
Introduction
Plastic is one of the most versatile materials in modern life, found in everything from packaging to automotive parts. But how is it made? The process starts with raw materials like crude oil or natural gas, which are refined into chemical compounds. Through polymerization, these compounds are transformed into long chains of polymers, forming the basis of plastic. The polymers are then molded or shaped into a variety of products using methods like injection molding, extrusion, or blow molding. Let’s explore the fascinating journey of how plastic is created, its types, and its uses.
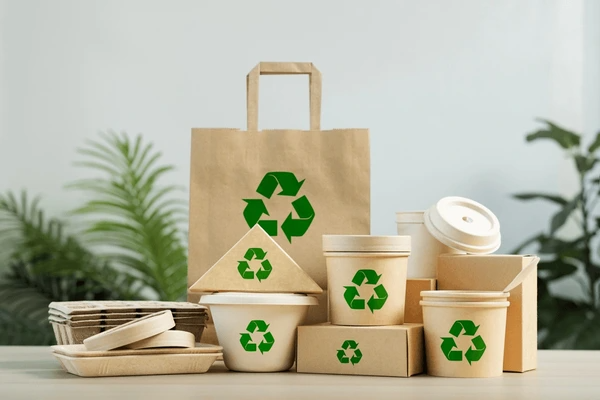
Raw Materials for Plastic
The selection of raw materials is crucial in plastic shaping processes as it directly impacts the efficiency, quality, and environmental footprint of the final product. Common raw materials include thermoplastics such as polyethylene (PE), polypropylene (PP), polystyrene (PS), and polyvinyl chloride (PVC), as well as thermosetting plastics like epoxy resins and phenolic resins. Each material has unique properties that influence the shaping process.
The Plastic-Making Process
Injection Molding
Injection molding is a predominant method for mass-producing plastic parts with complex geometries and precise dimensions. The process involves injecting molten plastic into a mold cavity, where it cools and solidifies into the desired shape. This method is widely used due to its efficiency and ability to produce high-quality parts with minimal waste.
Blow Molding
Blow molding is used to create hollow plastic products such as bottles and containers. The process involves heating a plastic preform and inflating it within a mold to form the final shape. This method is particularly effective for producing lightweight and durable items.
Extrusion
Extrusion is a continuous process where molten plastic is forced through a die to create long shapes with a consistent cross-section, such as pipes, sheets, and films. This method is highly efficient for producing large volumes of uniform products.
3D Printing (Additive Manufacturing)
3D printing, particularly Powder Bed Fusion (PBF) techniques like Selective Laser Sintering (SLS) and Multi Jet Fusion (MJF), has revolutionized plastic manufacturing. These methods build parts layer-by-layer from thermoplastic powders, allowing for complex geometries and customization. PBF is advantageous for producing parts without support structures and is suitable for low to medium volume production.
Types of Plastic
Shaping and Manufacturing Plastic Products
- Injection Molding: This process involves melting plastic and injecting it into a mold where it cools and solidifies into the desired shape. It is widely used for mass production of complex and precise plastic parts.
- Blow Molding: Used primarily for making hollow plastic products like bottles and containers, this method involves inflating a heated plastic tube until it fills a mold and forms the desired shape.
- Extrusion: In this process, melted plastic is forced through a die to create long shapes like pipes and sheets. The extruded plastic is then cooled and cut to the required length.
- Thermoforming: This involves heating a plastic sheet until it becomes pliable, then forming it over a mold and trimming it to create the final product.
- 3D Printing: Also known as additive manufacturing, this method builds plastic parts layer by layer based on digital models, allowing for high customization and complex geometries.
Advantages and Disadvantages of Plastic
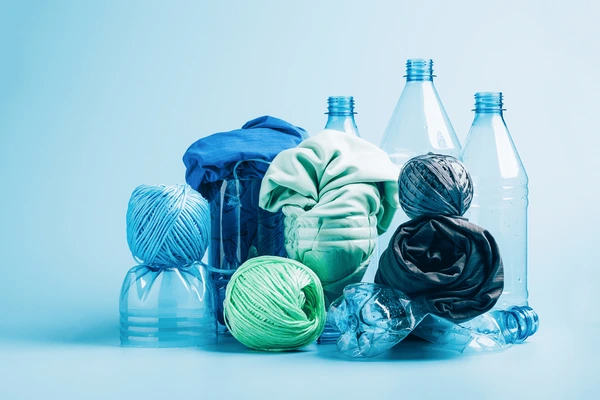
Advantages of the Plastic-Making Process
Versatility and Adaptability
Plastics can be molded into a wide variety of shapes and sizes, making them suitable for diverse applications ranging from disposable packaging to high-end engineering components. This adaptability is due to the material’s inherent properties and the flexibility of manufacturing processes such as injection molding and extrusion.
