
Technical Background and Objectives
Background
Improving brazing performance has garnered significant attention from researchers and industry players. Patent application data shows a relatively stable trend with an initial increase followed by a gradual decline, suggesting consistent R&D efforts. Conversely, related literature publications have steadily increased, indicating growing academic interest. This divergence suggests that while the industry may have reached a certain level of maturity, academia continues to explore new avenues, potentially leading to future advancements.
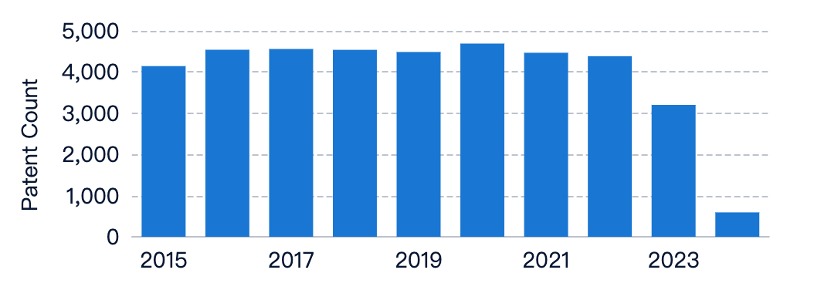
Objectives
The primary objective is improving brazing performance through innovative techniques, materials, and methodologies. This research aims to address challenges and improve the quality, efficiency, and cost-effectiveness of brazing operations, ultimately advancing manufacturing processes and product quality.
To get a detailed scientific explanations of improving brazing performance, try Eureka.
Technical Current Status Analysis
Brazing Overview
Brazing is widely used in automotive, aerospace, electronics, and construction industries. It involves using a filler metal with a lower melting point than the base metals to create strong, durable joints.
Applications and Impact:
- Automotive: Joining components like heat exchangers, radiators, and fuel systems for improved durability and heat transfer.
- Aerospace: Joining structural components, engine parts, and heat exchangers to ensure safety, reliability, and fuel efficiency.
- Electronics: Joining components in power electronics, semiconductor packaging, and heat sinks for better thermal management and reliability.
- Construction: Joining pipes, fittings, and components in HVAC systems and plumbing for stronger, more durable joints.
Technical Characteristics and Challenges:
- Filler Metal Properties: Developing filler metals with improved wettability, capillary action, and mechanical properties.
- Base Metal Compatibility: Optimizing compatibility to ensure strong, reliable joints.
- Joint Design and Clearance: Ensuring proper joint design and clearance for adequate filler metal flow.
- Surface Preparation and Cleanliness: Developing effective surface preparation techniques.
- Brazing Atmosphere and Flux: Optimizing atmosphere and flux composition to improve joint quality.
- Process Control and Repeatability: Ensuring consistent, high-quality brazed joints through advanced process control.
Technological Paths:
- Advanced Filler Metal Development: Researching new compositions with improved properties.
- Surface Engineering and Pretreatment: Developing advanced techniques for better joint formation.
- Joint Design Optimization: Using modeling and simulation to optimize designs.
- Brazing Process Control and Automation: Implementing advanced control systems.
- Atmosphere and Flux Development: Researching optimized atmospheres and fluxes.
- Characterization and Quality Control: Developing advanced techniques for evaluating joint quality.
- Multidisciplinary Research and Collaboration: Fostering collaboration between various fields.
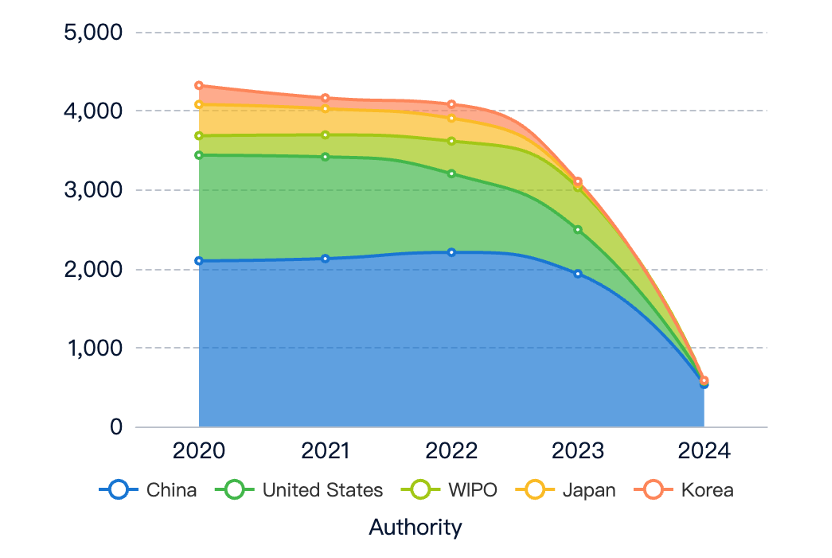
Research Content
Research Objectives
Enhance brazing performance through innovative techniques, materials, and methodologies to meet the increasing demands for higher quality, efficiency, and cost-effectiveness.
