
Introduction
Choosing the right material is a crucial step in achieving the best results for your 3D printing projects. ASA vs. ABS are two popular thermoplastics, each offering unique advantages that cater to different needs. While ABS is known for its strength, durability, and affordability, ASA stands out for its excellent weather resistance and UV stability. Whether you’re creating functional parts, prototypes, or outdoor applications, understanding the differences between these materials can help you make the best choice. This article compares ASA and ABS, exploring their properties, benefits, and ideal use cases to guide you in selecting the right material for your next project.
Key Properties of ASA Filament
1. Chemical Composition
ASA is a three-component copolymer made of acrylonitrile, styrene, and acrylic esters. This unique blend provides a well-balanced combination of rigidity, toughness, and visual appeal, making it versatile for various applications.
2. Key Properties of ASA
- Impact Resistance: ASA delivers excellent impact resistance, ensuring durability for parts exposed to mechanical stress. This toughness makes it ideal for functional 3D-printed components.
- UV Stability: ASA stands out for its superior resistance to UV degradation, maintaining its performance and appearance in outdoor environments. This property makes it a top choice for projects exposed to sunlight.
- Chemical Resistance: With its ability to resist exposure to various chemicals, ASA remains stable in challenging environments, making it reliable for industrial and chemical applications.
- Dimensional Stability: ASA maintains its shape and dimensions over time, ensuring precision and reliability for 3D prints where accuracy is critical.
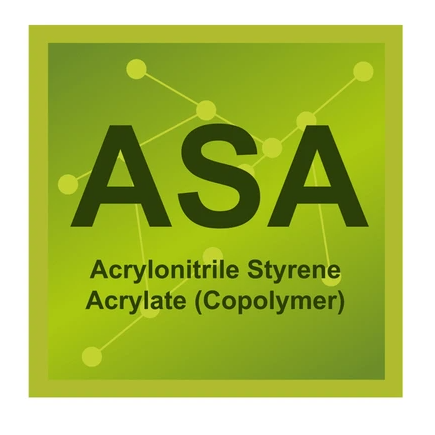
Key Properties of ABS Filament
ABS, or Acrylonitrile Butadiene Styrene, is a widely used thermoplastic polymer in 3D printing, particularly with Fused Deposition Modeling (FDM) technology. Its combination of durability, heat resistance, and ease of use makes it a favorite for both prototyping and production.
Key Characteristics of ABS
- Mechanical Properties
- ABS offers high impact strength and toughness, allowing it to withstand significant mechanical stress.
- Its good tensile and flexural strength makes it ideal for creating durable, long-lasting parts.
- Thermal Properties
- ABS exhibits excellent thermal stability with a glass transition temperature (Tg) of around 105°C.
- This heat resistance makes it suitable for applications in outdoor or high-temperature environments.
- Printability
- ABS flows smoothly during extrusion, ensuring high-quality prints with minimal defects.
- It adheres well to the build platform, reducing warping and improving overall print consistency.
- Aesthetic Properties
- ABS produces parts with a smooth, glossy finish, perfect for applications requiring a polished appearance.
- Available in a wide range of colors, ABS adds versatility to creative and functional designs.
- Cost Effectiveness
- ABS is more affordable compared to advanced materials like polycarbonate or nylon.
- This cost efficiency makes it a practical choice for various industries and applications.
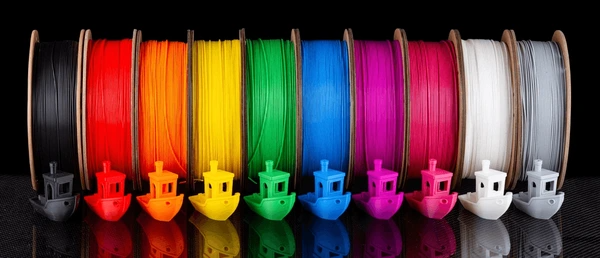
ASA vs ABS: Durability and Weather Resistance
1. Composition and Structure
- ASA: ASA is made from acrylonitrile, styrene, and acrylate. The acrylate component replaces butadiene, eliminating double bonds and increasing resistance to UV degradation.
