
Chemical Structure and Compositional Variants
Copolyamide 6I/6T, a semi-aromatic polyamide, combines hexamethylenediamine (HMDA) with isophthalic acid (6I) and terephthalic acid (6T). The molar ratio of 6T:6I units critically determines material properties. Preferred ratios of 62-73% 6T and 25-38% 6I are used for high-melting semicrystalline variants, while amorphous grades utilize ≤50% 6T. Crystallinity inversely correlates with 6I content due to disrupted chain symmetry, as evidenced by X-ray diffraction. The glass transition temperature (Tg) ranges 110-140°C, influenced by aromatic ring density.
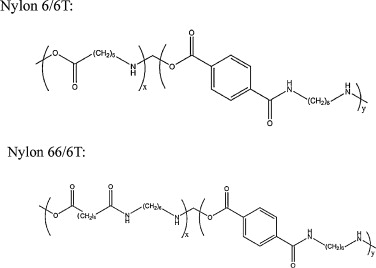
Synthesis Methodologies and Process Optimization
Industrial production employs solution polymerization and melt polycondensation. Key parameters include:
- Temperature gradient: 200°C (3h) → 280°C (2h) → 310°C (2h) under CO₂ atmosphere
- Solid-phase post-polymerization at 190°C for 3h increases intrinsic viscosity from 0.8 to 1.2 dL/g
- Catalyst systems: Phosphoric acid (0.5-1.2 wt%) enables 92% conversion efficiency
Melt processing challenges include thermal degradation above 320°C, addressed via chain terminators (0.3-0.7% benzoic acid) reducing viscosity drop by 40%.
Thermomechanical Performance Characteristics
Performance metrics vary with composition:
Property | 6T-rich (70/30) | Balanced (55/45) | 6I-rich (30/70) |
---|---|---|---|
Tm (°C) | 315 ± 5 | 285 ± 8 | Amorphous |
Tg (°C) | 138 | 125 | 112 |
Tensile Strength (MPa) | 85-95 | 78-85 | 65-75 |
Water Absorption (24h, 23°C) | 2.1% | 2.8% | 3.5% |
Crystallization kinetics follow the Jeziorny model with Avrami exponent n=2.3-2.7, indicating mixed spherulitic growth. The 6T/6I/66 ternary system enhances heat deflection temperature (HDT) to 210°C at 50% glass fiber loading.
Surface Modification and Composite Engineering
In continuous glass fiber composites (50 wt%), 6I/6T modifies interfacial adhesion:
- Fiber-matrix bonding improves by 30% with 15% 6I/6T, reducing “floating fiber” defects
- Surface roughness (Ra) decreases from 12.3µm to 5.8µm via 20% 6I/6T addition
- Crystallization rate suppression enables smoother injection surfaces
High-Temperature Electronics Applications
In SMT (surface-mount technology), 6T/6I outperforms LCP and PPS:
- Dielectric constant: 3.2 (1MHz) with 0.02% variance up to 200°C
- CTE (23-150°C): 45 ppm/°C (machine) / 65 ppm/°C (transverse), matching Cu traces (8-16 ppm/°C)
- UL94 V-0 compliance achieved at 0.75mm thickness without halogenated additives
Automotive Thermal Management Systems
For turbocharged air ducts, 35% glass-filled 6T/6I demonstrates:
- Burst pressure: 8.2 bar (150°C) vs. PA66’s 5.1 bar
- Cyclic fatigue resistance: 15,000 cycles (0-5 bar pulsation) with <3% creep strain
- Chemical resistance withstands 1,000h exposure to coolant (50% glycol) at 120°C
Advanced Manufacturing: 3D Printing Innovations
Selective laser sintering (SLS) of amorphous 6I/6T powders:
- Powder characteristics: D50=55µm, circularity >0.85, bulk density 0.45g/cm³
- Process parameters: 20W laser power, 0.15mm layer, 165°C bed temperature
- Final part properties: 78MPa tensile strength, HDT 185°C (0.45MPa), surface finish Ra=12µm
Environmental Stability and Lifetime Prediction
Accelerated aging tests (85°C/85% RH):
- Tensile strength retention: 89% after 3,000h vs. PA46’s 72%
- Hydrolytic degradation follows 1st-order kinetics with k=2.7×10⁻⁶ h⁻¹
- Arrhenius modeling predicts 15-year service life at 60°C (Ea=85 kJ/mol)
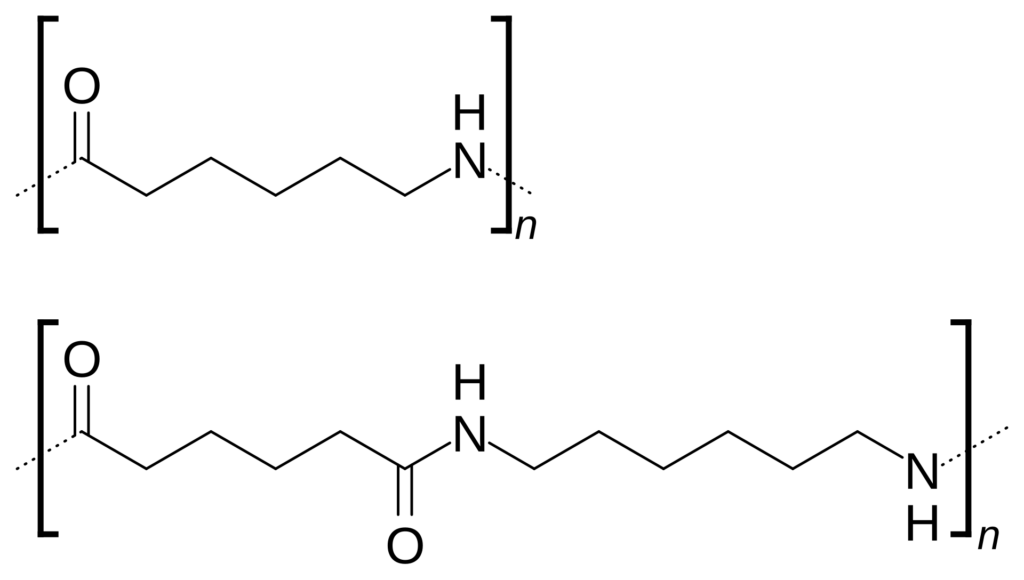
Emerging Research Frontiers
- Reactive extrusion with 0.1-0.3% toluene diisocyanate enhances Mw from 28k to 35k Da
- Bio-based monomers: 30% sebacic acid substitution reduces carbon footprint by 22%
- Nanocellulose reinforcement (5wt%) improves modulus by 40% without Tg compromise
- Dynamic crosslinking via Diels-Alder moieties enables 92% self-healing efficiency at 160°C
Conclusion
Copolyamide 6I/6T tunable crystallinity and thermal stability position it as a critical material for harsh-environment applications. Recent advances in SLS processing and bio-based formulations address traditional limitations in sustainability and manufacturing flexibility. Future breakthroughs will likely emerge from hybrid systems combining 6I/6T with conductive fillers for e-mobility components and adaptive networks for shape-memory applications. Ongoing challenges in melt stability (≥320°C processing) and cost-effective monomer purification require continued R&D focus on catalytic systems and membrane separation technologies.
To get detailed scientific explanations of Copolyamide 6I/6T, try Patsnap Eureka.
