
What is an Immersion Heater
An immersion heater, often referred to as a direct immersion heater, is a highly efficient device used to heat liquids or gases. It operates by directly submerging an electric heating element into the fluid, allowing for rapid and uniform heat transfer. These heaters typically feature a tubular housing with electric resistance elements made from durable materials like Nichrome or ceramic-coated metals. Insulated from the housing, the heating element efficiently warms the surrounding fluid when powered by electricity. In this article, we’ll explore how immersion heaters work, their applications, and why they are a reliable solution for various heating needs.
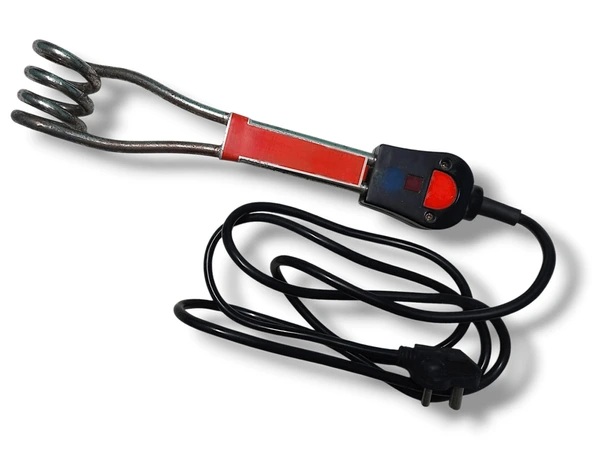
Components of Immersion Heaters
- Heating Element: The heating element is the core component responsible for generating heat. It is typically made from resistive materials such as coiled wire, ceramic-coated rods, or similar materials. This element directly transfers heat to the surrounding fluid, ensuring quick and efficient warming.
- Housing or Sheath: The housing, also known as the sheath, is a protective casing that encloses the heating element. It is crafted from corrosion-resistant materials like stainless steel or ceramic to withstand harsh environments and prevent damage to the element.
- Flange or Mounting: A flange or mounting bracket secures the heater to a tank or vessel. This component ensures the heater remains stable during operation, allowing for safe and effective heat transfer.
- Electrical Connections: Electrical connections, such as terminals or wires, connect the heating element to a power source. These connections ensure a consistent and reliable flow of electricity to power the heater.
- Thermostat or Controller (Optional): Many immersion heaters include a thermostat or controller for precise temperature regulation. This optional feature enhances safety by preventing overheating and allows users to maintain the desired temperature for their application.
Benefits of Using an Immersion Heater
1. Direct and Efficient Heat Transfer
Immersion heaters transfer heat directly to the material or fluid by submerging within it. Since they eliminate the need for intermediate surfaces, they achieve faster and more uniform heating. As a result, they provide higher thermal efficiency compared to external heating systems, which makes them a practical solution for energy-intensive applications.
2. Compact and Space-Saving Design
Thanks to their compact size, immersion heaters fit easily into applications where space is limited. Their design simplifies integration into existing tanks or vessels without requiring extensive modifications. This makes them an ideal solution for environments where external heating systems would be impractical or too bulky.
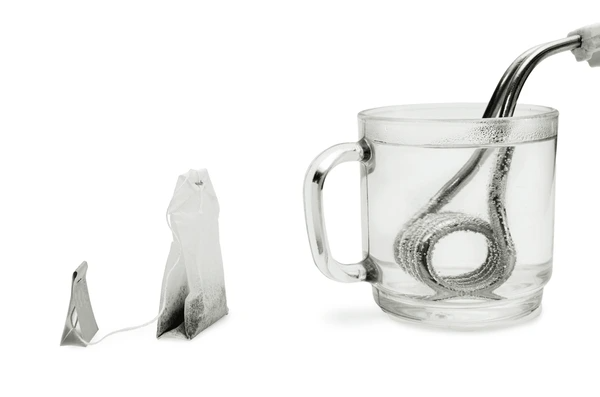
3. Precise Temperature Control
Immersion heaters allow you to control temperatures with precision by directly adjusting the heat input. This feature becomes particularly useful in applications that demand strict temperature ranges. Moreover, integrating advanced control systems ensures automated regulation and prevents overheating, enhancing both efficiency and safety.
4. Improved Energy Efficiency
By heating the material directly, immersion heaters reduce heat losses to the surrounding environment. This direct approach increases energy efficiency and can significantly lower operational costs. In industrial settings, where energy demands are high, this efficiency can make a noticeable difference in cost savings.
5. Versatility and Scalability
Immersion heaters adapt easily to a wide range of applications, including heating liquids, gases, and even solid materials. They come in various sizes and power ratings, allowing you to scale them to match specific requirements. From small laboratory setups to large industrial operations, immersion heaters provide the flexibility needed for diverse applications.
6. Enhanced Safety and Durability
Built with durable and corrosion-resistant materials, immersion heaters perform well even in harsh environments. Manufacturers design these heaters with safety features such as overheating protection and automatic shutoff mechanisms. These additions not only enhance safety but also improve long-term reliability in demanding industrial processes.
Applications of Immersion Heaters
1. Maintaining Molten Metal Baths
Industries use immersion heaters with high heat flux to maintain molten states for metals like aluminum, tin, zinc, and magnesium. These heaters ensure consistent temperatures for casting processes, improving the quality of the final product. By providing direct heat transfer, they minimize energy loss and enhance process efficiency.