Research Direction and Focus
Optimization of Brazing Materials and Filler Metals
- Investigate advanced filler metal compositions tailored to specific applications.
- Enhance compatibility and wettability with various base metals to improve joint strength, corrosion resistance, and overall performance.
Innovative Brazing Techniques and Process Optimization
- Explore novel techniques like induction brazing and laser brazing for improved control, precision, and efficiency.
- Optimize process parameters to achieve superior joint quality and minimize defects using process modeling and simulation.
Advanced Characterization and Quality Control
- Implement non-destructive testing methods like ultrasonic inspection and X-ray tomography for in-situ monitoring.
- Conduct microstructural analysis and mechanical testing to understand the relationship between brazing parameters, joint microstructure, and mechanical properties.
Technical Development Roadmap
Key Areas of Advancement
- Controlled Atmosphere Brazing (CAB) Technologies: Development of high-purity atmosphere control systems, optimization of brazing alloy compositions, and advancements in furnace designs.
- Active Brazing Technologies: Plasma-assisted brazing, ultrasonic-assisted brazing, and induction brazing for localized heating and joining.
- Advanced Brazing Filler Metal Development: High-temperature filler metals, optimized compositions for specific applications, and nanoparticle-reinforced filler metals.
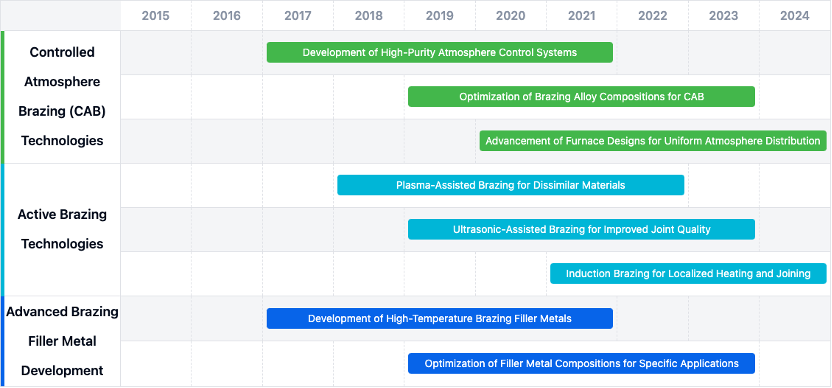
Main Player Analysis
Key Players and Focus
- Mitsubishi Electric Corp.: 1973 patents focused on advanced brazing materials, processes, and applications.
- DENSO Corp.: 2712 patents focused on advanced brazing solutions for automotive applications.
- GE Aerospace: 1980 patents focused on brazing solutions for aerospace applications.
- Harbin Institute of Technology: Research on brazing of dissimilar materials, composite materials, and corrosion behavior.
- Nanjing University of Aeronautics & Astronautics: Research on brazing of advanced materials, interfacial microstructure, and process optimization.
Current Technical Solution Overview
Brazing Alloy Compositions
- Improved Wetting and Flow: Formulated to enhance wetting and flow characteristics.
- High-Temperature Applications: Designed to maintain properties at elevated temperatures.
- Dissimilar Materials: Specialized compositions for compatibility and joint reliability.
- Low-Temperature Applications: Compositions with lower melting points.
- Corrosion Resistance: Enhanced resistance through specific elements.
Brazing Process Modifications
- Temperature Profiles and Atmosphere Control: Adjustments to improve performance.
- Surface Treatment Methods: Enhancing wettability and joint quality.
- Process Optimization: Controlling parameters for better joint properties.
Brazing Joint Design and Preparation
- Surface Treatments and Joint Clearances: Optimizing for better brazing performance.