Lightweight
Plastics are significantly lighter than metals and other traditional materials, which is advantageous in industries like automotive and aerospace where weight reduction is crucial for fuel efficiency and performance.
Cost-Effectiveness
The raw materials for plastics are relatively inexpensive, and the manufacturing processes are highly efficient, allowing for mass production at a lower cost compared to other materials. This makes plastics an economically viable option for many applications.
Energy Efficiency in Production
The energy required for plastic molding processes, such as injection molding and extrusion, is relatively low compared to metalworking processes. This contributes to lower overall production costs and energy consumption.
Chemical Resistance
Plastics exhibit excellent resistance to a wide range of chemicals, making them ideal for use in harsh environments and for storing reactive substances.
Recyclability
Many types of plastics, particularly thermoplastics, can be recycled and reprocessed multiple times without significant degradation in quality. This supports sustainable manufacturing practices and reduces environmental impact.
Innovative Manufacturing Techniques
Advanced manufacturing techniques such as additive manufacturing (AM) and powder bed fusion (PBF) allow for high precision and complex geometries, which are difficult to achieve with traditional methods. These techniques also enable mass customization and rapid prototyping.
Disadvantages of the Plastic-Making Process
Environmental Impact
The production and disposal of plastics pose significant environmental challenges. The manufacturing process consumes large amounts of water and energy, and generates harmful emissions such as carbon monoxide, carbon dioxide, and volatile organic compounds (VOCs). Additionally, plastic waste contributes to pollution in landfills and oceans.
Resource Consumption
The plastic-making process requires substantial amounts of non-renewable resources, such as petroleum and natural gas, which raises concerns about sustainability and resource depletion.
Recycling Challenges
While many plastics are recyclable, the recycling process can be complex and inefficient. Contaminants and mixed materials often reduce the quality and economic viability of recycled plastics, limiting their use to lower-end applications.
Mechanical Limitations
Plastics generally have lower mechanical strength and thermal stability compared to metals. This limits their use in high-stress and high-temperature applications unless reinforced with additives or composites.
Dimensional Stability
Plastics are prone to shrinkage and deformation during cooling, which can affect the precision and quality of the final product. This issue is particularly significant in injection molding processes.
Health and Safety Concerns
The production and processing of plastics involve the use of potentially hazardous chemicals and solvents, which can pose health risks to workers and contribute to environmental pollution if not managed properly.
Anisotropic Properties
Additive manufacturing processes like PBF produce parts with anisotropic mechanical properties, meaning the strength and durability can vary depending on the build orientation and layer thickness. This can be a limitation for certain applications.
High Initial Costs
The setup and maintenance of plastic manufacturing facilities, including the cost of molds, machinery, and quality control systems, can be substantial. This initial investment can be a barrier for small-scale manufacturers.
Limited High-Temperature Performance
Most plastics have a lower melting point compared to metals, which restricts their use in high-temperature environments. Specialized high-performance plastics can address this issue but at a higher cost.
Applications of Plastic Product
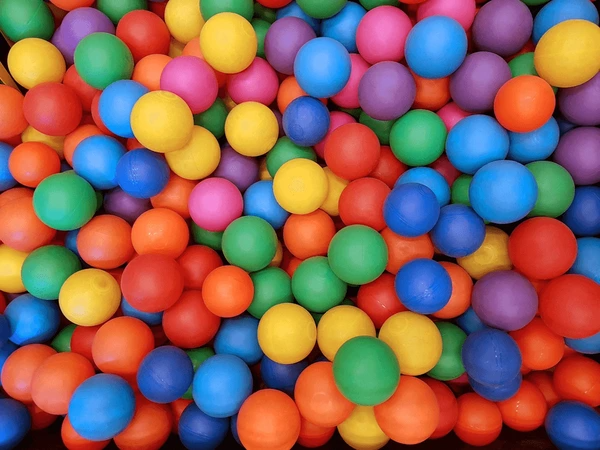
Automotive Industry
Plastic products are extensively used in the automotive industry for both interior and exterior parts. They are utilized in the manufacturing of car bodies, dashboards, bumpers, and other components due to their lightweight and durable nature. The development of specialized plastics such as engineering plastics (EP) and general-purpose plastics has further enhanced their application in this sector. Additionally, plastics like polypropylene, polyurethane, and polyvinyl chloride are commonly used in automotive parts due to their excellent mechanical properties and ease of fabrication.
Construction Industry
In the construction industry, plastic products are used in various applications such as cast-in-place concrete. Plastic cushion blocks, for instance, are widely used in engineering projects to provide support and stability. The construction ministry has promoted the use of plastic products as key materials in their development plans. Plastics are also used in building and construction products like pipes, tubes, sheets, and insulation materials due to their durability and resistance to environmental factors.