2. Heating Process Solutions
In the finishing industry, immersion heaters are an economical choice for heating various process solutions. Factors such as solution temperature, heater surface temperature, and specific heat capacity are carefully considered during design. This precise control ensures optimal performance and extends the longevity of both the heater and the process solution.
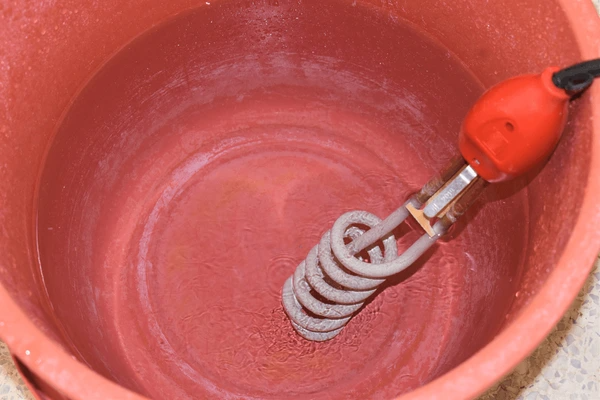
3. Catalyst Bed Heating
Chemical reactors often require efficient heating within catalyst beds to maintain reaction conditions. Immersion heaters can be directly submerged into the catalyst bed, providing even and effective heat transfer. To avoid damaging brittle catalyst particles, operators must carefully control the heat output, minimizing thermal stress and ensuring consistent performance.
Tips for Maintaining an Immersion Heater
1. Descaling and Cleaning
Mineral buildup and scale can accumulate on the heating element, reducing efficiency and causing potential damage. To prevent this, perform regular descaling.
- Descaling Solution: Use a descaling solution or vinegar to dissolve mineral deposits.
- Soaking: Soak the heating element in the solution for several hours.
- Scrubbing: After soaking, scrub off the loosened scale.
- Heavy Buildup: If descaling doesn’t work, consider replacing the heating element for severe buildup.
2. Gasket and Seal Replacement
Check the gaskets and seals regularly for signs of wear, cracks, or leaks. Faulty seals can cause water leakage, which may create fire hazards.
- Inspection: Replace gaskets or seals as needed to prevent leakage and ensure safety.
3. Inspecting Electrical Connections
Inspect all electrical connections, wiring, and terminals for corrosion, damage, or loose connections.
- Tightening Connections: Tighten any loose connections to avoid potential short circuits.
- Replace Damaged Wiring: Replace any corroded or damaged wiring to maintain safe operation.
4. Testing the Thermostat
Test the thermostat periodically to ensure proper functioning. It should turn the heater on and off at the right temperatures.
- Replacement: If the thermostat malfunctions, replace it to ensure reliable performance.
5. Monitoring Water Levels
Never operate the heater unless fully submerged in water.
- Low Water Cutoff: Install a low water level cutoff switch or monitor the water level to prevent overheating.
- Avoid Exposure: Make sure the heating element remains submerged to avoid damage from exposure.
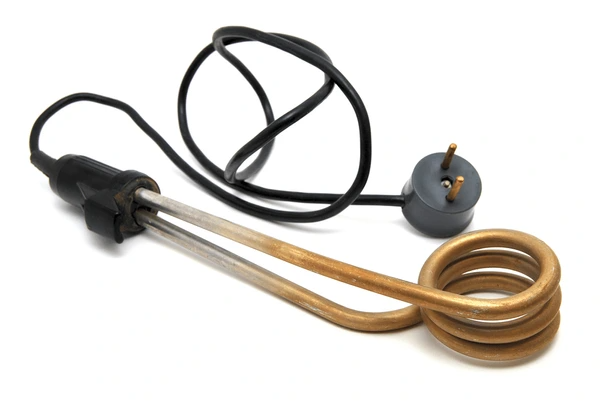
6. Professional Inspection
Consider having a professional inspect and service the heater annually, or as recommended by the manufacturer.
- Inspection Benefits: A professional can identify potential issues and perform necessary repairs or replacements, ensuring safe and efficient operation.
Common Issues
Overheating
Insufficient liquid levels or inadequate flow can cause heating elements to overheat. Overheating not only reduces efficiency but also leads to premature failure of the components.
Scaling and Fouling
Mineral deposits and contaminants often accumulate on the heater’s surface. These buildups reduce efficiency, create hotspots, and may damage the system over time.
Electrical Faults
Ground faults, arcing, and insulation breakdowns can occur due to moisture ingress or material wear. These issues pose significant safety risks if left unaddressed.
Troubleshooting and Prevention Tips
Overheat Protection
Install temperature sensors, high-limit switches, and low liquid level cut-offs to prevent overheating. These safeguards ensure the system shuts down before damage occurs.
Descaling and Maintenance
Perform regular cleaning and descaling to keep the heater surface free from mineral deposits. Consistent maintenance prevents fouling and helps maintain optimal performance.
Electrical Safety Measures
Inspect electrical connections, ensure proper grounding, and seal components against moisture. These steps help prevent electrical faults and ensure safe operation.
Correct Immersion Depth
Make sure the heating elements remain fully submerged during operation. Proper immersion prevents exposure, which could lead to overheating and component failure.
Optimize Liquid Flow
Ensure adequate liquid flow around the heating elements. This promotes even heat distribution and prevents the formation of hotspots, which can harm the system.
To get detailed scientific explanations of immersion heaters, try Patsnap Eureka.
