeated pivotal movement with minimal maintenance.
- Shock Absorbers and Struts: Bearings in these components handle repeated reciprocal movements, contributing to the vehicle’s suspension system’s efficiency and durability.
- Trunk Deck Lid and Hood Hinges: Lighter duty applications in the automotive industry also utilize bearings for smooth and reliable operation.
Industrial Applications
- Wind Turbines: Bearings support rotating shafts and accommodate radial and axial loads, ensuring the efficient operation of wind turbines.
- Paper Mills and Steel Making: In these industries, bearings are essential for the smooth operation of heavy machinery, reducing wear and tear and enhancing productivity.
- Pumping Stations: Bearings in pumping stations support hydraulic loads, maintain shaft alignment, and reduce vibrations, thereby extending the service life of the equipment.
- Machine Tools and Power Generators: Bearings are critical in machine tools and power generators, where they reduce friction and enhance the precision and efficiency of operations.
Aerospace Applications
- Aeroengine Bearings: These bearings are developed using advanced material technologies to withstand high temperatures and loads, ensuring the reliability and efficiency of aerospace engines.
- Space Shuttle Main Engine Turbo Machinery: Bearings in these applications are designed for high-speed and high-performance conditions, ensuring the smooth operation of critical aerospace components.
Marine and Construction Industries
- Marine Applications: Bearings in boats and ships ensure the smooth operation of propulsion systems and other rotating machinery.
- Construction Equipment: Bearings in construction machinery such as bulk conveyors, compact track loaders, and tunnel drills reduce friction and enhance the durability and reliability of the equipment.
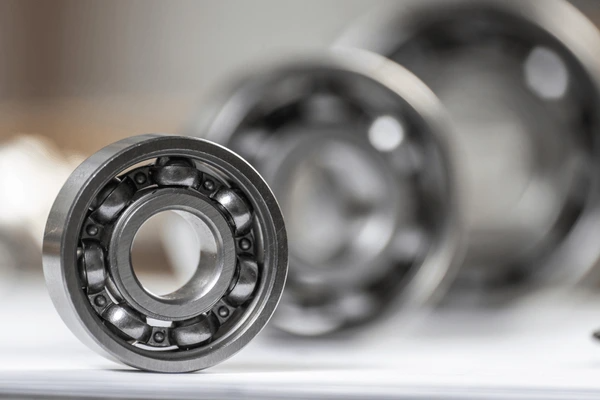
Latest Technical Innovations in Engine Bearings
Advanced Materials for Engine Bearings
- Pb-free Alloys: Traditional Pb-based alloys are being replaced with environmentally friendly alternatives such as Cu-based alloys with additions of Bi, Al, and Sn. These materials offer low friction, good corrosion resistance, and excellent embeddability and conformability.
- Bismuth Alloy Plating: Developed to improve fatigue resistance, bismuth alloy plating is a significant innovation in bearing materials. This plating enhances the durability of bearings under high load conditions.
- Composite Materials: Bearings now incorporate composite materials that combine metals with polymers or ceramics to achieve a balance of strength, wear resistance, and low friction.
Surface Treatment Technologies
Surface treatments play a crucial role in extending the lifespan and performance of engine bearings. Recent advancements include:
- Resin Coating with Additives: Resin coatings containing barium sulfate and DLC (Diamond-Like Carbon) coated journals have been developed to improve seizure resistance. Additionally, onion-like carbon added to resin coatings enhances tribological performance.
- Cold Spray Deposition: This solid-state material deposition technology is gaining traction for its ability to create wear-resistant surfaces without altering the substrate’s microstructure. It is widely adopted in automotive and aerospace industries.
- Thermal Spray Techniques: Although traditional thermal spray techniques have drawbacks such as high porosity and oxide formation, they remain popular for developing wear-resistant surfaces. Innovations aim to mitigate these issues and improve coating quality.
Design Innovations
- Integration Design: In aerospace applications, integration design ideas and practices have shown significant advantages. These designs focus on optimizing the shaft-bearing system’s reliability and performance.
- Low Maintenance Bearings: Bearings designed for low maintenance incorporate features such as metal supports with plastic layers, lubricious materials, and configurations that reduce motor vibrations and increase lifespan.
- High-Speed Applications: Bearings for high-speed applications, such as turbochargers, have been optimized to handle the increased demands of modern engines. These bearings are designed to reduce friction and wear, thereby improving efficiency and longevity.
Environmental Considerations
- Pb-free Bearings: The shift towards Pb-free bearings, such as Al alloys and overlaid Cu alloys, aims to reduce environmental and health hazards associated with lead. These materials are evaluated for their environmental impact and performance.
- Sustainable Manufacturing Processes: New manufacturing processes focus on reducing waste and energy consumption. Techniques such as cold spray deposition and advanced surface treatments contribute to more sustainable production methods.
Performance and Reliability Testing
Ensuring the reliability and performance of engine bearings is paramount. Recent innovations in testing methodologies include:
- Pre-Qualification Rig Testing: Conducted by companies like FAG Aerospace GmbH, these tests simulate real-world conditions to validate the performance and reliability of new bearing designs. This approach helps identify potential issues early in the development process.
- Advanced Simulation Tools: The use of advanced simulation tools allows for more accurate predictions of bearing behavior under various operating conditions. These tools help optimize design and material selection to achieve desired performance outcomes.
To get detailed scientific explanations of engine bearings, try Patsnap Eureka.

Learn more
2024 Toyota Hilux Review: Everything You Need to Know
The LS3 Engine: Unleashing Power and Efficiency in Automobile
V12 Engine: Unleashing Ultimate Power, Performance, and Luxury