Packaging Industry
The packaging industry heavily relies on plastic products for various applications. Polyesters, for example, are used to manufacture mono- and bi-oriented films, shrink films, and thermoformed foodstuff packaging. These materials are chosen for their excellent barrier properties, flexibility, and ability to be formed into different shapes and sizes. Bioplastics like polylactic acid (PLA) are gaining popularity in packaging due to their biodegradable nature, making them an eco-friendly alternative to traditional petro-plastics.
Electronics and Electrical Industry
Plastic materials are widely used in the electronics and electrical industry for manufacturing components such as housings, connectors, and insulation materials. Their excellent electrical properties, lightweight, and ease of molding make them ideal for these applications. Organic-inorganic composite materials, for instance, are used as resin additives and coating materials to enhance the performance and durability of electronic components.
Medical and Biomedical Applications
In the medical field, plastics are used in the production of various medical devices and equipment. PLA, due to its biocompatibility and biodegradability, is used in tissue engineering and biomedicine. It is also widely utilized in 3D printing for creating custom medical implants and prosthetics. The antimicrobial properties of certain plastics, such as those derived from algae, make them suitable for use in medical applications where hygiene is critical.
Public Space and Product Design
Plastic materials are increasingly used in the design of public space products. These applications include furniture, fixtures, and other elements that enhance the aesthetic and functional aspects of public spaces. The flexibility and durability of plastics allow for innovative designs that can withstand various environmental conditions.
Agricultural Sector
In agriculture, plastics are used for applications such as mulching films, greenhouse covers, and irrigation systems. These materials help in improving crop yield and protecting plants from adverse weather conditions. Polyesters, for example, are used to manufacture films for mulching and wrapping bales, providing a cost-effective and efficient solution for farmers.
Application Cases
Product/Project | Technical Outcomes | Application Scenarios |
---|---|---|
Algae-derived antimicrobial plastic substrates Bloom Holdings LLC | Contains antimicrobial substances from algae, providing inherent antimicrobial properties similar to nylon and other polymers. | Used in environments requiring antimicrobial properties, such as medical devices and food packaging. |
Aliphatic-aromatic biodegradable polyester Novamont SpA | Biodegradable polyesters from renewable sources, offering environmental benefits and compatibility with other biodegradable polymers. | Ideal for applications requiring biodegradable materials, such as packaging and agricultural films. |
Organic-inorganic composite material Orient Chemical Industries Ltd. | High mechanical strength and water resistance, low-cost preparation, and high functionality. | Suitable for high-performance applications such as construction materials and high-functional plastic products. |
Plastic materials in product design | Extensive application in product design due to versatility and adaptability. | Used in various product designs to enhance functionality and aesthetics. |
Algae-derived antimicrobial plastic substrates Bloom Holdings LLC | Contains antimicrobial substances from algae, providing inherent antimicrobial properties similar to nylon and other polymers. | Used in environments requiring antimicrobial properties, such as medical devices and food packaging. |
Latest Technical Innovations in Plastic Product
Material Innovations
- Organic-Inorganic Composite Materials: Recent innovations include the development of organic-inorganic composite materials that enhance the mechanical and electrical properties of plastics. These composites are designed to replace conventional materials like metal, glass, and wood due to their superior molding ability, light weight, flexibility, and excellent mechanical properties.
- Siloxane-Based Coating Compositions: Innovations in siloxane-based coatings have led to significant improvements in the properties of plastic surfaces. These coatings provide excellent dyeability, abrasion resistance, glossiness, and transparency, making them suitable for applications requiring high surface quality, such as optical lenses and safety goggles.
Manufacturing Process Innovations
- Extrusion Techniques: The extrusion process has seen advancements that allow for the continuous production of films, sheets, and profiles with high surface quality. This method is particularly advantageous for producing versatile plastic products with single-sided self-adhesive properties and abrasion-resistant protective layers.
- Coating Processes: New coating processes have been developed to enhance the surface properties of plastic products. For instance, applying organic or silicon coatings to plastic surfaces can significantly improve scratch resistance, making these products more durable and suitable for various industrial applications.
Property Enhancement Techniques
- Abrasion Resistance: To address the inherent softness of plastic surfaces, new coating compositions have been developed. These include siloxane-based coatings that offer excellent abrasion resistance and are used in products like optical lenses and safety goggles. However, challenges remain in balancing properties such as transparency and dyeability.
- Surface Quality and Optical Properties: Innovations in protective layers for plastic products have focused on achieving high surface quality, particularly in terms of optical properties. These advancements are crucial for applications where visual clarity and surface durability are paramount.
- Adhesive Properties and Stability: Recent developments in coating compositions have also aimed at improving adhesive properties, glossiness, and storage stability. These improvements ensure that the coatings remain effective over time and under various environmental conditions.
To get detailed scientific explanations of how is plastic made, try Patsnap Eureka.

Learn more
Shock Cords: Versatile Strength for Every Need
Pressure Switches: Small Devices, Big Impact
Unveiling The Lead Screw: Its Mechanism, Benefits, And Beyond