
What is a Natural Gas Generator?
A natural gas generator is a device that converts the chemical energy of natural gas into electrical energy. This process involves several key components and operational principles, which are crucial for understanding its function and efficiency.
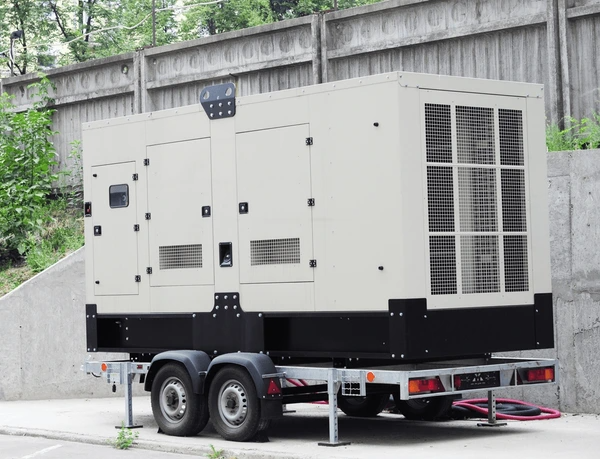
How Does a Natural Gas Generator Work?
- Natural Gas Engine: The heart of the generator, the natural gas engine, operates similarly to a gasoline or diesel engine but is specifically designed to run on natural gas. It includes components such as pistons, cylinders, and a crankshaft. The engine ignites the natural gas-air mixture to produce mechanical energy.
- Alternator: This component converts the mechanical energy produced by the engine into electrical energy. It consists of a rotor and a stator, where the rotor generates a rotating magnetic field that induces an electric current in the stator windings.
- Fuel System: The fuel system includes a fuel tank, fuel lines, and a fuel regulator. It ensures a steady supply of natural gas to the engine at the correct pressure and flow rate.
- Cooling System: To prevent overheating, the generator is equipped with a cooling system that circulates coolant through the engine and other components.
- Exhaust System: This system expels the combustion gases produced by the engine. It includes components like exhaust pipes, mufflers, and catalytic converters to reduce emissions.
- Control Panel: The control panel allows users to monitor and control the generator’s operation. It includes gauges, switches, and indicators for parameters such as voltage, current, and frequency.
Benefits of Natural Gas Generators
Environmental Benefits: Natural gas generators produce fewer pollutants compared to other fossil fuel generators, such as those running on coal or oil. This results in lower emissions of CO2, NOx, and SOx, contributing to a cleaner environment and helping to meet stringent environmental regulations.
Efficiency: Natural gas generators are known for their high fuel efficiency. They can achieve efficiency rates of up to 60% in combined cycle power plants, which is significantly higher than the efficiency rates of coal-fired power plants. This high efficiency translates to lower fuel costs and better overall performance.
Economic Performance: The cost of natural gas is generally lower and more stable compared to other fossil fuels. This economic advantage is further enhanced by the high efficiency of natural gas generators, making them a cost-effective solution for power generation.
Versatility and Reliability: Natural gas generators can be used in various applications, including residential, commercial, and industrial settings. They are also reliable during power outages, as natural gas supply lines are often unaffected by weather conditions that might disrupt electrical grids.
Reduced Noise Levels: Compared to gasoline generators, natural gas generators tend to produce less noise, making them more suitable for residential and commercial use where noise pollution is a concern.
Common Issues with Natural Gas Generators
- Fuel Supply and Price Volatility: Although natural gas is generally cheaper than other fossil fuels, its price can be volatile due to market fluctuations and geopolitical factors. This can affect the overall cost of operating natural gas generators.
- Maintenance and Operational Challenges: Natural gas generators require regular maintenance to ensure optimal performance. Common maintenance issues include the need for frequent inspections of gas lines and connections to prevent leaks, as well as regular cleaning of components to avoid buildup of contaminants.
- Initial Setup Costs: The initial cost of setting up a natural gas generator can be higher compared to other types of generators. This includes the cost of installing gas lines and ensuring proper ventilation systems to handle exhaust gases safely.
- Safety Concerns: Natural gas is a flammable substance, and improper handling or installation of natural gas generators can lead to safety hazards such as gas leaks and explosions. It is crucial to have proper safety measures in place, including gas detectors and emergency shut-off systems.
- Environmental Impact of Methane: While natural gas generators produce fewer CO2 emissions, methane, the primary component of natural gas, is a potent greenhouse gas. Any leaks or incomplete combustion can contribute significantly to greenhouse gas emissions, which is a concern for long-term environmental sustainability.
Maintenance Tips for Natural Gas Generators
- Regular Inspection and Servicing: Conduct regular inspections and servicing of the generator to identify and address any wear and tear issues. This includes checking and replacing filters, pressure regulating valves, and absorbers as needed to maintain optimal performance.
- Fuel Quality Management: Ensure the natural gas used is of high quality and free from contaminants such as water, light oil, and particles. Using a natural gas purification unit can help in maintaining fuel quality and ensuring a stable supply.
- System Calibration and Testing: Regularly calibrate and test the generator’s systems, including the ignition system, compression ratio, and spark advance settings. This helps in maintaining the efficiency and reliability of the generator.
- Noise and Emission Control: Implement measures to control noise and emissions, such as using soundproof enclosures and advanced emission control technologies. Regularly monitor and adjust these systems to ensure compliance with environmental regulations.
- Safety Protocols: Follow strict safety protocols to prevent accidents and ensure safe operation. This includes installing fire-restrain devices, pressure reducers, and other safety features, as well as training personnel on proper handling and emergency procedures.
