
Every minute, 3 million HDPE plastic bottles are consumed worldwide. Yet, this crucial material goes unnoticed despite its role in modern infrastructure, packaging, and industrial applications. High-Density Polyethylene (HDPE) is revolutionizing industries, making appliance casings lighter, extending waterproof membrane lifespans, and improving the efficiency of electric vehicle (EV) battery cooling systems.
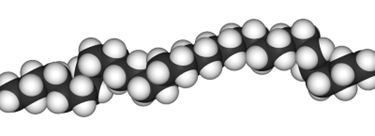
According to Grand View Research’s 2024 report on the European HDPE drum market, the global HDPE industry is projected to grow at a compound annual growth rate (CAGR) of 4.9% from 2025 to 2030. As industries seek sustainable solutions, bio-based and recycled High-Density Polyethylene innovations are shaping the future of materials. This article dives deep into what makes High-Density Polyethyleneunique, its safety concerns, groundbreaking sustainability innovations, and future trends.
What Is HDPE?
High-Density Polyethylene is a thermoplastic polyolefin polymer derived from ethylene polymerization, made possible by Ziegler-Natta catalysts. Its high crystallinity (>90%) gives it exceptional durability and versatility, making it a preferred material across packaging, construction, and automotive industries.
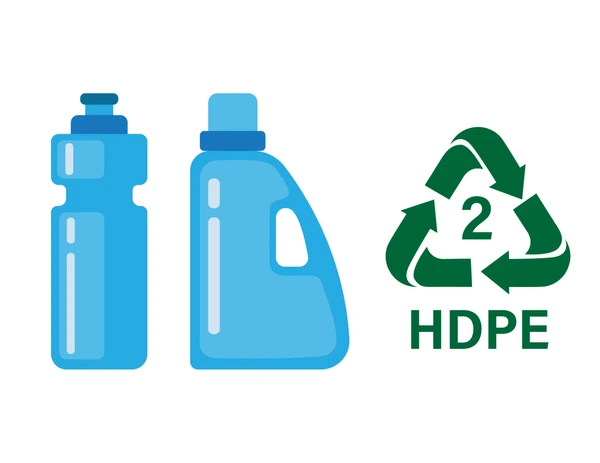
Key Properties of HDPE
- High-Density Defense: With a density of 0.941–0.965 g/cm³, High-Density Polyethylene is resistant to acids, alkalis, salts, and organic solvents, making it ideal for chemical storage and piping.
- Extreme Heat Resistance: Withstanding continuous temperatures up to 120°C and peaking at 180°C (ASTM D638 standard), High-Density Polyethylene performs well in high-temperature industrial settings.
- Cost-Effective Advantage: Compared to metal piping, HDPE installation costs are over 40% lower, and its maintenance cycle is three times longer.
But how do these lab-tested parameters translate into real-world industrial innovation?
Game-Changing Application: EV Battery Cooling Systems
The rise of electric vehicles (EVs) has driven the need for efficient battery cooling solutions. Current systems suffer from high-temperature permeability and bending limitations, which shorten battery life and compromise safety.
A breakthrough solution from Yangzhou Huaguang New Materials integrates silane cross-linked HDPE into multilayer co-extruded cooling pipes, reducing permeability to 2.7 g/(m²·day). This improves resistance to stress cracking, corrosion, and extreme heat, extending EV battery lifespan and safety.
Is HDPE Safe?