- ABS: ABS consists of acrylonitrile, butadiene, and styrene. However, the double bonds in butadiene make ABS more vulnerable to oxidative degradation under UV exposure.
2. Durability and Weather Resistance
- ASA
- Weather Resistance: ASA offers superior weather resistance, performing 10 times better than ABS in outdoor conditions.
- Color Stability: It retains color and mechanical properties, even after prolonged outdoor exposure. This makes it ideal for automotive parts and outdoor furniture.
- UV Stability: ASA resists UV degradation effectively, maintaining its strength and durability when exposed to sunlight.
- ABS
- Weather Limitations: ABS has limited resistance to UV, heat, and oxygen, which causes degradation in outdoor environments.
- Color Changes: Prolonged outdoor exposure often results in yellowing and a loss of mechanical properties.
- Improved with Additives: Additives like light stabilizers can enhance weather resistance, but ABS still falls short of ASA’s performance.
3. Common Applications
- ASA Applications: ASA is widely used in outdoor applications like automotive exterior parts, construction materials, sports equipment, and consumer goods. Its weather resistance and durability make it a preferred choice for outdoor use.
- ABS Applications: ABS is more suited for indoor applications, including consumer electronics, appliances, and toys. While protective coatings or color stabilizers can make it usable outdoors, it is less reliable in harsh conditions compared to ASA.
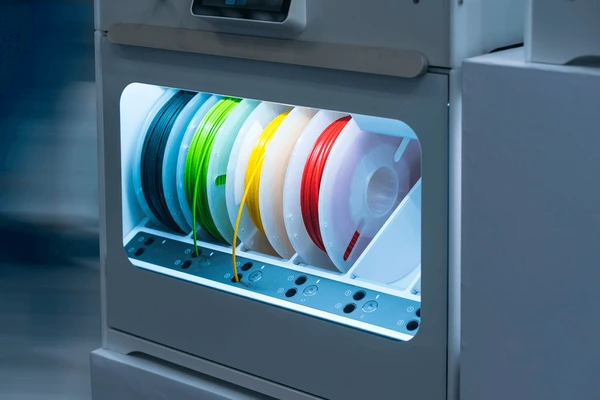
Choosing the Right Material for Your Project
Consider Environmental Conditions
- Outdoor Applications: If your project will be exposed to sunlight, UV light, or harsh weather, ASA is the better choice. Its superior weather resistance and UV stability make it perfect for long-term outdoor use.
- Indoor Applications: On the other hand, ABS works well for indoor projects where environmental exposure is minimal. It performs reliably in controlled conditions, making it ideal for general-purpose applications.
Assess Mechanical and Aesthetic Requirements
- Durability and Strength: When durability is a priority, ASA offers exceptional toughness and the ability to withstand stress and environmental wear. For projects requiring functional parts that face mechanical challenges, ASA stands out.
- Aesthetic Needs: Furthermore, ASA maintains its color stability over time, which is crucial for projects where appearance matters. While ABS delivers a smooth, glossy finish, it may yellow when exposed to UV light, making it less suitable for applications demanding long-term visual appeal.
Evaluate Cost and Processing Needs
- Cost-Effectiveness: If budget is a concern, ABS is a more affordable option. Its lower cost and ease of processing make it practical for cost-sensitive projects.
- Processing Requirements: Both ASA and ABS are compatible with standard 3D printing methods. However, ASA may require slightly more expertise to achieve optimal results, especially in complex designs.
Match the Material to the Application
- ASA Applications: Thanks to its durability and UV resistance, ASA is ideal for outdoor furniture, automotive parts, sports equipment, and construction materials. Its superior performance in challenging environments makes it a top choice for outdoor projects.
- ABS Applications: ABS is best for consumer electronics, toys, and appliances that don’t face harsh conditions. While not as weather-resistant as ASA, it excels in indoor settings where environmental stress is minimal.
To get detailed scientific explanations of ASA vs. ABS, try Patsnap Eureka.
