
Technical Background and Objectives
Background
The field of ‘butt weld’ and the technical effect of ‘easy butt welding’ have shown a consistent upward trend in patent applications over the years, indicating growing interest and research efforts. This trend reflects the increasing demand and importance of developing technologies that facilitate easy butt welding processes. However, related literature publications present a different pattern with a relatively low and fluctuating number, suggesting that while there is significant patent activity, academic research may not be keeping pace with the industry’s interest and development efforts.
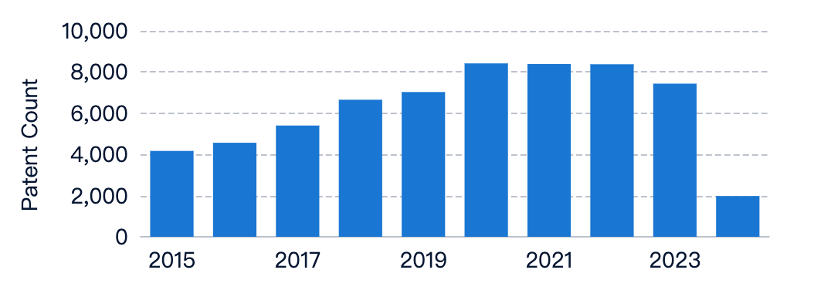
Objectives
The primary objective is to develop innovative and efficient butt welding techniques that simplify the process, reduce costs, and improve overall weld quality. The goal is to provide viable solutions readily adopted by various industries such as construction, manufacturing, and infrastructure development, where butt welding is extensively utilized.
To get a detailed scientific explanations of Butt Welding, try Eureka.
Technical Current Status Analysis
Butt Welding Overview
Butt welding is widely used in various industries including construction, shipbuilding, automotive, and pipeline fabrication. It involves fusing two metal pieces by melting their ends together, creating a strong and seamless joint. Achieving easy and reliable butt welding can be challenging due to several factors.
Applications and Impact:
- Construction: Joining structural steel components such as beams, columns, and trusses.
- Shipbuilding: Joining steel plates used in constructing ship hulls, decks, and other components.
- Automotive: Joining components such as frame members, exhaust systems, and fuel tanks.
- Pipeline Fabrication: Joining pipe sections used in transporting oil, gas, and other fluids.
Technical Characteristics and Challenges:
- Material Properties: Chemical composition, microstructure, and mechanical properties impact weldability.
- Joint Preparation: Precise alignment, gap control, and surface preparation are crucial.
- Welding Parameters: Optimizing current, voltage, travel speed, and heat input is essential.
- Welding Position: Different welding positions affect the ease and quality of welding.
- Preheating and Interpass Temperature Control: Necessary for preventing defects like hydrogen-induced cracking.
- Welding Technique and Operator Skill: Proper technique and skilled operators are vital.
Technological Paths:
- Advanced Welding Processes: Implementing processes like friction stir welding, laser beam welding, or hybrid welding techniques.
- Automated and Robotic Welding Systems: Enhancing consistency and repeatability.
- Adaptive Welding Control: Developing systems that adjust parameters in real-time.
- Computational Modeling and Simulation: Optimizing joint designs and welding parameters.
- Advanced Materials and Filler Metals: Utilizing materials with improved weldability.
- Welding Procedure Development and Qualification: Establishing optimized procedures.
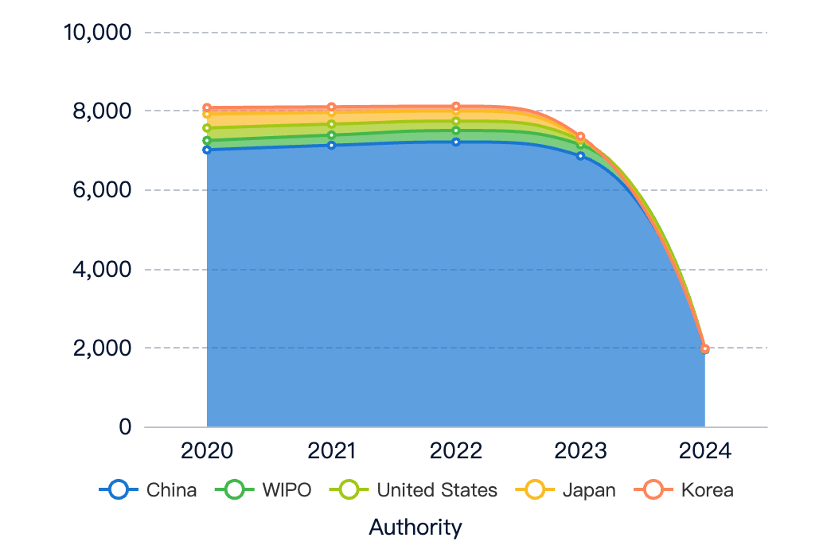
Research Content
Research Objectives
Develop innovative techniques and methodologies to simplify butt welding processes, reduce costs, and improve weld quality.