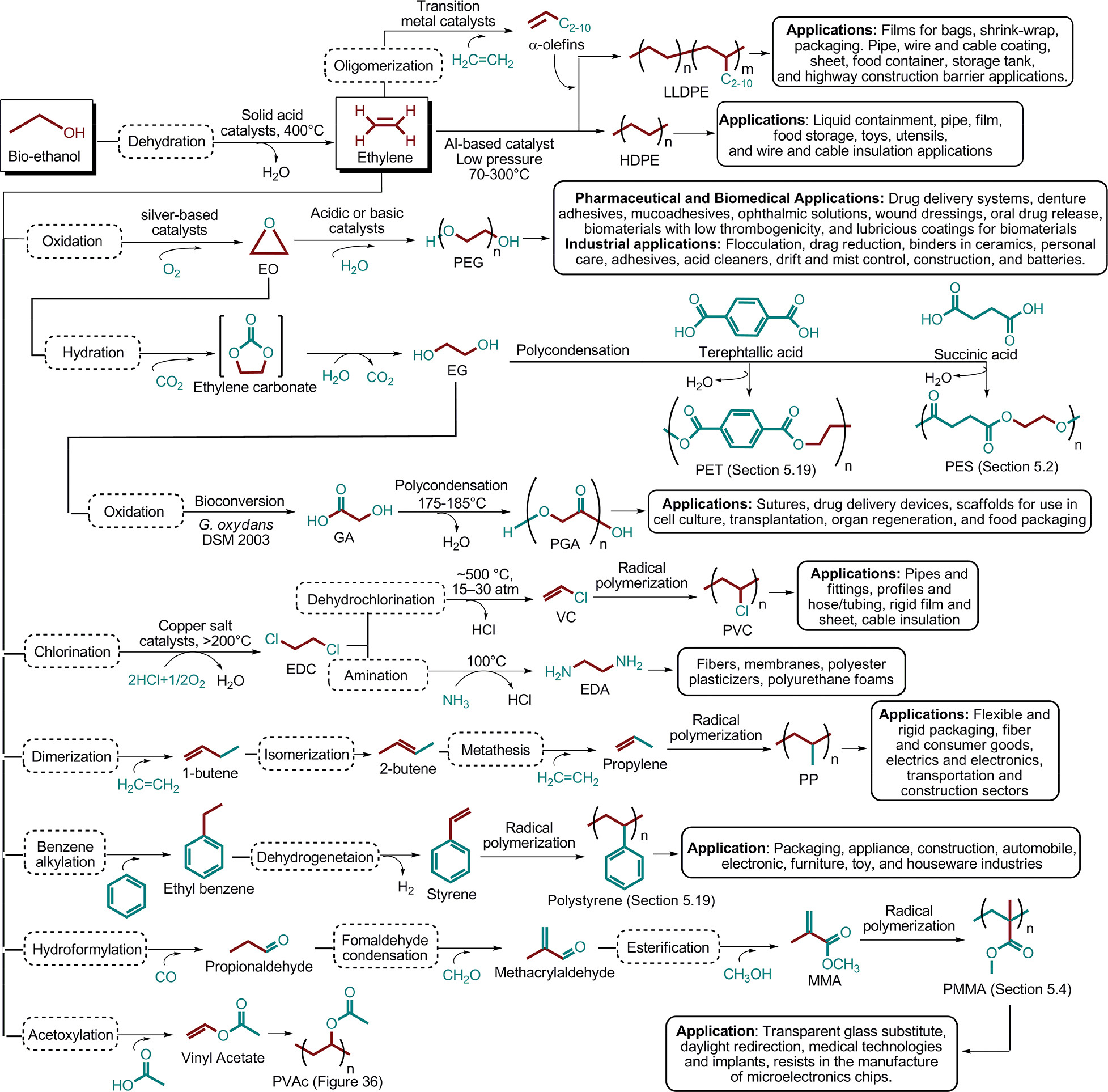
From milk jugs and food containers to microwave-safe trays, High-Density Polyethylene is everywhere in the kitchen. But concerns about plastic safety and potential health risks have sparked debates.
1 HDPE’s Safety in Food Contact
Unlike materials like PVC or polystyrene (PS), which require plasticizers, High-Density Polyethylene is a rigid plastic with superior chemical stability, preventing the leaching of harmful substances such as phthalates.
According to FDA regulations and China’s GB 4806.6-2016 standards, food-grade High-Density Polyethylene must meet strict migration tests:
- Total migration levels must be below 10 mg/dm² in food contact applications.
- Heavy metal content (lead and cadmium) must not exceed 1 ppm and 0.5 ppm, respectively.
But what happens when High-Density Polyethylene is microwaved?
2 Microwaving HDPE: Safe or Risky?
A temperature threshold experiment reveals:
- Safe Zone: Medium heat (700W) for 3 minutes—the container surface stays below 90°C, with no material degradation.
- Risk Zone: High heat (1000W) for 5 minutes with oily foods—localized temperatures reach 135°C, potentially leading to material breakdown.