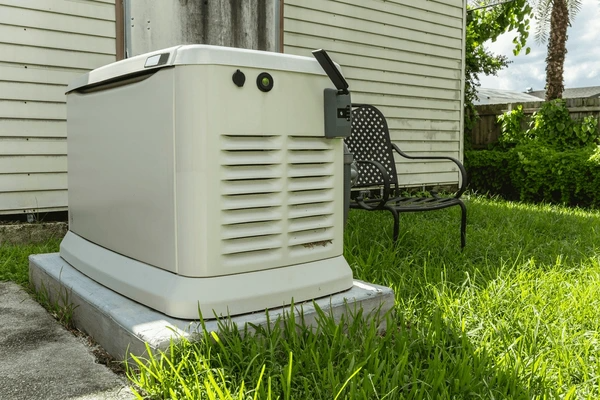
Applications of Natural Gas Generator
Industrial Applications
- Power Generation: Natural gas generators are extensively used in power plants for electricity generation. They offer a cleaner alternative to coal and oil-fired power plants, reducing greenhouse gas emissions and improving air quality.
- Manufacturing: In manufacturing industries, natural gas generators provide a reliable power source for continuous operations. They are particularly beneficial in sectors like chemical production, where consistent energy supply is critical.
- Oil and Gas Industry: Natural gas generators are used in oil and gas fields to power drilling rigs, production facilities, and processing plants. They help in utilizing associated gas, which is a byproduct of oil extraction, thereby reducing flaring and environmental impact.
Commercial Applications
- Backup Power: Commercial establishments such as hospitals, data centers, and shopping malls use natural gas generators as backup power sources. They ensure uninterrupted power supply during grid outages, maintaining critical operations and services.
- Combined Heat and Power (CHP) Systems: Natural gas generators are integral to CHP systems, which simultaneously produce electricity and useful heat. This application is common in commercial buildings, universities, and industrial facilities, enhancing energy efficiency and reducing operational costs.
Residential Applications
- Home Backup Generators: Natural gas generators are increasingly popular for residential use, providing backup power during outages. They are preferred over diesel generators due to their cleaner emissions and the convenience of a continuous fuel supply from the natural gas grid.
Environmental and Efficiency Benefits
- Lower Emissions: Natural gas generators produce fewer pollutants compared to coal and oil-based generators. They emit lower levels of sulfur dioxide (SO2), nitrogen oxides (NOx), and particulate matter, contributing to improved air quality and public health.
- High Efficiency: Modern natural gas generators are highly efficient, with some combined cycle plants achieving efficiencies of up to 60%. This high efficiency translates to lower fuel consumption and reduced operational costs.
Innovative Applications
- Liquefied Natural Gas (LNG) Production: Natural gas generators are used in LNG plants to power the liquefaction process. The process involves cooling natural gas to -162°C, converting it into a liquid form for easier storage and transportation.
- Gas Treatment Facilities: In gas treatment facilities, natural gas generators are employed to power purification units that remove impurities such as water, light oil, and particles from the gas. This ensures a stable and clean supply of natural gas for various applications.
- Storage and Transport: Advanced systems utilize natural gas generators to facilitate the absorption and segregation of natural gas into liquid solvents for efficient storage and transport. This method enhances the compressed volume ratio, making storage and transportation more economical.
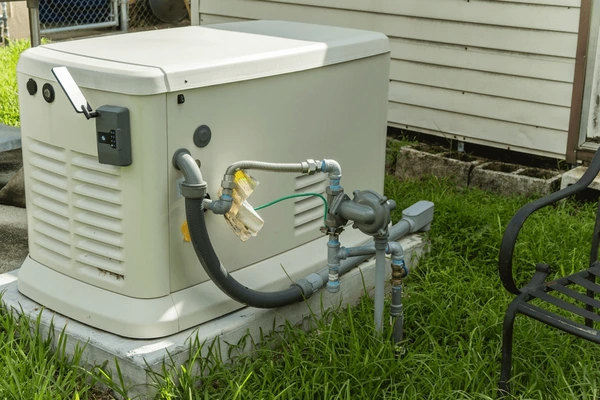
Latest Technical Innovations in Natural Gas Generator
Core Technology Advancements
Recent innovations in the core technology of natural gas generators have primarily focused on enhancing the gas treatment facilities. One significant development is the integration of advanced natural gas purification units. These units are designed to remove impurities such as water, light oil, and particles from the natural gas, which is crucial for maintaining a stable supply and improving the overall efficiency of the generator. The purification process involves a series of steps including filtration, adsorption, and separation techniques, which are detailed in recent research papers
Efficiency and Performance Improvements
Efficiency and performance improvements in natural gas generators have been a major area of focus. Innovations include the development of high-efficiency combustion systems that optimize the air-fuel mixture, resulting in more complete combustion and reduced emissions. Additionally, advancements in control systems have enabled more precise regulation of the generator’s operating parameters, leading to better fuel efficiency and lower operational costs. These improvements are often quantified by metrics such as thermal efficiency (measured in percentage) and specific fuel consumption (measured in g/kWh).
New Materials and Components
The use of new materials and components in the construction of natural gas generators has also seen significant advancements. For instance, the adoption of high-temperature resistant alloys and ceramics in the turbine and combustion chamber components has allowed for higher operating temperatures, which in turn improves the overall efficiency of the generator. Moreover, the development of advanced coatings and surface treatments has enhanced the durability and longevity of critical components, reducing maintenance requirements and downtime.
To get detailed scientific explanations of natural gas generators, try Patsnap Eureka.

Learn more
Shock Cords: Versatile Strength for Every Need
Pressure Switches: Small Devices, Big Impact
Unveiling The Lead Screw: Its Mechanism, Benefits, And Beyond