
Introduction: Hot Rolled vs Cold Rolled Steel
Hot rolled steel and cold rolled steel are two widely used materials, each with unique properties suited to different applications. While hot rolled steel excels in affordability and heavy-duty use, cold rolled steel offers superior precision and strength. Understanding their differences ensures you select the right steel for your project.
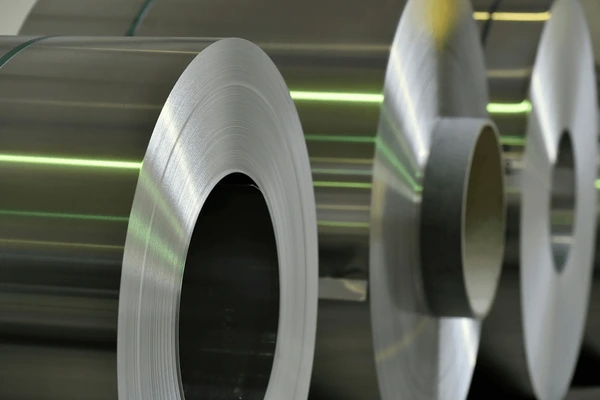
What Is Hot Rolled Steel?
Hot rolled steel is produced by rolling a steel billet at high temperatures, typically above the recrystallization temperature of austenite (around 850-950°C) 258. The hot rolling process involves the following steps:
- Heating the steel billet to the desired temperature in a furnace.
- Rough rolling the heated billet to reduce its thickness.
- Finish rolling the rough-rolled material through a series of rolling stands to achieve the final desired shape and dimensions.
- Cooling the hot-rolled steel on a run-out table or by water quenching (e.g., TEMPCORE® process).
- Coiling the cooled steel at a temperature of around 600-700°C.
The high temperatures during hot rolling result in a microstructure with lower strength and good ductility, making hot rolled steel suitable for applications requiring further cold working or heat treatment. Hot rolled steel typically has a ferritic-pearlitic microstructure.
What Is Cold Rolled Steel?
Cold rolled steel is produced by further rolling the hot rolled steel at room temperature, resulting in significant strain hardening and improved mechanical properties 1611. The cold rolling process involves:
- Pickling the hot rolled steel coil to remove surface oxides.
- Cold rolling the pickled steel through a series of rolling stands at room temperature, reducing the thickness by up to 90%.
- Annealing the cold rolled steel to relieve internal stresses and achieve the desired microstructure and properties.
Cold rolling increases the yield strength, tensile strength, and hardness of the steel, while reducing its ductility. The final microstructure and properties of cold rolled steel can be tailored by adjusting the cold rolling reduction ratio and annealing parameters.
Cold rolled steel exhibits superior surface finish, dimensional accuracy, and mechanical properties compared to hot rolled steel, making it suitable for applications requiring high strength, formability, and surface quality, such as automotive body panels, appliances, and construction materials.
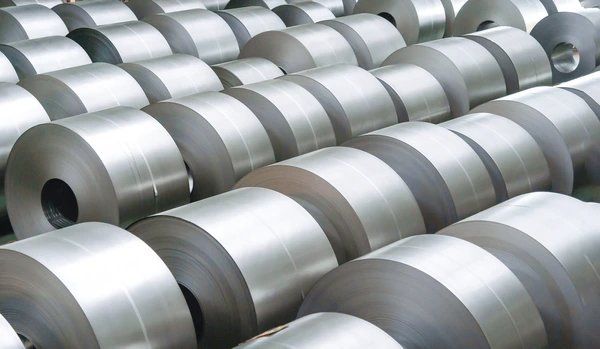
Key Differences Between Hot Rolled and Cold Rolled Steel
Production Process
Hot rolled steel is produced by heating steel billets or slabs to high temperatures (above 927°C) and then rolling them through a series of rollers to achieve the desired shape and thickness. This process allows for significant deformation and reshaping of the steel. Cold rolled steel, on the other hand, starts with hot rolled steel coils or sheets and further reduces the thickness and improves the surface finish by rolling at room temperature.
Microstructure and Properties
The high temperatures involved in hot rolling result in a ferrite-pearlite microstructure with lower strength and higher ductility. Cold rolling introduces strain hardening, increasing the yield strength and tensile strength while reducing ductility. The cold rolled steel microstructure is typically finer and more uniform compared to hot rolled steel.
Surface Quality
Hot rolled steel has a rougher surface due to the formation of oxide scales during the high-temperature rolling process. Cold rolled steel has a much smoother and more uniform surface finish, making it suitable for applications requiring a high-quality surface appearance.
Dimensional Accuracy
Cold rolled steel has better dimensional accuracy and tighter tolerances compared to hot rolled steel due to the lower temperatures and controlled deformation during the rolling process. This makes cold rolled steel more suitable for applications requiring precise dimensions and tight tolerances.
Applications
Hot rolled steel is commonly used in construction, machinery, and structural applications where high strength is not a primary requirement. Cold rolled steel is preferred for applications that require higher strength, better surface finish, and tighter dimensional tolerances, such as automotive body panels, appliances, and precision components.
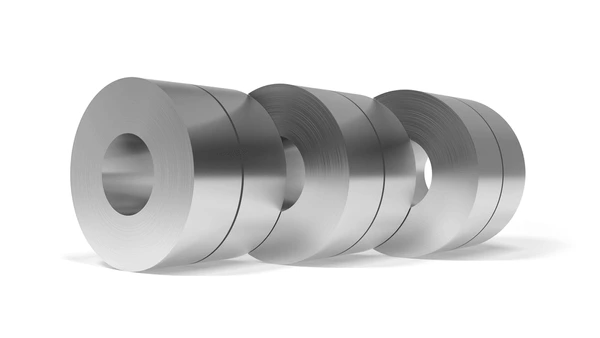
Conclusion: Which Should You Choose?
Hot rolled vs cold rolled steel boils down to your project’s needs. For cost-effective, large-scale applications, hot rolled steel is ideal. If precision, strength, and surface finish are critical, cold rolled steel is the better choice. Make an informed decision to ensure the success of your project.
FAQs
- What is the main difference between hot rolled and cold rolled steel?
The primary difference lies in the processing temperature: hot rolled steel is processed at high temperatures, while cold rolled steel undergoes further processing at room temperature for precision. - Is cold rolled steel stronger than hot rolled steel?
Yes, cold rolled steel is stronger due to additional processing, which increases its hardness and tensile strength. - Can hot rolled steel be used for precise applications?
It’s possible but uncommon, as its rough surface and loose tolerances make it less suitable for precision applications. - Why is cold rolled steel more expensive?
Cold rolling requires additional processing, resulting in higher manufacturing costs and improved quality. - Which type of steel is best for heavy-duty projects?
Hot rolled steel is preferred for heavy-duty applications where surface finish and precision are less important.
To get detailed scientific explanations of cold rolled steel, try Patsnap Eureka.