🔴 Common Mistakes:
❌ Microwaving oily foods in High-Density Polyethylene containers accelerates material degradation.
✅ HDPE is safer than PET when heating food with over 60% water content.
3 Safe Usage Guidelines for HDPE Containers
- Check for Proper Labels: Look for the microwave-safe symbol (ISO 21701 standard).
- Avoid High-Risk Foods: Use glass for oil-rich foods (boiling point >200°C).
- Replace Worn Containers: Scratches deeper than 0.1mm accelerate migration of particles.
HDPE remains one of the safest plastics for food storage—when used correctly.

Sustainability of HDPE
1. Recycled Plastic Packaging: Circular Economy in Action
With sustainability searches surging by 300%, brands like Schwarzkopf are leading the way. Their ginger shampoo bottle uses 30% post-consumer recycled (PCR) HDPE, even overcoming color-matching challenges in mixed-color recycling.
2. The Bio-Based Breakthrough: Sugarcane-Derived HDPE
Braskem, a global leader in bio-based polyolefins, producesHigh-Density Polyethylene from renewable sugarcane sources, cutting carbon emissions by 60–80%.
Key innovation: Lummus’ EtE EverGreen technology, which transforms sugarcane ethanol into ethylene before polymerization into High-Density Polyethylene This model merges Brazil’s agricultural expertise with U.S. process optimizations.
3. Closed-Loop Recycling: Maximizing HDPE Reuse
Dragon Recycling Resources operates a closed-loop recycling system, producing 25,000 tons of food-grade recycled HDPE (rHDPE) annually. Their “collection-cleaning-pelletizing-production” process ensures high-quality bottle-to-bottle recycling.
These innovations are making High-Density Polyethylene a key player in the circular economy.
Application of HDPE
Wondering where HDPE is used? Eureka Technical Q&A provides expert insights into its applications in piping, packaging, and construction, highlighting its durability, chemical resistance, and sustainability for various industries.
Packaging
Manufacturers rely on this material for packaging because it resists moisture, chemicals, and UV radiation. It plays a crucial role in producing bottles, containers, and films for food and beverage storage.
Construction
Lightweight yet durable, this plastic is a top choice for water supply, gas distribution, sewage, and drainage systems. Its longer lifespan makes it more reliable than traditional materials.
Automotive
Automakers use it to manufacture fuel tanks, bumpers, and other components. Its high strength-to-density ratio helps create lightweight, impact-resistant parts that improve vehicle efficiency.
Agriculture
Farmers benefit from its durability in irrigation pipes, greenhouse films, and mulch films. Its strong resistance to chemicals ensures long-term performance in outdoor environments.
Medical
The healthcare industry uses this material for bottles, syringes, and medical devices. Its biocompatibility and chemical resistance make it safe for medical applications.
Consumer Goods
Toys, household items, and packaging materials often contain this plastic due to its durability and impact resistance. Its ability to withstand wear and tear makes it a preferred material for everyday products.
Industrial Applications
In industrial settings, this material strengthens geomembranes used for landfills and wastewater containment. Its chemical resistance ensures long-term stability in harsh environments.
Transportation
Fuel tanks and vehicle components benefit from its lightweight yet strong structure. Its durability makes it an excellent material for transportation-related applications.
Electrical Insulation
Cable jackets and insulation materials rely on its chemical resistance and electrical properties. It enhances safety and durability in electrical applications.
Sports and Recreation
Manufacturers use this plastic to produce sports equipment, including balls, bottles, and other gear. Its impact resistance and durability make it ideal for recreational products.