- Joint Design and Geometry: Enhancing filler metal flow and joint strength.
Brazing Materials and Substrates
- Compatible Materials: Selecting materials with suitable properties.
- Specialized Brazing Methods: Tailored techniques for specific applications.
Brazing Evaluation and Quality Control
- Non-Destructive Testing: Ensuring joint integrity and quality.
- Process Monitoring: Continuous data analysis for performance improvement.
Key Patent Interpretation
Patent Highlights
Patent 1: Development-Free Element Type Ni-Based Brazing Filler Metal
- Core Invention Points:
- No-MPD type Ni-based filler metal with better wettability, higher remelting temperature, and better plasticity.
- Solves issues like poor wettability and low remelting temperature found in traditional filler metals.

Patent 2: Rolling Process of Composite Brazing Aluminum Foil
- Core Invention Points:
- Controlled annealing and cold rolling processes for better performance.
- Improved brazing performance through controlled grain size and structure.
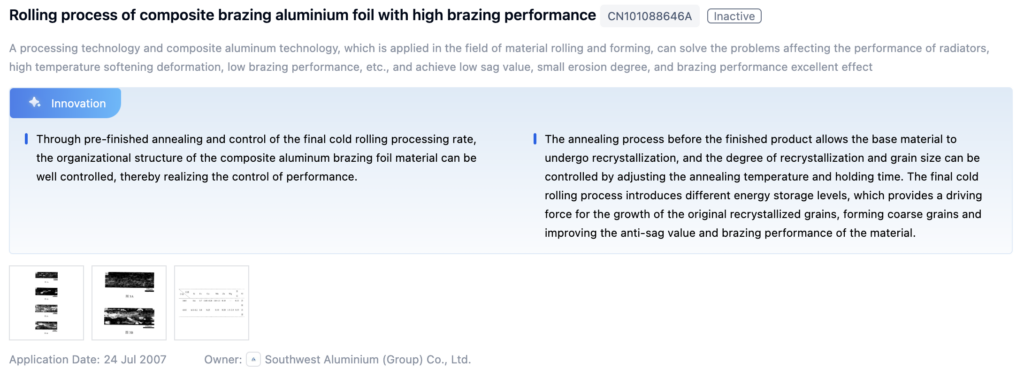
Patent 3: Multi-Field Assisted Brazing Device and Method
- Core Invention Points:
- Combines ultrasonic vibration, electric field, and magnetic field to improve wettability and joint quality.
- Low power loss, good temperature uniformity, and excellent insulation performance.
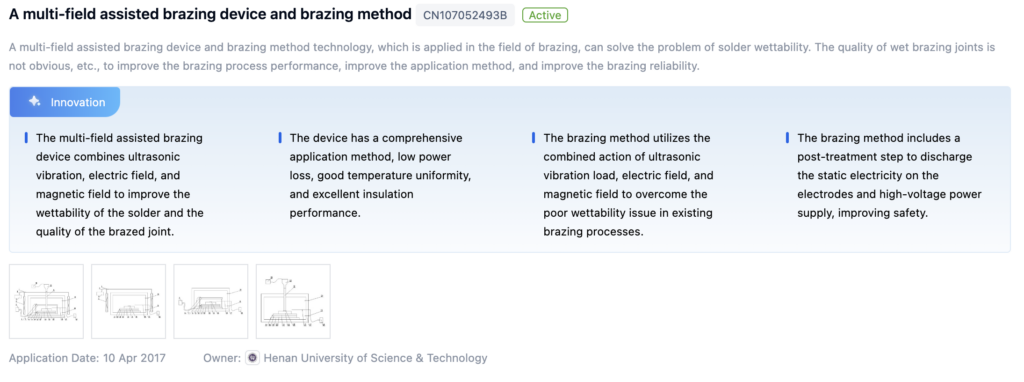
Possible Research Directions
- Brazing Method Optimization: Fine-tuning process parameters for stronger, defect-free joints.
- Enhanced Alloy Compositions: Developing specialized alloys for better performance.
- Fluxless Brazing Techniques: Simplifying the process by eliminating flux.
- Filler Metal Application and Control: Ensuring proper distribution and flow of filler metal.
- Automated Brazing Processes: Implementing robotic systems and advanced monitoring for improved consistency and quality.
If you want an in-depth research or a technical report, you can always get what you want in Eureka Technical Research. Try now!