Research Direction and Focus
Weld Joint Preparation and Design
- Optimize the design and preparation of butt weld joints, exploring novel joint geometries, surface treatments, and material combinations.
- Investigate joint fit-up, gap tolerance, and material compatibility.
Welding Process Optimization
- Simplify procedures and reduce complexity through alternative welding methods like friction welding, laser welding, or hybrid techniques.
- Integrate advanced control systems, automation, and real-time monitoring.
Materials and Consumables
- Select and develop advanced filler materials, flux compositions, and shielding gases.
- Explore alternative materials or alloys with improved weldability.
Cost and Productivity Analysis
- Conduct comprehensive cost and productivity analyses to ensure economic viability.
- Evaluate material costs, energy consumption, labor requirements, and process cycle times.
Validation and Testing
- Implement rigorous validation and testing protocols, including laboratory-scale testing, simulations, and real-world trials.
- Employ quality control measures and non-destructive testing methods.
Technical Development Roadmap
Key Areas of Advancement
- Weld Joint Design and Optimization: Narrow groove designs, dissimilar metal joints, and joint strength modeling and simulation.
- Weld Process Control and Monitoring: Adaptive control systems, real-time defect detection, and process data analytics.
- Advanced Butt Welding Techniques: Friction stir welding of high-strength alloys, laser welding of thick sections, and hybrid welding processes.
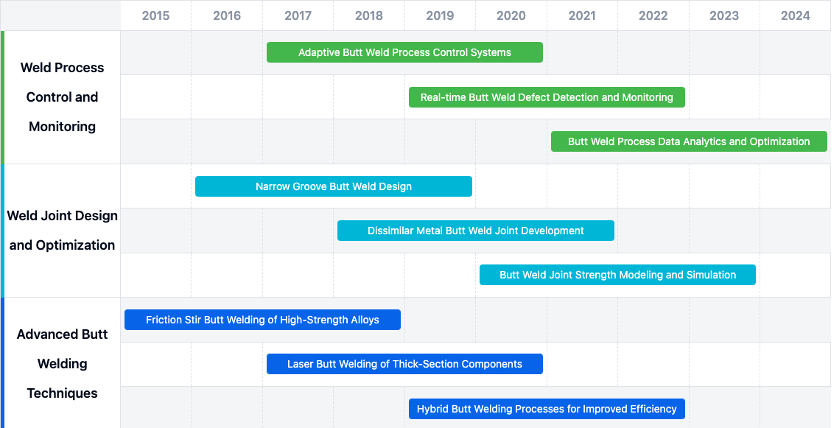
Main Player Analysis
Key Players and Focus
- Hitachi Ltd.: 523 patents focusing on advanced welding techniques, equipment, and processes.
- Osaka University: Research on residual stress analysis, stress intensity factors, and laser welding of aluminum alloys.
- Honda Motor Co. Ltd.: 505 patents on advanced welding techniques and processes for the automotive industry.
- NIPPON STEEL CORP.: 1101 patents on advanced welding techniques, materials, and processes.
- Nanchang Hangkong University: Research on friction stir welding of dissimilar materials and laser welding of shape memory alloys.
Current Technical Solution Overview
Butt Welding Methods and Techniques
- Methods for Pipes and Tubes: Resistance welding, laser welding, and flux-cored wires.
- Methods for Steel Plates and Components: Techniques for heavy-gauge steel, low-alloy steels, and high-strength steels.
- Auxiliary Devices and Techniques: Shielding devices, visualization and correction methods, and finishing techniques.
- Hybrid and Specialized Methods: Combining different welding processes and techniques for specific applications.
- Inspection and Non-Destructive Testing: Methods to ensure weld quality without causing damage.
Butt Weld Joint Structures and Configurations
- Structures for Pipes or Tubes: Designs to facilitate alignment and positioning.
- Structural Components: Frames, beams, or support structures with reinforcement or additional features.
- Alignment and Positioning Devices: Ensuring proper fit-up and gap control.
- Reinforcement and Repair Techniques: Methods for strengthening or repairing joints.
Butt Welding Equipment and Apparatus
- Equipment for Pipes or Tubes: Devices for alignment, heating, and supporting joints.
- Methods and Processes: Resistance, flash, laser, and arc welding techniques.
- Specialized Equipment: For specific applications like contact rails and pipelines.
- Joint Preparation and Inspection: Aligning, visualizing, and inspecting joints.
- Accessories and Auxiliary Components: Weld supports, guides, clamping devices, and cooling mechanisms.
Butt Weld Joint Reinforcement and Correction
- Reinforcement Methods: Adding elements to distribute stress and prevent cracks.
- Correction Techniques: Adjusting joints to improve quality and alignment.