Application Cases
Product/Project | Technical Outcomes | Application Scenarios |
---|---|---|
HDPE Closure Unilever Plc | Improved durability and processing efficiency for living hinge closure applications | Packaging for consumer goods, especially those requiring durable closures |
HDPE Sheets Dow Global Technologies LLC | Enhanced melt strength and ductility through oxygen contact and antioxidant addition | High-performance HDPE sheets for extrusion and thermoforming applications |
HDPE Packaging Celanese Polymers Holding, Inc. | Reduced water vapor and oxygen transmission rates | Food and beverage packaging requiring extended shelf life |
HDPE Caps and Closures Total Research Corp | Improved rigidity, ESCR, and processability | Beverage bottling, especially for carbonated or still drinks |
Multimodal HDPE Film Borealis AG | Enhanced mechanical and optical properties for recycled content | Film applications requiring high recyclate content and quality |
The Future of HDPE: Key Trends
🌍 Advanced Functionality:
- Multilayer co-extrusion pipes
- Extreme-temperature-resistant composites
- Smart aerospace and new energy applications
🌱 Bio-Based Carbon Neutrality:
- Sugarcane-derived HDPE
- Balancing land use with circular agriculture
♻️ Closed-Loop Recycling:
- Chemical recycling for high-purity HDPE reuse
- Expansion of same-grade recycling initiatives
🚀 Smart High-End Applications:
- IoT-integrated smart piping
- Medical-grade antimicrobial materials
- HDPE in solar and hydrogen energy sectors
Innovations in HDPE Research with Eureka
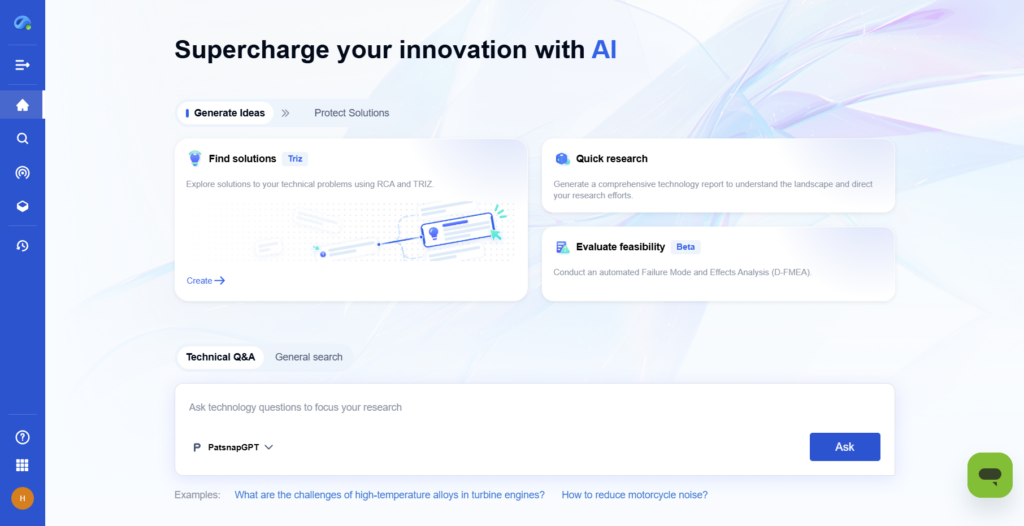
🔍 What is Eureka?
Eureka by PatSnap is an AI-powered research intelligence tool that helps manufacturers and engineers:
✅ Analyze material properties and performance
✅ Discover patents and new HDPE applications
✅ Optimize production processes with real-time data insights
🔍 How Eureka Enhances HDPE Research
✅ Material Performance Optimization – Eureka identifies new HDPE formulations that enhance durability and recyclability.
✅ Sustainability Innovations – AI-driven insights suggest eco-friendly alternatives for HDPE production.
✅ Patent Intelligence – Eureka tracks global advancements in HDPE applications.
📌 Example of Eureka in Action:
A plastic manufacturer using Eureka can:
- Find sustainable additives to improve HDPE recyclability
- Analyze patents on high-strength HDPE for industrial applications
- Optimize HDPE formulations for lightweight yet durable packaging
Conclusion: HDPE as a Game-Changer for Sustainability
Far from being an environmental villain, High-Density Polyethylene is the unsung hero of modern industry. Its dense molecular structure, durability, and safety make it an essential material in countless applications.
Thanks to innovations in recycled packaging, bio-based alternatives, and closed-loop recycling, High-Density Polyethylene is at the forefront of the low-carbon revolution. As the world shifts toward sustainability and resource efficiency, High-Density Polyethylene will play a key role in reshaping industries and reducing environmental impact.
Want to learn more about how HDPE is transforming the world? Join the conversation on Eureka Tech-Seek for expert insights and the latest industry trends.
To get detailed scientific explanations of HDPE, try Patsnap Eureka.