- Joint Designs: Optimizing geometry for different applications.
- Specialized Methods and Equipment: Improving weld quality and efficiency.
- Applications and Structures: For reinforcement cages, pipelines, and structural components.
Butt Welding of Specific Materials or Components
- Methods for Specific Materials: Techniques for thin sheets, coils, stainless steel, clad steel, and laminated items.
- Apparatus and Equipment: Devices tailored for butt welding operations.
- Methods for Tubes and Pipes: Ensuring uniform and strong weld joints.
- Techniques for Thick Materials: Addressing challenges in welding thick components.
- Laser Butt Welding: High-energy beams for precise and deep penetration welds.
Key Patent Interpretation
Patent Highlights
Patent 1: Automatic Coating and Brazing Butt Welding Equipment for Aluminum Pot
- Core Invention Points:
- Fully automated and intelligent process replacing manual operations.
- Secondary automatic brazing and powder dropping operations to ensure product quality.
- Standardized and uniform products with higher quality and reduced labor costs and errors.
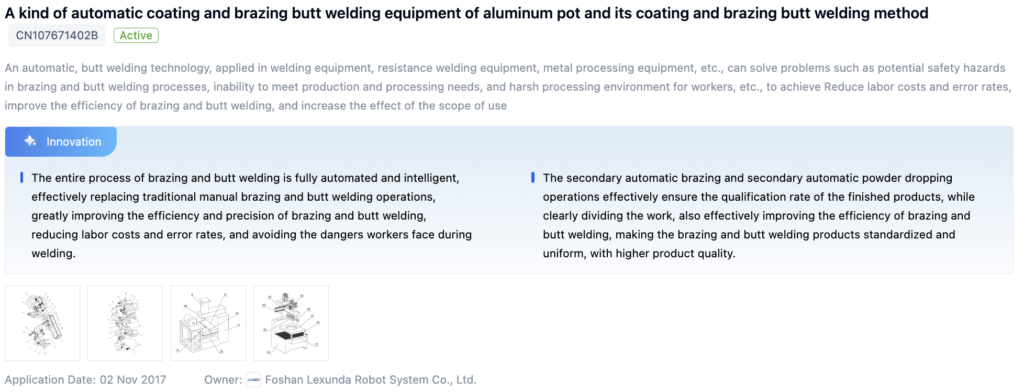
Patent 2: Automatic Butt Welding Equipment for Motor Rotor Commutator
- Core Invention Points:
- Integrated conveyor belts, manipulators, butt welding assembly, cooling assembly, and detection components for efficient welding.
- Automatic adjustment of welding rod length based on rotor diameter.
- Synchronous welding for even numbers of wire hooks to improve efficiency.
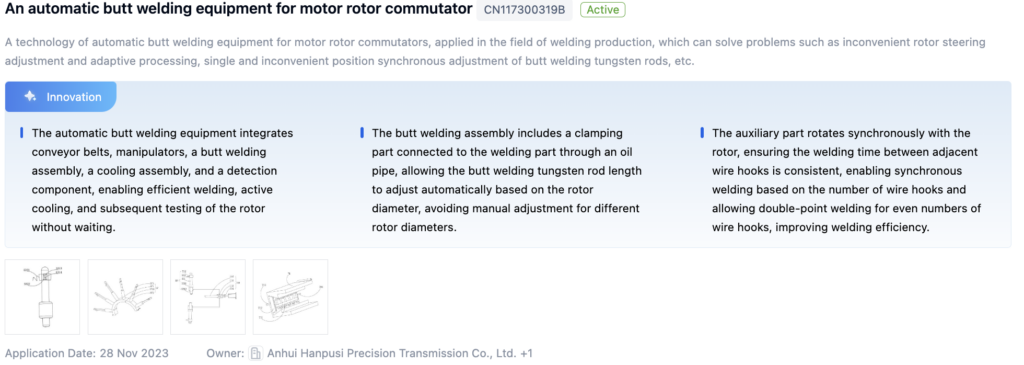
Patent 3: Electron Beam Welding Method for Locking Bottom Butt Joints of Large Size Thin-Walled Titanium Alloy Storage Tanks
- Core Invention Points:
- Optimized welding sequence to reduce deformation.
- Adjustable welding methods based on structural characteristics.
- Segmental tack welding and multi-pass welding to improve weld strength and inspection pass rate.

Possible Research Directions
- Butt Welding Methods and Techniques: Exploring advanced methods to improve quality and efficiency.
- Joint Design and Configurations: Optimizing designs for better structural integrity and properties.
- Quality Control and Monitoring: Implementing advanced monitoring techniques.
- Reinforcement and Strengthening: Enhancing joint strength and durability.
- Preparation and Tooling: Developing efficient preparation and tooling methods.
If you want an in-depth research or a technical report, you can always get what you want in Eureka Technical Research. Try now!
